Kal Tire transforms mining tire waste into new resources
Inside Kal Tire’s innovative OTR tire recycling facility in Chile
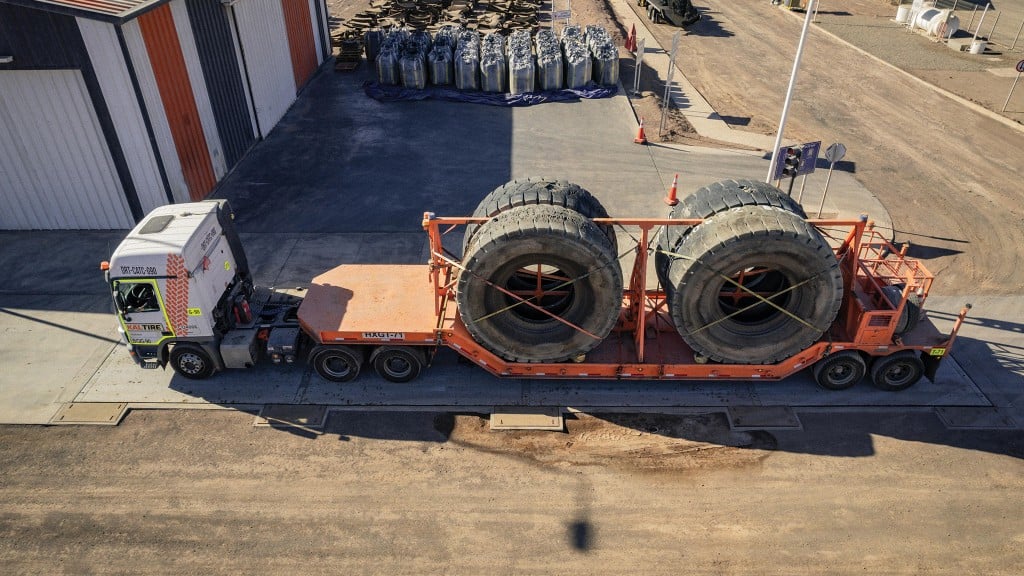
In Chile, Kal Tire's innovative recycling facility provides a crucial solution to one of the mining industry's critical and complex areas for sustainable waste management: the sustainable disposal of ultra-class mining tires.
For decades, these massive tires have accumulated at mining sites, with limited options for responsible disposal. Kal Tire's advanced thermal conversion process transforms this long-standing issue into an opportunity for resource recovery and environmental progress.
In 2021, Kal Tire opened its first tire recycling facility in northern Chile with an innovative solution focused on converting massive mining tires into reusable resources. Using proprietary technology, the facility is setting a new industry standard for sustainable tire recycling.
Why Chile?
Chile's prominence in the mining industry made it an ideal location for Kal Tire's first off-the-road (OTR) tire recycling facility. As the world's largest copper producer (23 percent of the global copper output), Chile's mines have operated at scale for decades. Over the years, these mines have accumulated thousands of scrap mining tires without a viable recycling solution.
According to Terry Galvin, vice president of recycling services with Kal Tire's Mining Tire Group, Chile's progressive mining tire disposal legislation was a key factor in Kal Tire's decision to build the facility. "Chile's mining legislation is structured so that there's a progressive requirement for 25 percent of giant mining tires to be recycled starting in 2023, 75 percent in 2027, and 100 percent by 2030."
Kal Tire's facility is located in Antofagasta, strategically positioned near some of Chile's largest copper mines. "We're within a couple of hundred kilometres of most major mining operations," says Galvin. "That proximity is key to ensuring efficient tire transportation and logistics." It is also key to ensuring that the environmental benefits of tire recycling in the region are not undermined by the process and logistics.
Building the facility came with unique challenges. Chile's stringent environmental regulations required Kal Tire to meet the highest global standards for emissions control, water usage, and overall environmental impact.
The plant also had to be engineered to withstand significant seismic activity. "We designed the plant to be resilient in the event of the worst of earthquakes," says Galvin. That meant meticulous engineering and ensuring safety protocols exceeded international requirements.
Thermal conversion process turns waste into resources
Kal Tire's recycling solution hinges on a proprietary thermal conversion process — a method that safely transforms mining tires into reusable materials without harmful emissions.
"Thermal conversion is essentially heat and friction in the absence of oxygen," explains Galvin. "This creates a reaction that breaks down the tires into their core components — gas, alternative fuel, steel, and carbon ash."
The recycling process is meticulously designed to ensure maximum resource recovery at every stage:
Tire collection & delivery Mining companies transfer scrap tires to the facility, often utilizing backhaul trips to minimize transportation costs by leveraging existing logistics.
Weighing & identification Each tire is weighed and assigned a serial number to ensure complete traceability throughout the chain of custody.
Cleaning & sizing The tires are cleaned to remove debris and contaminants, then cut into smaller segments to fit inside the reactors.
Thermal conversion process The tire segments are heated in a vacuum chamber with no oxygen, initiating the pyrolysis process. As the tires decompose, they release synthetic gas which is captured and reused to sustain the reactor's heating system.
Output recovery The thermal conversion process yields four primary outputs for each 4+ ton tire:
• 6,500 litres of alternative fuel — used as an industrial energy source or chemical feedstock.
• 4,000 kilograms of clean, high-tensile steel — ready for reuse.
• 8,000 kilograms of carbon ash — a fine, powdery substance that is further refined to create high-quality recovered carbon black.
• Synthetic gas — captured and reused to power the facility for up to seven hours.
"We designed the process to be completely self-sustaining," Galvin says. "The synthetic gas is an integral part of the operation. By harnessing that gas to fuel the plant, we've created a closed-loop system that minimizes environmental impact."
Refining carbon black for maximum value
One of the most significant innovations to emerge from Kal Tire's Chile facility is proprietary refining technology to produce recovered carbon black (rCB). This material, derived from carbon ash during the thermal conversion process, is further refined to meet the high quality standards of tire manufacturers and other industrial buyers.
Kal Tire partnered with a Canadian engineering firm to develop a proprietary refining system designed to purify and upgrade carbon ash. The process involves:
Heating The carbon ash is heated to remove impurities.
Milling The refined carbon is milled to achieve the desired particle size.
Pelletizing The carbon black is formed into pellets to meet industrial specifications.
Cooling The refined carbon is cooled and packaged for sale.
The result is a high-quality rCB product that is growing in demand from Tier 1 tire manufacturers and compounders.
Environmental impact and sustainability
Environmental responsibility is at the core of Kal Tire's operations. The facility is certified under the International Sustainability and Carbon Certification (ISCC) PLUS program, ensuring that all recycled materials are derived from waste products and promoting a circular economy.
"The ISCC PLUS certification is important because it provides our customers with transparency," Galvin explains. "It shows that the products we supply are sustainable and traceable."
Beyond emissions reduction, Kal Tire employs strategies to minimize its environmental footprint at every stage of the recycling process, from managing waste streams to reducing water consumption and optimizing energy efficiency.
Scalability and expansion
With the success of its Chilean plant, Kal Tire is actively exploring expansion opportunities in other mining regions. Kal Tire's scalable plant design makes future expansion practical and efficient. According to Galvin, there's growing interest from mining jurisdictions across North America, Australia, and Africa.
"There's a lot of appetite to look for solutions surrounding [mining tire recycling]. They're big operations and, eventually, they'll have to deal with mine closures," says Galvin. "So a more progressive reclamation mentality is starting to take hold."
The future of mining tire recycling
Looking ahead, Galvin believes that thermal conversion will play an increasingly vital role in managing mining tire waste. "This technology has the potential to change how mines around the world deal with their tire waste."
Kal Tire's forward-thinking approach to mining tire recycling reflects the company's broader commitment to sustainability. "I think companies are more sensitive to it, communities are more sensitive to the demands of doing the right thing. There is going to be a lot more focus on cleaning up and not leaving a mess behind," says Galvin. "I think the notion and the ability to progressively reclaim is going to become more and more prevalent as technologies improve."