Polypropylene recycling turns curbside waste into high-quality resin
PureCycle dissolution technology and Machinex sorting systems are redefining PP recycling
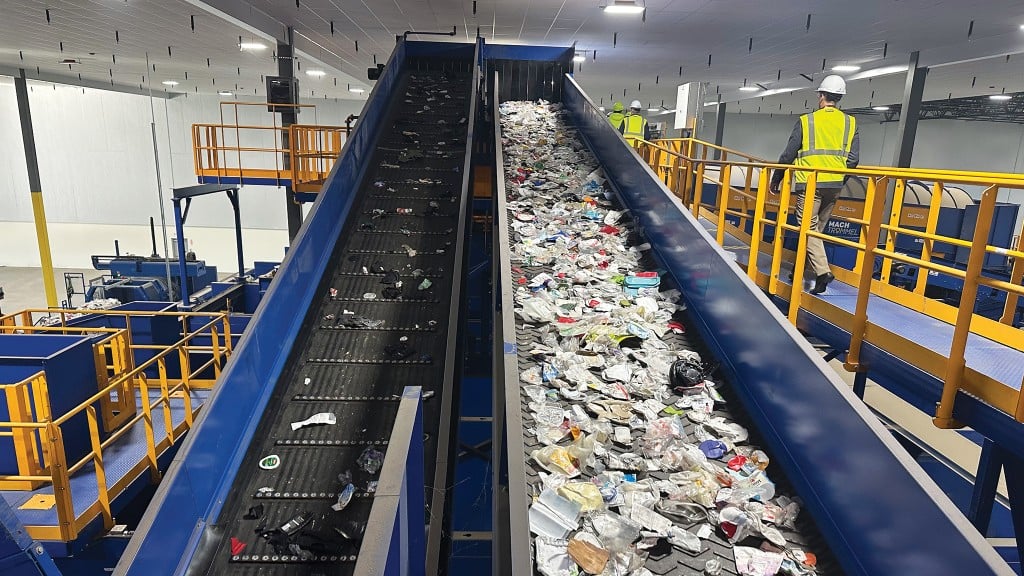
Polypropylene (PP) is one of the most widely used plastics in the world. It is manipulated for various consumer goods including packaging, parts for machinery, and even textiles.
Yet, despite its critical role, creating a blueprint for effective PP recycling has proved challenging. Contaminants, such as organic debris, elements added for functionality, colouring agents, and metal particles, are all obstacles to delivering a virgin-like PP end product. These obstacles have led to lower recycling rates compared to other plastics like polyethylene terephthalate (PET).
PureCycle is rising to address the challenges in PP recycling. Its patented technology surpasses traditional, mechanical methods of purification to go beyond surface cleaning and remove contaminants at the molecular level.
Why is recycling polypropylene challenging?
Polypropylene's durability and versatility make it a popular choice for manufacturers across many sectors, but these same properties complicate its recycling.
"If you think about plastics in the world, there are so many different types," explains Dustin Olson, CEO of PureCycle. "They could be different colours, shapes, sizes, or forms like fibre, film, or rigid materials. PP often contains additives like rubber or talc to improve functionality, making it difficult to purify."
Traditional mechanical recycling processes only clean the surface of the plastic, removing contaminants like food residue, but fail to address embedded colours, odours, and additives. Mechanical recycling degrades the polymer over time, which results in low-quality recycled PP that can only be used in limited applications.
PureCycle's recycled polypropylene purification process
PureCycle's patented purification technology, originally developed by Procter & Gamble, offers a promising solution to recycle polypropylene. This dissolution process uses extraction and filtration, isolating polypropylene while leaving contaminants behind. PureCycle is effectively creating a "molecular washing machine" that removes impurities at a molecular level.
Olson illustrates the process with a simple analogy: "Imagine mixing salt and pepper together in a bowl. We add a solvent that dissolves the salt (PP) but leaves the pepper (contaminants) intact. We filter out the pepper, evaporate the solvent, and are left with pure salt."
Unlike chemical recycling, which breaks plastic down to refining and petrochemical feedstocks, PureCycle's advanced dissolution process retains the polymer chain, producing near-virgin-quality PP.
This ensures "high quality, high yield, and a low carbon footprint," says Olson. "Our process allows our customers to do what they do without compromise. There's a lot of value in that."
Machinex's role in achieving feedstock purity
While PureCycle's technology is a potential game changer, it operates more efficiently with higher polypropylene plastic content feedstock. This is where Machinex's automated sorting system comes in.
By integrating Machinex's innovative sorting technology into the process, PureCycle has further strengthened its operations with a consistent, high-purity feedstock. The Denver, Pennsylvania, facility, developed in partnership with Machinex, plays an important role in pre-processing.
"We knew we needed to secure our feedstock position to better control our destiny on purification," Olson explains. "Machinex helped us design a regional [preprocessing] facility that provides consistent quality and minimizes logistics costs."
The Denver facility utilizes advanced sorting technologies, including infrared (IR) systems to identify different types of plastic and robotic arms to remove contaminants. According to Olson, IR sorting works by shining a light on the plastic and characterizing the properties of the reflected light.
Each type of plastic reflects a unique signal, enabling precise identification. Robotic arms then isolate contaminants to ensure the purity of the feedstock. This automated approach drastically reduces labour costs and human error, resulting in higher feedstock quality and improved downstream processing.
The synergy between PureCycle and Machinex
The partnership between PureCycle and Machinex facilitates an elevation of each of these technologies in processing polypropylene plastics.
"Our purification technology is very robust, but the efficiency of our process depends on the quality of the feedstock," says Olson. "By preparing our feed better through Machinex, we should achieve higher production quality, better carbon efficiencies, and enhanced rates."
Machinex's sorting process ensures the feedstock entering PureCycle's purification process is predominantly PP, maximizing efficiency and minimizing waste. This synergy enhances the scalability of PP recycling and sets a precedent for integrating automation into recycling workflows.
Mechanical recycling automation is the backbone of efficiency
Automation plays a pivotal role in PureCycle's operations at both the sorting and purification stages, especially when processing polypropylene material.
"In addition to partnering with companies like Machinex to mostly automate plastic sortation, the processes we use to purify the plastic and make [recycled polypropylene pellets] are fully automated," says Christian Bruey, director of communications for PureCycle. "Our skilled operators and technicians oversee and optimize these complex operations."
Olson adds, "We were born digital. We leverage data analytics from all our processes in a sophisticated way." This commitment to automation guarantees efficiency and consistency and ensures that PureCycle can scale its operations without sacrificing quality or sustainability.
Benefits of polypropylene recycling
Recycling polypropylene offers many benefits that extend beyond environmental conservation. One of the most significant advantages is the conservation of natural resources. Recycling polypropylene reduces the need for virgin materials, which in turn decreases the extraction and processing of oil and gas. This not only conserves resources, but also reduces the environmental footprint associated with plastic manufacturing.
Another benefit is the reduction of greenhouse gas emissions. The recycling process typically requires less energy compared to producing new polypropylene from raw materials. This energy efficiency translates into lower carbon emissions, and supports the circular economy by creating a closed-loop system where materials are continuously reused.
Implications for the recycling industry
The collaboration between PureCycle and Machinex helps address the challenges of recycling PP. This partnership also plays a role in transforming the industry as a whole. By demonstrating the viability of turning post-consumer curbside waste into high-quality feedstock, PureCycle and Machinex may influence further investment in recycling infrastructure.
"I think that there needs to be further investment in technologies like PureCycle and like Machinex and I would say also in MRF infrastructure. Extended producer responsibility legislation can be a mechanism for this," says Bruey. "It would be great to see these MRFs that are maybe 10, 20, 30 years behind the times and using just manual labour to see what you can do with the type of technology offered by Machinex."
"Recycling gets a bad rap at times. You and I, sitting at home, have to put it in our bin to make that recycling rate grow. And then we need the technologies to continue to improve. We're starting to see that," adds Bruey. "You can see that there is some real opportunity here for us to change the tide and really tell a great story of circularity and sustainability."
A vision for the future
PureCycle's aspirations extend beyond its current operations. With plans to expand in Augusta, Georgia, and globally, including facilities in Belgium and Asia, the company is poised to influence change in the expanding circular economy for plastics.
"The future of PureCycle is unbounded potential," says Olson. "We have a game-changing technology that, when applied to polypropylene, can have a transformative impact on the way recycling is done and also viewed by the consumer."
Through their partnership with Machinex, PureCycle is addressing the challenges of PP recycling and setting a new standard for innovation and sustainability.