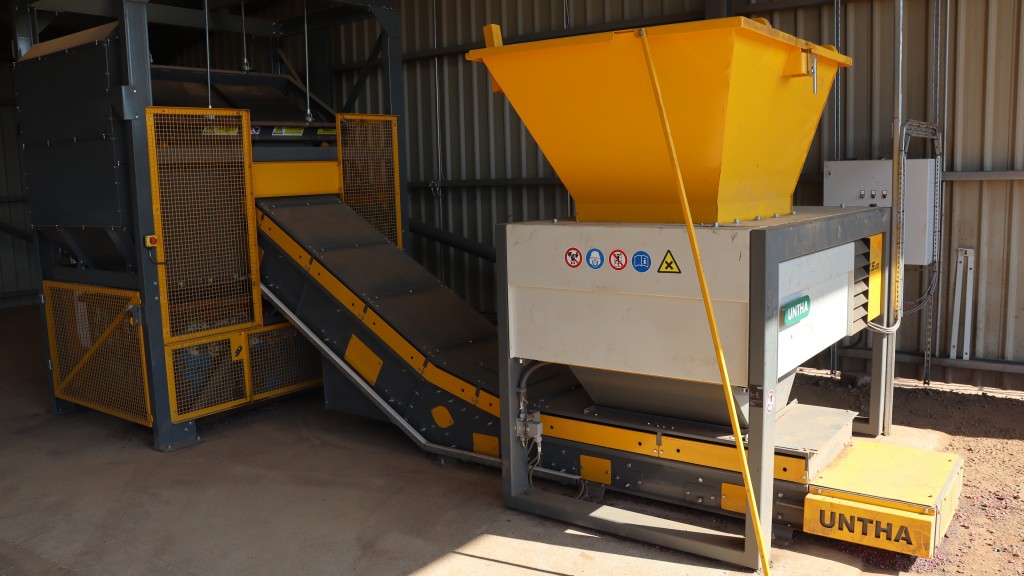
John Lawrie Tubulars has invested in a system that enables the 100 percent in-house recycling of its tubular by-products. Following successful trials, a specially configured RS40 four-shaft shredder from UNTHA is now in operation.
With operations in the U.K. and the U.S., John Lawrie Tubulars' 15-acre Montrose facility houses a full-service manufacturing, cleaning, recycling, and warehousing operation.
The firm purchases steel tubulars from the oil and gas industry, before giving the products a new life in construction piling. Repurposing the materials achieves a 97.21 percent carbon emission saving compared to using raw materials.
Keen to improve its sustainability agenda, John Lawrie Tubulars has now also invested in an UNTHA plastic shredder. This shredder can process half a tonne of screw caps – oil tube tread protectors – per hour, shredding the otherwise bulky material down to a homogenous 15-millimetre fraction.
Drum and over-band magnets affixed to the discharge conveyor then extract metal content from the output material for local resale and recycling in Aberdeen while the plastic is also sent for remanufacturing. This results in the 100 percent reuse of material that was previously unusable.
"We had heard that UNTHA shredders are valued for their longevity and reliability, which is something we value as a company," said John Lawrie Tubular's U.K. Sales and Purchasing Manager Iain Bell. "We therefore arranged a trial with a small sample of material, to see if the technology could tackle our input material. Impressed from the outset, we then arranged a second ‘shred test' to see how the machine performed with a full load.
"We were really pleased with the output quality as well as the availability of UNTHA's expert support, should we need it. Their communication has been exceptional."
"As the RS40 was already in stock and immediately available from our North Yorkshire headquarters, we simply configured the technology to meet John Lawrie Tubular's specific requirements," said UNTHA U.K.'s Sales Consultant Lewis Horne. "That's the beauty of this flexible recycling system. Only the conveyor required manufacturing, which shortened the lead time to commissioning. We've invested heavily in stock machines for this reason."