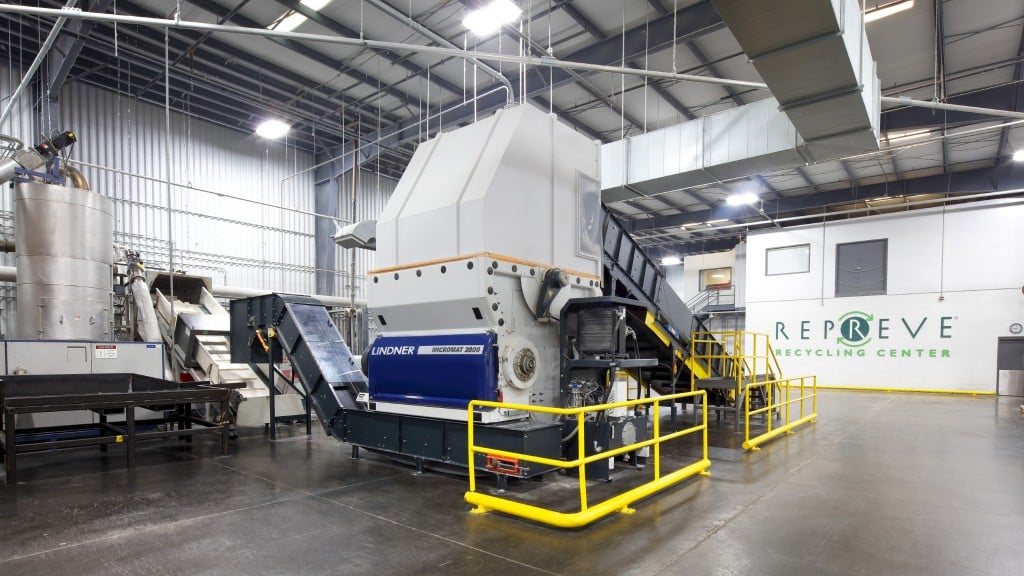
Of the 400 million tons of plastics produced worldwide each year, too much still ends up in waterways and landfills. Unifi, Inc. has decided to tackle this global problem. They collect used plastics, primarily post-consumer PET bottles, and transform these plastics into REPREVE, a recycled fibre. Three shredders from Lindner's Micromat series work to ensure that the plastics are optimally shredded for the downstream processes.
Higher recycling rates, improved collection systems, and more efficient processing facilities ensure that plastic waste is recycled and repurposed. Yet, there is much work left to be done and much plastic still goes unrecycled. To date, Unifi has transformed 35 billion plastic bottles into its proprietary REPREVE recycled fibre. Unifi's process ensures that plastics are returned to the consumer goods cycle as a valuable raw material and promotes a more circular economy.
From plastic collected within 50 kilometres of waterways or coastal areas, mainly in developing countries, Unifi produces Repreve Our Ocean recycled fibre. This process ensures that plastics are removed from the ocean and then returned to the recycling stream as raw material, avoiding the islands of rubbish from growing in oceans and reducing their impacts on humans and animals.
When Unifi was looking for a reliable partner to set up an efficient shredding process in 2018, they chose Lindner. A total of three Lindner Micromat 2000 shredders prepare plastic and textile waste for its journey to extrusion, spinning, and then winding the fibres.
Scott Trivette, operations manager of the Repreve Recycling Centre and Future Innovation Centre in Yadkinville, N.C., describes the relationship with Lindner as "a great partnership, which we require because of our 24/7/365 operating model. A provider who can only be there for us between 9 a.m. and 5 p.m. just doesn't work for us. We need answers within hours, not days, and Lindner with its hub in Statesville, N.C. is always there for us."
The Lindner shredders are designed for the requirements of post-commercial and post-consumer plastics recycling. They have strong, high-torque motors for shredding and are designed and built for ideal uptime and to streamline maintenance tasks.
Trivette says that the safety coupling offers ideal machine protection and access to the rotor to enable the fast removal of non-shreddable plastics.
"Lindner's machines have enabled us to minimize downtime and maximize the throughput of the entire plant, which is essential with an average production of 1.5 million pounds of resin per week," he continues.