Understanding the role of AI in the MRF
AI can excel when used as part of a holistic solution
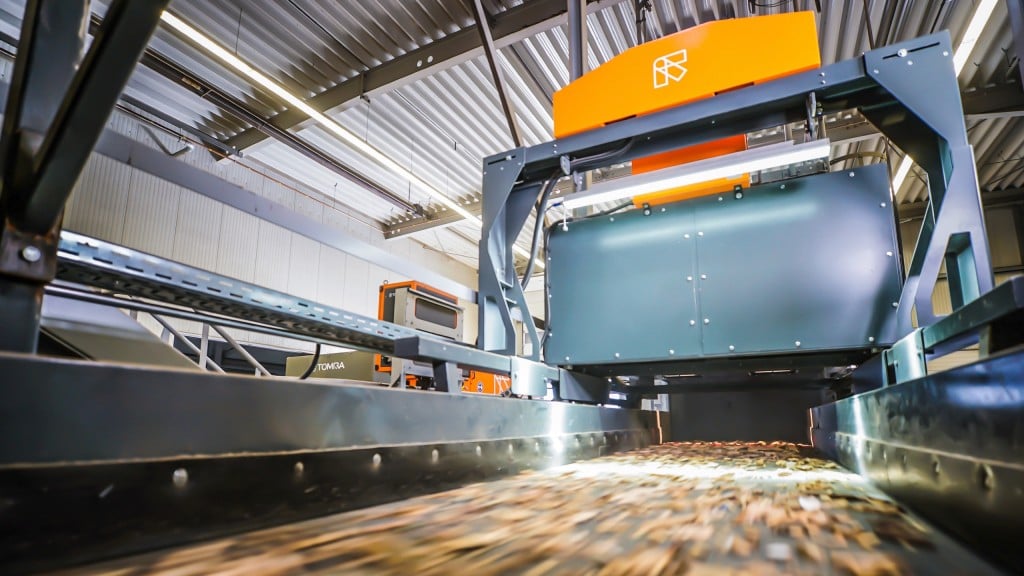
Talk of artificial intelligence (AI) has taken the recycling industry by storm and for good reason. When applied correctly, today's emerging AI technologies have transformative powers, driving automation and efficiently enabling more granular sorting of complex material fractions. When not, however, it can be an enormous waste of both time and financial investment.
Much of this buzz originates from a new type of ejection method for optical sorters – a robotic arm rather than valve blocks. The traditional valve block optical sorter employed in thousands of recycling facilities for decades uses precisely timed pulses of air in a drop-eject method to sort materials at rates reaching eight tons per hour or even higher, depending on the sorting task. Conversely, the new robotic arms more closely mimic a human's picking motion of multiple fractions at rates slightly higher than that of a person, roughly 0.5 tons per hour.
For this reason, Ty Rhoad, regional director of the Americas for TOMRA Recycling Sorting, advises recyclers they need to fully understand what exactly makes up AI and what it's designed to do. He stresses that AI is not the machinery – either the robotic arm or the valve block – and redirects the focus to highlighting how AI can be leveraged at the facility by incorporating it as part of a holistic solution.
"Right now, it's like AI is the must-have technology for customers," he says. "Recyclers must fully understand how it works and how it will improve the sort. Otherwise, final product and investment expectations may not be fully realized."
AI is not new
The good news: AI is nothing new to the industry. Most recycling facilities are already using some form of it. Optical sorters with valve block ejection have leveraged traditional AI for decades to drive sorting circuit automation and recycled product purity. Plant builders and technology suppliers have worked with customers to design material flows to improve yield, purity, and throughput with fewer manual sorters.
The heart of AI is software and algorithms, not the hardware. Traditional AI is used in combination with a variety of sensors – RGB cameras, near-infrared (NIR), laser, EM (electromagnetic), and X-ray – to automatically detect and process fractions.
"Traditional AI was a manual process," mentions Anthony Belmares, field service supervisor for TOMRA. "A technician engineers the classifiers and deploys it into the in-house developed sorting software."
Every sensor-based sorting machine consists of numerous components, all of which play their role and are chosen according to the sorting task. How well, or poorly, material fractions are sorted depends on how the core components – namely the sensor system, data processing (software), conveyor system, and ejection system – work together.
"This is why TOMRA invests roughly eight percent of our revenues on research and development," offers Rhoad. "We create the software internally, so we can optimize sorting performance for a range of material streams from waste and plastics to metals and wood."
Advancements in sensors and traditional AI have already led to many automated sorting improvements. Throughout the years, optical sorter designs have evolved with greater computing power and improved algorithms to leverage traditional AI and greatly improve colour sorting.
"This allows the MRF to sort out higher value clear and light-blue PET with higher yields and less contamination for secondary plastics sorters, so bales can be sold as Grade A or B versus Grade C or D," offers Rhoad.
Five years ago, optical sorters had a difficult time sorting PET bottles from thermoforms. The ability to separate the two results in higher quality rPET being cycled back into new PET bottles.
"We developed the SHARP EYE sensor and our Intelligent Object Recognition software to give AUTOSORT the ability to distinguish the small differences between PET bottles and thermoforms, so they can be separated for equivalent product recycling," offers Eric Olsson, plastics segment manager for TOMRA.
He also points to recent advancements in flake sorting and the company's work to develop a mechanical sorting process for consistently separating mixed polyolefins by polymer and colour to close the loop on food-grade, cap-to-cap recycling.
"Advancements made in our near-infrared (NIR) sensor, two-sided colour cameras and sorting software ensure classification of PE and PP materials and position the industry at the beginning of mixed polyolefins going closed loop," Olsson adds.
Deep learning
AI's deep learning subset further advances sorting accuracy and adaptability to material streams. Large datasets of trained neuronal networks enable deep learning technologies to recover materials that are difficult or even impossible to distinguish using traditional technologies.
For deep learning to work, software engineers train the network with thousands of images that hold a pool of object information. The network recognizes patterns in the data and connects this information pool to the sorting task.
Since these most recent advancements in AI are application-specific, Belmares cautions the technology supplier must provide the recycler with material testing, training, and optimization.
"A supplier cannot just drop AI-based equipment into the circuit and leave," he says. "Full potential is only achieved through a well-optimized and positioned machine with workers trained on how to get the most out of it."
Optimization leads to a much more granular sort. Whereas conventional optical sorters accurately identify and sort aluminum from the material stream, "trained deep learning systems take the next step to detect and sort items like used beverage containers (UBC) from other aluminum in the stream," Rhoad explains. "Deep learning enables recyclers to selectively target a specific value stream and increase purity of that product."
Rhoad is optimistic about the industry's future with deep learning and sees several areas where AI can play a part in improving the sort.
"We've already launched applications like wood sorting for TOMRA's deep learning-based GAIN and will soon have an application that focuses on the aforementioned UBC cleaning. We also see value for the industry with PET cleaning and the ability to detect PET food-grade containers from the material stream."
Because of its ability to be trained to see objects on the belt like a human sorter, AI's deep learning technology, when combined with conventional sorting technologies, can bring final product qualities and yield to the next level. Because deep learning is application-specific, however, recyclers need to work with a trusted technology supplier to ensure that they get the most out of it.