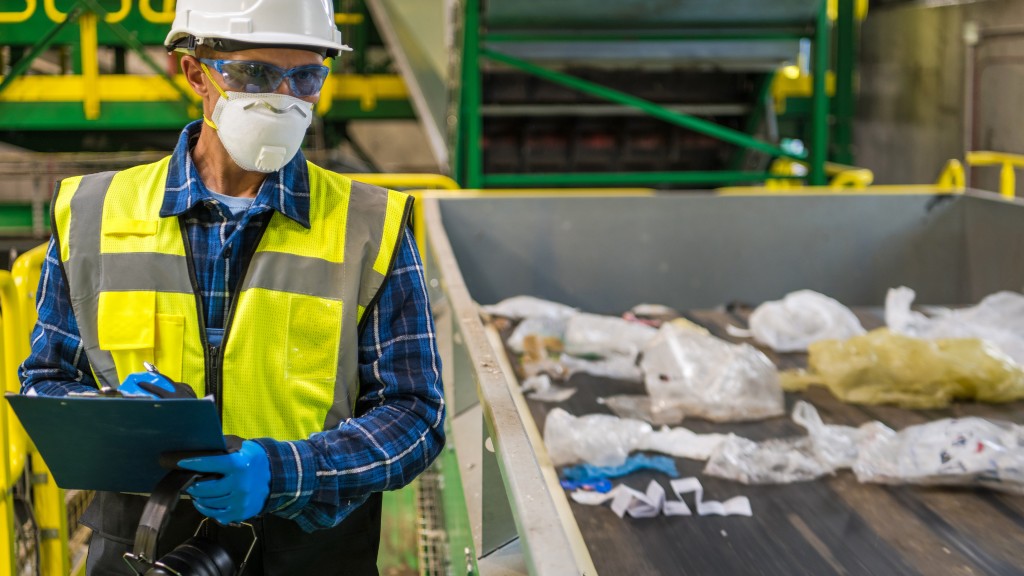
Behind the walls of recycling facilities across the U.S., a sea of materials moves through hands and machines working hard to get them to the end of the line – and the beginning of their next life. A critical balance of manual labour and automation enables the sorting and recovery of these materials in a closed-loop system. Yet despite a multi-step sortation process, it is difficult to track what flows through the system at all times. It's a challenge that results in many recycled materials losing potential value, in addition to millions of dollars worth of valuable material being sent to landfills unintentionally.
Among the diverse materials flowing through the recycling system are the yogurt containers and iced coffee and fountain beverage cups many use on a regular basis. These are just a few examples of products made of one of the most commonly used resins in food service packaging today: polypropylene (PP). PP is a valuable material that should be kept in circulation to reduce waste and meet corporate commitments to use more recycled content in food service packaging. With that said, very little mechanically recycled food-grade PP actually cycles back into food-grade applications. Most end up in nonfood-grade applications that limit their value and the number of times they can be reused. To create a more circular path for food-grade PP, we must first answer the question: What is in the PP stream today, and how much of it is food-grade or clear food-grade PP?
The NextGen Consortium is a multi-year industry collaboration addressing single-use foodservice packaging waste by advancing solutions across material innovation, reuse, and recovery infrastructure – and it's working to answer that question. In the fall of 2022, the Consortium partnered with Resource Recycling Systems to examine PP bales in two materials recovery facilities (MRFs) to learn what was inside. While only a snapshot in time, the results were enlightening.
On average, nearly half of the PP bales (48 percent) were presumed food-grade, and more than a quarter of the bales were clear food-grade (26 percent). Clear beverage cups represented 14 percent of the bale on average. The high percentage of food-grade PP suggested that there is untapped value in the PP stream. A better system is required to ensure food-grade and/or clear food-grade PP is properly sorted into a separate bale at some point in the value chain if we are to retain its highest potential value.
In 2023, the NextGen Consortium is diving even deeper, launching a study leveraging artificial intelligence (AI) to analyze the composition of the PP material stream before it ends up in a bale. The NextGen Consortium is working with Greyparrot, an AI waste analytics platform. The collaboration aims to track and categorize objects in the PP stream and determine the volume of valuable food-grade material passing through the system. AI is on the rise as one potential means of increasing visibility into the recycling process. More technologies are needed to handle an increasingly mixed stream of collected materials, including plastics, electronics, textiles, and food scraps – and to enable the recovery of clean, high-quality materials.
"Ensuring that recovery infrastructure can keep pace with a rapidly growing and diverse material stream is critical to advancing the circular economy, alongside solutions such as material innovation, reduction and reuse," said Kate Daly, managing director and head of the Center for the Circular Economy at Closed Loop Partners. "An important part of our work in the NextGen Consortium is identifying opportunities for data collection and analysis that can advance the circularity of foodservice packaging, and drive greater value for stakeholders across the system, including brands, innovators, infrastructure operators and consumers."
As part of this project, Greyparrot Analyser units will be installed above the PP recovery conveyor belts at four U.S. MRFs: Balcones Recycling, Texas; Cougles Recycling, Pennsylvania; Rumpke Recycling, Ohio; and Eureka Recycling, Minnesota. Greyparrot's AI-powered computer vision system uses cameras to capture images of objects in the PP stream, aiming to quantify and qualify the materials flowing through the MRFs. Their AI model will look to categorize each object based on material, format, financial value, and brand – as well as distinguish food- and nonfood-grade material – using those images. Their units will then send that data to an analytics dashboard in real time. Through machine learning, flexible vision systems can help improve package recognition and classification over time.
"We use artificial intelligence to gain continuous and reliable visibility into recycling streams," said Ambarish Mitra, co-founder and CPO of Greyparrot. "This helps us improve recycling operations by placing waste intelligence into the hands of the people who are recovering, redesigning, and remanufacturing the objects we throw away. We are thrilled to work with our U.S. partners towards our vision of a future where every piece of waste is valued as a resource."
The collaborative project will run for more than six months. During that period, it will gather data on the composition of PP bales while accounting for seasonality. That insight can help determine the potential untapped value in these streams, and identify other materials that might be coming through unintentionally. This data can also help shed light on the presumed volume of food-grade material being captured in the system, along with opportunities for recovery and separation into distinct value chains. More broadly, this can advance a circular economy for valuable materials, improve material quality delivered to recycling facilities, and enhance the value of recyclable commodities shipped to U.S. end markets.
"A lot is unknown about the curbside polypropylene stream today. Filling these knowledge gaps can increase the pace of development for material recovery. Understanding the composition of the stream in a large-scale study highlights potential, reduces risk for pioneers, and accelerates better design implementation. This study will be the catalyst to developing much larger-scale recycling of polypropylene," said Curt Cozart, president of Common Sense Solutions and technical advisor to the project.
PP cup recovery is a critical focus for the NextGen Consortium. According to The Recycling Partnership, more than 2 billion pounds of PP are generated every year by single-family households in the U.S. If just 30 percent of this material were recovered, it would reduce greenhouse gas emissions by over 300,000 metric tons, providing over 600 million pounds of valuable raw material to companies with recycled content commitments for their foodservice packaging, both voluntary and mandated.
As more data about the PP material stream is captured over the next six months, the consortium will analyze the new data to identify opportunities to improve PP sortation and recovery, finding new food-grade applications and areas where more research is needed.