Ascend Elements and EcoPro to supply recycled battery materials to North American EV industry
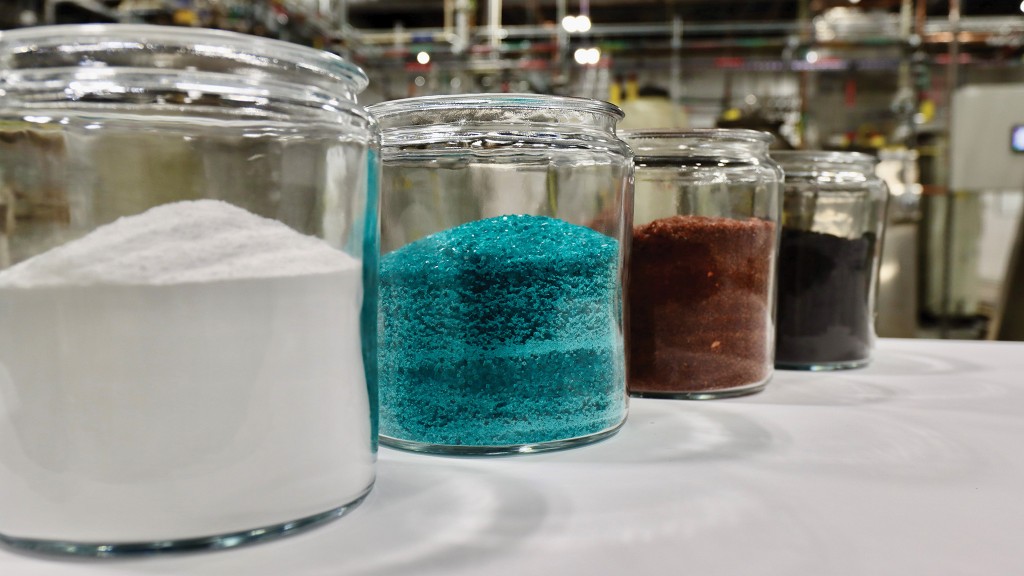
Ascend Elements, a Massachusetts-based battery recycling and engineered materials company, and EcoPro Group have released a memorandum of understanding (MOU) agreement to cooperate in the development, qualification, and integration of recycled battery materials into EcoPro's cathode products.
EcoPro is a cathode active material (CAM) supplier to EV battery manufacturers in North America while Ascend Elements recycles EV batteries and battery manufacturing scrap from many sources, including the SK Battery America (SKBA) facility in Commerce, Georgia. Beyond EV battery recycling, Ascend Elements also transforms recycled batteries and manufacturing scrap into new, sustainable cathode precursors. With this agreement, Ascend Elements will supply recycled battery materials to EcoPro, which will convert the material into battery-ready, high-performance CAM for its battery manufacturing clients.
"This is one of the first North American examples of a truly circular battery economy," says Michael O'Kronley, CEO of Ascend Elements. "Currently, battery manufacturing scrap is the largest source of lithium-ion battery materials available for recycling. We're not only recycling this scrap material and keeping it out of landfills, we're elevating the value of the material by engineering it to meet EcoPro's precise specifications."
By using recycled battery materials instead of newly mined materials, battery manufacturers can significantly reduce the climate impact of EV battery manufacturing. Additionally, cathode precursor made in the United States from recycled lithium-ion batteries is considered a domestic source of battery materials under the U.S. Inflation Reduction Act.
Ascend Elements uses a Hydro-to-Cathode direct precursor synthesis process to transform black mass into sustainable, high-performance precursor and CAM that rival or exceed the performance of cathode materials made with virgin metals. The process can recover up to 98 percent of critical battery elements with lower carbon emissions compared to traditional cathode manufacturing methods.
The company plans to invest up to $1 billion to build a sustainable lithium-ion battery materials facility in Hopkinsville, Kentucky. The manufacturing facility, known as "Apex 1", will produce enough lithium-ion battery precursor and sustainable CAM to equip up to 250,000 electric vehicles per year.