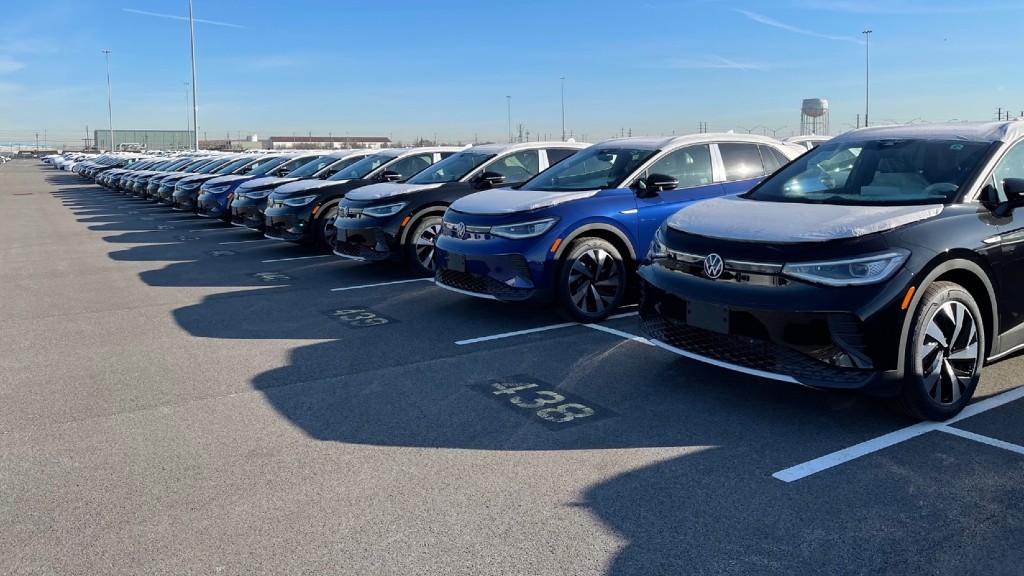
Volkswagen Group of America, Inc. and Redwood Materials, Inc. will collaborate to create a supply chain to recycle Volkswagen and Audi electric vehicle batteries in the United States, with the goal of providing accessible and more sustainable electric mobility for American drivers. By advancing Volkswagen Group of America's strategy to localize all major competencies for its electric transformation, as well as Redwood's goal of creating a closed-loop supply chain for lithium-ion batteries, the collaboration represents a crucial step in growing North America's domestic EV industry.
"For Volkswagen, going all-in on electrification means driving sustainable solutions at every turn," says Scott Keogh, president and CEO at Volkswagen Group of America, Inc. "Redwood Materials is a great partner to help us accelerate EV adoption in America. This collaboration allows us to move closer toward our goal of closing the loop for a circular EV economy, giving American consumers yet another reason to go electric."
The new EV battery recycling collaboration will be facilitated by VWGoA's nationwide network of approximately 1,000 dealers, starting with the Volkswagen and Audi brands. Key to the collaboration is a holistic approach to the battery lifecycle. By allowing for more sustainable utilization of battery components from the moment vehicles leave the assembly line through the end of their lifecycle, the collaboration can support local battery capacity and expertise as Volkswagen continues its transition to an electrified portfolio.
As Volkswagen Group brands plan to introduce more than 25 new battery electric vehicles to American consumers through 2030, VWGoA aims to begin establishing battery recycling capabilities for current and future vehicles in North America now. In addition, the new EV battery recycling collaboration will integrate prototype batteries from Volkswagen's research facilities such as the Battery Engineering Lab (BEL) in Chattanooga. Redwood Materials will work directly with dealers and Volkswagen facilities to identify end-of-life batteries and materials, and then safely package and transport them to their Nevada facilities.
"The electric transformation means making commitments in many areas throughout our business," said Daniel Weissland, president at Audi of America. "In addition to our robust lineup of fully electric Audi e-tron models available now, having like-minded partners like Redwood Materials in place to further reduce environmental impact throughout the lifecycle of every electric vehicle is critical."
Each year, Redwood already recycles more than 6 GWh of lithium-ion batteries, the equivalent of 60,000 EV batteries, in Nevada. The batteries that come to Redwood are composed of end-of-life consumer devices, battery production scrap, and electric vehicle batteries, and represent the large majority of lithium-ion batteries recycled in North America. Redwood then extracts raw materials such as cobalt, copper, nickel, and lithium, refines and remanufactures them into critical battery components, anode copper foil and cathode, before delivering those products back to domestic battery cell manufacturers.
"The transition to electric transportation and clean energy is coming and the batteries powering these technologies present an incredible opportunity. As more and more batteries reach end-of-life each year, an increasing and infinitely recyclable resource becomes available", says JB Straubel, Redwood Materials founder and CEO. "Redwood and Volkswagen Group of America share a vision to create a domestic, circular supply chain for batteries that will help improve the environmental footprint of lithium-ion batteries, decrease cost and, in turn, increase access and adoption of electric vehicles."
The collaboration of Volkswagen Group of America and Redwood Materials reflects a shared vision for a circular EV economy that, if adopted across the industry, could help reduce battery costs and the need to mine and ship raw materials.
Volkswagen Group of America is aiming for 55 percent of its U.S. sales to be fully electric by 2030. To achieve this goal the company is transforming the North American region into an EV powerhouse, featuring localized EV engineering and R&D capabilities, EV assembly and component production for its brands, and plans for a dedicated battery cell production.