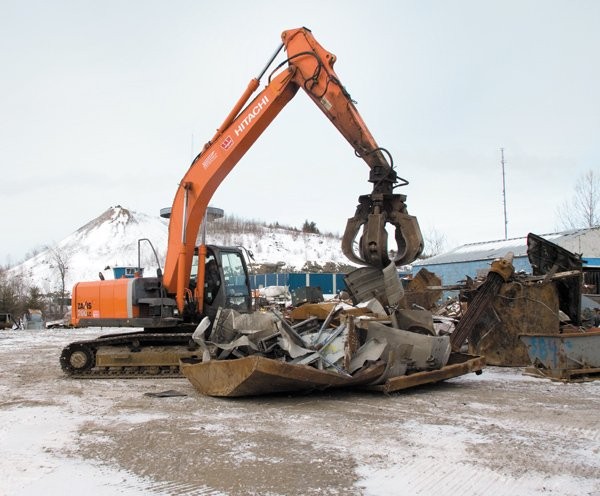
Not content to buy, process, and recycle scrap in one location, Scrappie’s Salvage Iron & Metals is a truly mobile processing operation. Based out of Hanmer, Ontario, and with an additional yard in Timmins, Labelle’s company travels all over the province, visiting scrap yards, mines, and the temporary holding yards of demolition contractors.
“Our job is to make scrap saleable for our customers,” says Mike Labelle, Scrappie's owner. “We have mobile shears, mobile car crushers, and mobile tin balers that crush and recycle a wide range of primarily ferrous materials – including cars, tin, appliances, heavy steel, plate steel, and structural steel.”
“We’re not a demolition company. We buy scrap when it hits the ground and process it right there. Then we usually ‘mag’ it onto our truck and bring it back to our yard to process the material down to the mill’s specifications before delivery.”
Mobility is key
According to the Institute of Scrap Recycling Industries, while some segments of the Canadian and U.S. economies are slow, demand for scrap commodities continues to be strong. And with the weak dollar, imported steel is now more expensive, so domestic mills are busier. At the same time, a weaker dollar makes scrap exports from Canada and the U.S. more attractive.
“It’s not rocket science, but you’ve got to know your materials and their market value,” says Labelle. “You also need the right equipment for efficiently processing and handling a lot of scrap.”
“We have several Hitachis in our yard and on location. Most are Zaxis 200s with magnets or grapples. Some are configured to switch back and forth between the two. We also have a ZX210 wheeled excavator with a two-finger clam that sorts nonferrous materials. It’s faster than a tracked machine, obviously, which lets it efficiently move around.”
“We have one ZX370LC-3 with a shear that processes beams and other large steel from demolition scrap,” he continues. “Some beams are 100-feet long. We cut them into four-foot lengths in a process called ‘manufacturing’. We used to have a crew of guys torching steel, but safety is very important to our customers.”
“Putting a man in a guarded cab and hydraulically cutting and moving steel is the only way to go.” Labelle cites reliability, fuel-efficiency, low-maintenance and service as key factors to good equipment. “Reliability is especially crucial when you’re on the road. You can’t have something that’s going to break down every week,” he says. “You have to move the material quickly,” Labelle says.
“In this business, you’re only guaranteed a scrap price for a month, so if I quote you a price on the 17th of the month and you accept it two days later, that gives me a week or so to get in, get the material out, process it, and deliver it to the mill before the month is over. The price could go down next month, so it’s go, go, go!”