"Scrapping" the scrap removal problem
Largest ever beltless magnetic conveyor proves right choice for manufacturing operation
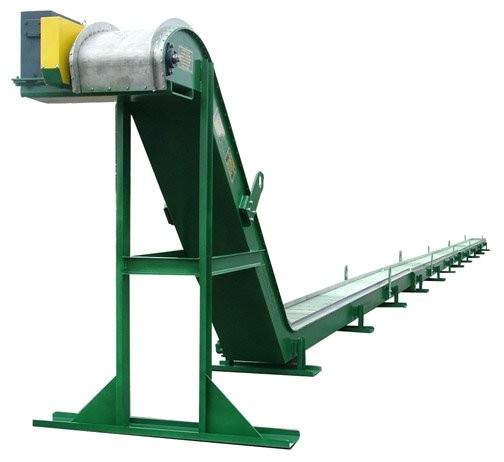
Removal of scrap metal is a vital, constant and costly function faced by plant managers worldwide. Untimely removal of scrap can endanger workers and damage machinery, and storage of traditional scrap bins on factory floors reduces overall available manufacturing space and is unsightly. Despite declining monetary and human resources, plant managers must continue to ensure that scrap metal is removed for recycling in a timely and reliable manner.
Several years ago, a major Midwestern manufacturer in the U.S. needed to install a new press with an unusually high drop from the pass line of the press to the scrap removal conveyor. This presented a number of challenges. Firstly, the conveyor had to keep up with an extremely high volume. Secondly, each piece of scrap was over a foot long. And thirdly, the angle of incline had to be extremely steep to accommodate the plant’s current deep pit.
The company debated the merits of a steel hinge conveyor versus a magnetic conveyor. In this case, it was determined that the magnetic conveyor was clearly the right choice. The magnetic conveyor would offer a substantial costs savings and improved performance as compared to its steel-belted counterpart. Furthermore, the manufacturer would not have to deal with slide back or “cascading” scrap, or wedging scrap, which commonly leads to the early demise of steel conveyors. They contacted Magnetic Products, Inc. (MPI), a Michigan-based provider of both magnetic and non-magnetic material handling solutions. After extensive testing in its in-house research facility, MPI recommended its Series 1200 beltless magnetic conveyor.
According to MPI, their beltless magnetic conveyors provide positive control of ferrous metal materials, using powerful permanent magnets conveyed below a non-magnetic stainless steel slider bed to move and convey ferrous metal objects. BLM conveyors are offered in a variety of sizes with many design options and can be supplied with other ancillary components, such as feeders and hoppers, to provide a complete material handling system. The company also offers complete demolition of old equipment as well as installation services.
What resulted for the Midwest manufacturer was, at the time, the largest BLM ever built by MPI. The job they needed done by the system was to catch all of the metal scrap so that they could efficiently remove it from the plant floor and return it to their steel supplier for re-melting and processing back into useable material. According to the company, after seven years, operating on a 24/7 schedule, the conveyor has flawlessly processed 6.5 lbs. of scrap per stroke, which equates to more than 10,000,000 lbs. of scrap.
Five years after the initial installation, the same manufacturer faced another challenge. The plant now required a conveyor that was able to handle an even bigger load: eight lbs. of scrap per stroke. The solution was an even bigger MPI beltless magnetic conveyor which, this time measured 24” wide, 35’ long and 20’ tall with an 18’ in-feed. The new conveyor featured:·powerful Ceramic 8 magnet material; an internal oil reservoir which allows for continuous lubrication; a reinforced impact bed designed to perform consistently in extremely rugged environments; a self-adjusting chain tensioning system; 7 gauge stainless steel slider beds; and a 7.5-hp 230/460V 3-phase motor with gear reducer and torque limiter.
“That conveyor was a monster.” remarks Barry Tackett, one of MPI's customer service representatives. “We had to ship it on a flat-bed. It was too big to fit in a semi-trailer.” According to MPI, this latest installation -- now their biggest BLM conveyor ever -- has operated 24/7, for over 18 months, without incident and without downtime.
Magnetic Products, Inc.
www.mpimagnet.com