Shredders vs grinders: Are shredders replacing grinders for wood waste?
Differences like throughput, maintenance, and speed are essential considerations for selecting the right equipment
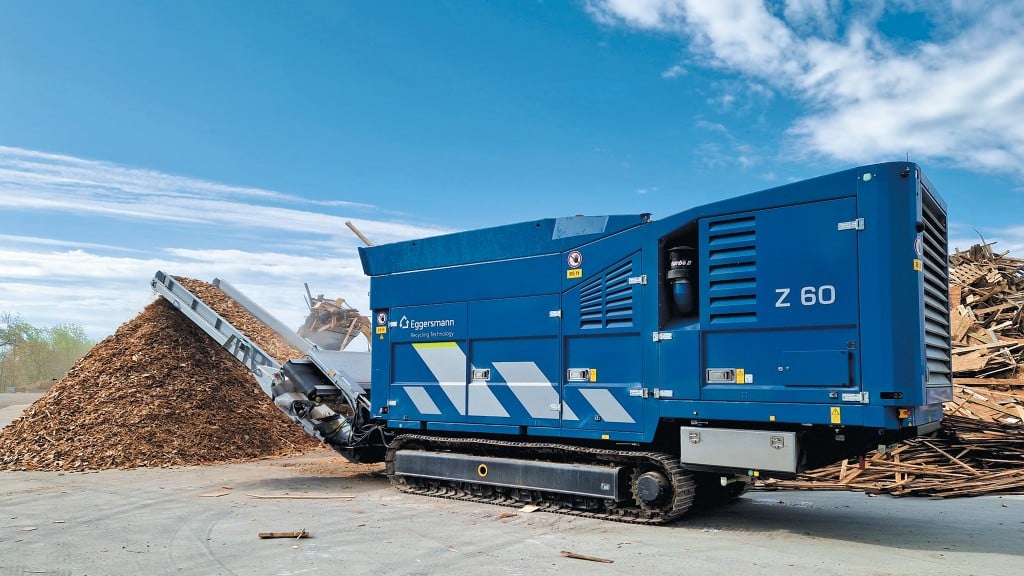
The waste and recycling industry has seen significant advancements in technology over the past few decades, particularly when it comes to processing wood waste. As municipalities, businesses, and contractors continue to seek more efficient and sustainable ways to handle wood debris, two types of equipment have emerged as popular options: shredders and grinders.
Both play a pivotal role in reducing the volume of wood waste for recycling, reuse, or disposal, but are shredders beginning to replace grinders for wood waste processing?
Key differences between shredders and grinders
Before diving into the reasons why one machine might replace the other, it's important to understand the fundamental differences between the two. Shredders were once primarily used for contaminated wood, but in recent years their use has expanded across all wood waste recycling sectors, says Christopher Pickhardt, president of Eggersmann.
"The feedstock for shredders includes clean white wood, logs, stumps, roots, green waste, mixed feedstocks of dirty green waste, construction and demolition waste, and other wood waste that may be contaminated with rocks, dirt, or tramp metal," says Pickhardt. "There are also special applications such as solar panels, tires, windmill blades, railroad ties, or glass that a shredder can handle and make a product out of."
Grinders, on the other hand, are better suited for processing larger volumes of wood and are often used in applications where the final product needs to be uniform and consistent in size, like mulch or wood chips. For operations that focus on large-scale wood processing or need to break down large wood debris quickly, grinders are still the go-to solution.
"Shredders often have a bit less production than a grinder. However, shredders have a higher throughput per horsepower than a grinder typically does. The specific weight per cubic yard from a shredder is higher than from a grinder, because the shredder doesn't fluff up the material as much as a grinder," says Pickhardt. This distinction can be important when considering storage, transport, or downstream processing needs.
The slower processing speed of shredders also requires a different approach to loading materials compared to high-speed grinders. Shredders are typically loaded directly on top of the shredding chamber, whereas grinders generally have an infeed system with a feed hopper. Understanding the differences in operation can help maximize efficiency and ensure optimal machine performance.
Slow-speed shredders are particularly efficient in handling municipal solid waste (MSW), making them ideal for waste management facilities that deal with contaminated waste streams.
Why shredders are gaining popularity
As shredders continue to gain traction in the wood waste recycling industry, their advantages in efficiency, durability, and versatility make them a valuable asset for processors looking to optimize their operations. Some of these benefits include:
1. Fuel savings
Shredders are designed to work with less energy consumption, using approximately one-quarter of the fuel required by a grinder. This can lead to long-term savings, especially for operations running machinery for extended hours.
2. Reduced maintenance costs
With fewer moving parts, shredders are generally more affordable to maintain than grinders and are often the more cost-effective option for smaller operations that don't require the fine output provided by grinders. Wear parts also last longer in a shredder, with wear rates being about one-third of those of a grinder.
3. Versatility
Shredders offer a high degree of flexibility, capable of handling a wide range of materials beyond wood waste. Shredders can process a variety of materials in one machine, allowing companies to consolidate their equipment and save space and money. Grinders, on the other hand, are more specialized and generally require a higher level of maintenance when processing non-wood materials.
4. Ease of operation
Shredders are often simpler to operate than grinders, especially when it comes to adjusting the output size or switching between different material types. With their more straightforward design, shredders can be a more user-friendly option.
Working in tandem or alone
Shredders are frequently used for primary size reduction, breaking down materials before they're processed further by a grinder. However, in some cases, a shredder can eliminate the need for a grinder altogether.
"Grinders could be eliminated in special applications dependent upon the size requirements of the finished product," says Pickhardt. "Some shredders, like Eggersmann shredders, have the option for a screen basket system to make a sized and consistent product."
When grinders are the better choice
Despite the growing popularity of shredders, grinders remain an essential part of many wood waste processing operations. For companies that require a finely ground, uniform product, such as mulch, wood chips, or sawdust, grinders are often preferred. Shredders, on the other hand, produce a rougher, more irregular output that may not meet the specific needs of these industries.
Sustainability benefits
As landfills become more crowded and regulatory pressure to divert waste increases, the ability to recycle or repurpose wood waste efficiently is critical. The consistent output of shredders is ideal for use in energy generation, composting, or as feedstock for other industrial processes, which are key to achieving higher diversion rates. Grinders are often limited in their ability to contribute to other recycling initiatives.
The right tool for the right job
While shredders are gaining traction due to their lower cost, flexibility, and environmental benefits, grinders continue to hold an essential place in high-volume, heavy-duty applications that demand precise, uniform output. In the end, the decision comes down to the type of wood waste, the desired end product, and the long-term strategy of the company. Both types of equipment will continue to coexist, and the real question is how businesses can effectively integrate both into their operations.