The paradox of paper recycling
Although paper is easily recycled, it’s still the most prominent material in municipal waste streams
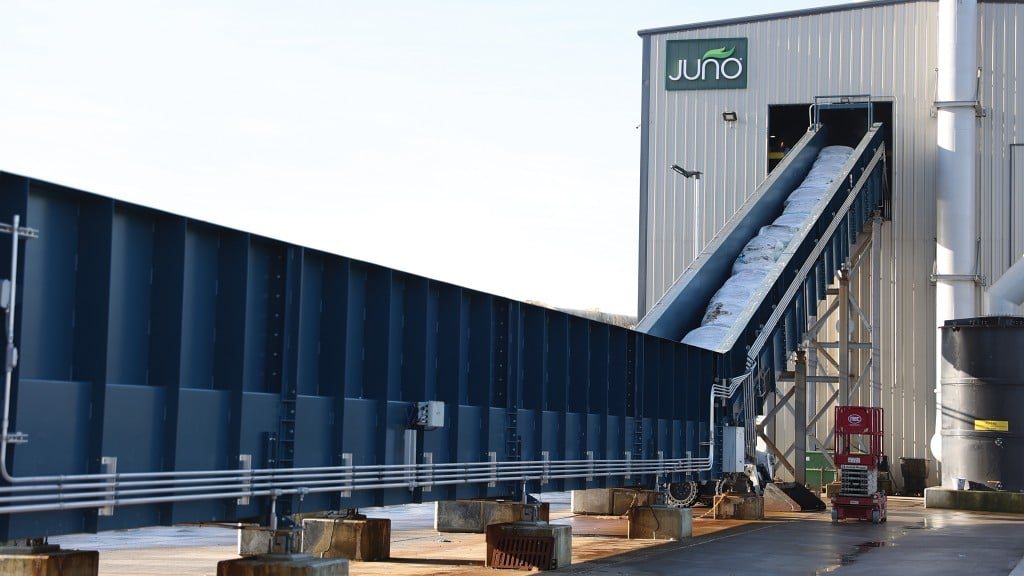
Paper is a perplexing commodity in the recycling market. It's the easiest recycled material, although it remains the most prominent recyclable material found in our municipal waste stream: this is the paradox of paper.
Paper and corrugated cardboard are incredibly common and versatile materials. Hardly a day goes by without a human interacting with a paper product; whether it's reading a local newspaper, receiving a package, grabbing a morning cup from a favourite coffee shop, or picking up takeout for a family dinner, paper is everywhere. Despite the best efforts from every corner of the industry to keep paper out of garbage cans and landfills, it still ends up there.
Waste stream issues despite ease of recyclability
Unlike other consumer materials, paper is relatively easy for consumers to recycle, which can explain why paper boasts one of the highest recycling rates. So, the prevalence of paper and paper-based products in our landfills tells us that there are other barriers at play.
According to the Environmental Protection Agency (EPA), paper and paperboard make up 23.1 percent of all generated municipal solid waste, but recycling rates vary dramatically based on how the paper is used by consumers.
For example, in 2018 — the last year data is available — newspapers had a recycling rate of 64.8 percent, while only 20.8 percent of paper containers and packaging were recycled. Meanwhile, an impressive 96.5 percent of corrugated boxes were recycled. This data tells us that, despite consumers being willing and capable of recycling high volumes of paper, 17.2 million tons of paper and paperboard still found its way to landfills.
Issues with limited infrastructure
Clearly, barriers still exist for collecting and recycling paper. Like other commodities, contamination and technology limitations are major challenges that reduce paper's recyclability.
Municipalities and solid waste programs, as well as paper producers around the world, have tried different approaches to enhance paper recycling rates. Cities like Seattle and San Francisco mandate the use of recyclable or compostable single-use food service packaging. Major food and beverage brands are also working to reduce plastic packaging and replace it with compostable materials.
Increasing the use of compostable materials could be helpful to reduce the use of some materials, like plastic. However, the infrastructure to handle post-consumer compostables is very much in its infancy. To date, only 143 composting facilities in the U.S. (about 16 percent) accept packaging in addition to food waste. Meanwhile, only 27 percent of the U.S. population has access to a curbside or drop-off composting program.
While composting can be part of the solution, especially for hard-to-recycle materials, access remains a significant barrier for most consumers.
Contaminated material with food-soiled fibres
Luckily, waste diversion technology has advanced and is proven to greatly reduce the barriers to recycling and reusing paper. One of the most prominent sources of contamination originates from paper used in food and beverage containers.
For example, pizza boxes are contaminated with grease, and paper cups have plastic films that prevent the liquid from seeping through. While recycling these products has historically been challenging, the paper fibres remain recyclable.
Until recently, landfills were the only destination for these products. The recycling system did not have an efficient means of cleaning and separating contaminants from the paper fibre; that all changed with the development of advanced waste diversion technology.
Advanced waste diversion technology — like Juno Technology, a patented autoclave process — uses heat, pressure, and steam to clean, decontaminate, and separate paper fibres from other materials in the solid waste stream. Clean paper fibres are then available to be used in recycled paper products.
However, recovering paper fibre from the waste stream is just the first hurdle to clear. The second is ensuring that the fibres recovered from municipal solid waste (MSW) can be effectively reused in recycled paper products and ultimately used in products that meet Food and Drug Administration (FDA) standards for food safety.
The fibre collected is used to make paper at Georgia-Pacific's nearby containerboard mill and has been deemed safe for food contact in the U.S. This process is a game changer for consumers because paper-based food packaging can now be recycled just like a newspaper or junk mail with very little education or shift in behaviour.
Sustainable packaging for everyone
Today, many consumers can purchase items with compostable packaging. But, if you are one of the 85 percent of Americans without access to curbside or drop-off composting, it's likely that your compostable packaging will end up in a landfill. That's because compostable packaging doesn't break down in a typical backyard compost bin. Most compostable materials, especially those labelled "commercial compostable only," need a higher level of industrial processing to break down.
For a quarter of consumers, mostly in dense urban areas, this isn't necessarily a problem because they have access to commercial composting programs. But a vast majority of consumers still want sustainable packaging and need an alternative to commercially compostable packaging.
Clean recyclables are still recycled. Yard and food waste are still separated for composting where it's available. Most importantly, wet or dirty paper and cardboard, like the greasy pizza box or used to-go coffee cup, are still disposed of in the curbside garbage. The difference is that advanced waste diversion technology can process the solid waste stream to clean, sanitize, and recover high-value materials and paper fibres before they end up in landfills and is designed to integrate seamlessly into curbside solid waste processes.
Brewing innovation
Waste diversion technologies are evolving. The solid waste and recycling industry is continually searching for more efficient and effective methods to collect valuable materials. Technology like optical sorting, electromechanical sorting, and anaerobic digestion have made resource recovery more approachable for the solid waste and recovery industry.
Juno's parent company, Georgia-Pacific, has a long history of using recycled fibres to make paper-based products and leans on its more than 50 years of experience in recycling as one of the largest traders of recyclable commodities. As a papermaker, Georgia-Pacific recognized that paper fibres and other materials being sent to landfills still held value, but the necessary technology to clean and sanitize them did not yet exist.
In 2010, research started to develop a technology that could recover paper fibres. After over a decade of research, the autoclave-centred technology was born and ready for testing. While proving the capability to process municipal solid waste was always the end objective, the initial goal of the project was to first test the technology on commercial waste from office parks, food courts, and quick-serve restaurants — particularly focused on disposable, single-use coffee cups. These waste streams would be naturally high in paper fibre products and would provide a perfect opportunity to test the autoclave on fibre-rich waste and evaluate its recyclability.
In 2021, the COVID-19 pandemic was raging and people worked from home as office buildings sat empty which meant that the commercial waste stream shifted over into the residential waste stream. Because research is rarely linear, the project pivoted, and the residential portion of municipal solid waste became the primary feedstock at the outset.
After initial testing, operations were scaled to demonstrate viability on a commercial level. The modular 70,000-ton-per-year unit ran on a 24/7 work schedule for almost two years and nearly tripled the community's local diversion rate.
The plant processed MSW while diverting fibre, food, and metals away from landfills. Future installations will leverage optical sorters to recover plastics in addition to anaerobic digestion to turn food into renewable biogas on-site to divert up to 90 percent of the municipal waste it processes away from landfills and incinerators.
Future-focused solutions
The COVID-19 pandemic did much more than alter waste diversion research — it fundamentally shifted consumer waste generation. One study published by the National Institutes of Health found in a survey of 23 countries that food waste increased 43 percent. Meanwhile, in Ontario, residential garbage increased 15 percent.
While it is widely accepted that waste generation was expected to increase temporarily, the pandemic will likely have a lasting impact on where and how that waste is disposed of. As more employees continue to work from home or in hybrid work arrangements, residential recycling programs will likely continue to see higher waste generation rates.
The recycling industry will likely feel these shifts for years to come. The one clear thing is the need to create a more flexible solid waste management system capable of recovering and diverting high-value materials directly from both commercial and residential MSW.
Now is a critical moment in time for more effective waste diversion strategies to align with consumer demand and generating new sources of recyclable content for paper-based packaging. Additionally, advanced waste diversion expands access to paper fibres once thought to be unrecyclable and technological progress now allows food-safe paper-based packaging to be made from multiple sources of recycled fibre.
Material users, manufacturers, and consumers should keep researching, innovating, and implementing new advanced diversion technologies. By expanding recovery capabilities within the curbside waste system, access to material recovery can be expanded without forcing significant system changes or intensive alterations to consumer behaviour.
Christer Henriksson is the president of Juno, a Georgia-Pacific-owned company. Prior to leading the Juno team, he spent 12 years modernizing Georgia-Pacific's recycling operations and leading the development of innovative recycling technologies. Before joining Georgia-Pacific, Christer served as SVP and COO of American Fiber Resources International, a multi-recycled-pulp mill entity. Christer can be reached at chenriks@gapac.com or on LinkedIn @ChristerHenriksson.