Textile fibre database enables more rapid and efficient fabric recycling
This information can be used to train and test sorting algorithms to improve efficiency
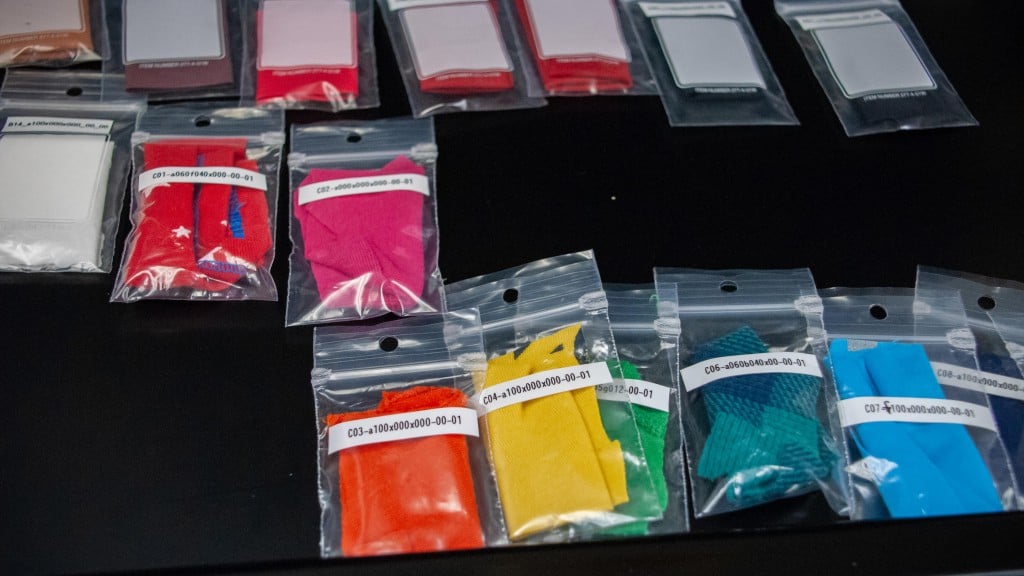
According to the David Suzuki Foundation, worldwide, people consume 80 billion new pieces of clothing every year — a 400 percent increase from 20 years ago. What happens to all that "fast fashion" — trendy, low quality clothing — after it quickly goes out of style?
In 2018, the Environmental Protection Agency (EPA), found around 85 percent of used clothes and textiles were sent to landfills and incinerators. This wastes precious resources and pollutes the environment in North America, and also in developing countries where many of the clothes end up after they are donated to charity. One reason is that recycling can be more expensive than landfilling, so companies have little incentive to recycle.
To help solve this problem, researchers at the National Institute of Standards and Technology (NIST) have developed a database that contains the molecular "fingerprints" of different kinds of textile fibres and that can enable more rapid, efficient sorting of fabrics at recycling centres.
"This reference data will help improve sorting algorithms and unlock the potential for high-throughput sorting, which requires less manual labour," says Amanda Forster, a NIST materials research engineer. Forster leads the NIST project focused on keeping end-of-life textiles in the economy, a process called textile circularity. "That should reduce costs and increase efficiency, making textile recycling more economically viable."
Fast fashion's business model entails companies churning out large volumes of inexpensive clothes that are often quickly discarded. New types of textiles, blended textiles, and incomplete or inaccurate labeling also pose significant challenges when it comes to sorting textiles at recycling centres.
The role of near-infrared spectroscopy
At those centres, workers sort clothing using handheld, near-infrared light devices that measure how much of the light passes through or scatters off the fabric, producing a unique pattern — a sort of fingerprint that can identify the type of fibres in the clothing. This technique, called near-infrared (NIR) spectroscopy, can also be used in automated conveyor belt systems. However, current techniques still require a lot of manual labour.
In recent years, recycling equipment manufacturers have increasingly used machine learning and artificial intelligence to improve their sorting algorithms. To train these algorithms, they need high-quality reference data.
That's where NIST's database comes in. Called the Near-Infrared Spectra of Origin-defined and Real-world Textiles, or NIR-SORT, it contains 64 different fabric types along with the NIR fingerprints they produce. The database includes pure fibre types, such as cotton and polyester; blended fibre types, such as spandex blends; and real-world fabrics taken from thrift stores. Manufacturers of NIR scanner systems can use this database to train and test their sorting algorithms and improve the performance of their products.
"The difficulty comes in when fibres are similar, like cotton or hemp. That means that the near-infrared signal is similar. The same is true with a cotton and polyester blend. Is this a new fibre or a blend of two or more fibres?" says NIST research chemist Katarina Goodge, who led the development of the database. "AI can help make the decision-making process more accurate."
Because NIST is the nation's measurement institute, it has the equipment and expertise to fill this database with very high-quality spectra. That will hopefully mean fewer errors when identifying fabrics, and more textiles getting recycled.
This research stems from a key initiative of a report by NIST in which experts recommended the development of better technology for identifying and sorting textiles and clothing. These efforts are part of NIST's Circular Economy Program, which develops measurement science and methods to support an economy where materials are designed to retain their value through repeated reuse, repair, and recycling, with disposal as a last resort.