Recycling pilot project diverts and upcycles plastic waste from construction sites
The Construction Plastics Initiative tests the feasibility of a circular economic model for plastic from construction sites
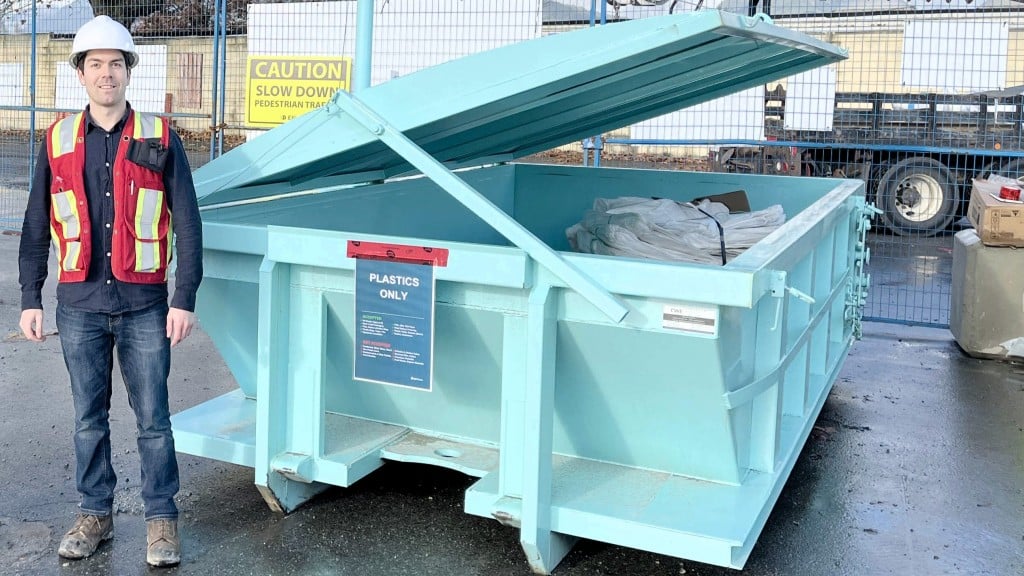
Light House, a B.C.-based organization focused on sustainable construction practices, has launched a new initiative aimed at diverting and upcycling plastic waste from approximately 10 Metro Vancouver construction sites. The pilot program, The Construction Plastics Initiative, is running now until February 2026 and is actively seeking projects to bring on board.
"Currently, there is a lack of comprehensive studies in North America quantifying the volume of construction plastic waste directed to landfills," says Gil Yaron, managing director of circular innovation for Light House. "Studies from Europe suggest approximately 80 percent of plastic waste from on-site construction activities consists of clean packaging materials, which are readily divertible from landfills. This pilot project aims to provide valuable insights into the extent of construction plastic pollution in North America and to identify opportunities for circular innovation in managing construction plastics."
The program's objective
The objective of the Construction Plastics Initiative is to demonstrate the feasibility and financial viability of a circular economic model for plastic waste generated on construction sites. The intention is to collect, separate, measure, and process plastics from construction sites to determine the amount and types of plastic waste being generated in British Columbia's construction sector, and to demonstrate circular economic solutions to divert and repurpose the plastic into new products. Project participants will be able to showcase their leadership by pioneering plastic diversion and using the locally manufactured building products in their projects.
"In Canada right now, virtually all of the plastic generated on these construction sites is ending up in landfill or being buried on site," says Yaron. "There's a better solution — and we're testing it out right now. We're bringing partners together through the construction plastic value chain, developing a management framework to collect, monitor, and track the flow of materials, and we're exploring the business case and sale of derivative building products back into the construction sector."
Collected plastics from all projects will be processed by Ocean Park Recycling before being recycled into a reusable plastic pellet, which will be integrated into the manufacturing of a range of new building products. The pilot program will help developers and general contractors reduce material use and the embodied carbon associated with their projects. Through this initiative, Light House is not only reducing the environmental impact of construction but also preparing the industry for the federal government's upcoming plastics registry reporting requirements in 2026 — helping to set a new standard for sustainability in construction.
How the Construction Plastics Initiative program works
A qualified site monitor will be provided to the participating construction project. The site monitor will work with the general contractor and site supervisor to identify the types of plastics to be collected, schedule collections based on the construction timeline, provide size-appropriate collection bins, train site crews on proper source separation practices, monitor bins for contamination, and assist with the delivery and removal of collection bins, as required.
"By establishing a comprehensive network between developers, contractors, recyclers, and manufacturers, and focusing on upcycling, Light House's innovative project will help address one of our most pressing priorities: reducing waste from the construction and demolition sector," said Sarah Kirby-Yung, Chair of Metro Vancouver's Zero Waste Committee. "As leaders in waste reduction with one of North America's best recycling programs, Metro Vancouver recognizes the importance of supporting such initiatives to reduce construction plastic waste."
Example of end use: InfinaNet
InfinaNet is a cost effective and sustainable voided concrete solution specifically designed for floor and wall slabs. Replacing non-structural, dead-weight concrete with InfinaNet in traditional slabs uses less concrete, is lighter, and performs better than solid slabs. Concrete production is one of the world's leading carbon dioxide emitters. By using less concrete in the project, there are less emissions without compromising the structural integrity of the build.
"InfinaNet slabs are not only cheaper than every voided concrete system currently on the market, but our InfinaNet system is your complete void solution," said Manveer Pattar, president of Infina Technologies. "InfinaNet offers a void, rebar support, and chair all in one. This innovative design makes installation faster and cheaper, eliminating the need for additional steel cages, and individual installation."
To learn more about the Construction Plastics Initiative, please visit light-house.org/cpi. If you are a developer or general contractor, contact Light House directly to get involved.