New food waste depackaging system installed in Sunnyvale, California
The system uses Van Dyk Recycling Solutions equipment including a Keith walking floor, a SMIMO120 depackager, and SMIMO15 grinder
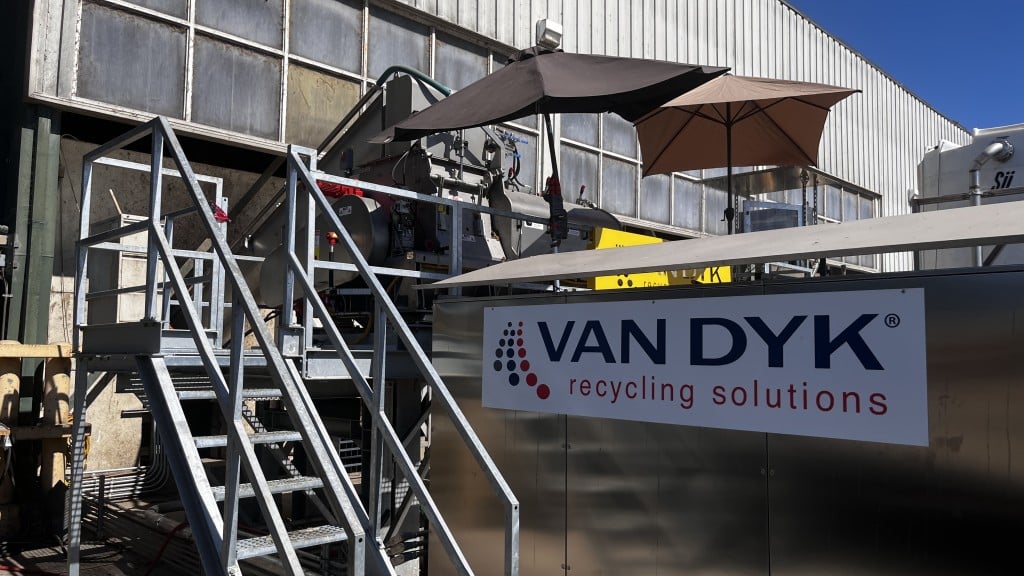
The City of Sunnyvale, CA, has replaced their entire food waste depackaging system to comply with California's SB1383 mandate to divert organic waste from landfill. Completed during the summer of 2024, the new system increases storage capacity by 60 percent, increases recovery of organics from the waste stream, and reduces truck unloading times. This project was funded through the CalRecycle Organics Grant Program, Cycle 5.
The new facility accepts both commercial source separated organics (SSO), including waste from restaurants and other businesses that generate food waste, and residential SSO via a curbside collection program in Sunnyvale. The system currently runs 18-20 tons per hour or more, up from previous capacity rates of 15 tons per hour, while achieving greater than 85 percent recovery of organics. The resulting organic slurry is sent to wastewater treatment facilities.
The equipment was supplied by Van Dyk Recycling Solutions and includes a 10-12 ton storage and feed bunker; a Keith walking floor for extra storage capacity and quality control; a SMIMO120 depackager, which acts as the primary separator; a SMIMO15 grinder for further processing; and pumps and conveyors to transport the material between units.
The in-ground feed bunker allows hauling trucks to back up and unload directly into the bunker, expediting the time for trucks to empty (average unloading times are currently around five minutes). The infeed bunker is equipped with three shaftless screws acting as a preliminary mixer to create a homogenous feed for the SMIMO120 depackaging unit. Screws have a shaftless design to resist wrapping of contamination. The material is then conveyed to a walking floor for visual inspection prior to the depackager. Any bulky, non-organic contamination is easily spotted and removed from the walking floor, and no other presorting is required.
Material from the walking floor is metered into the SMIMO120 depackager, where a rotating 360 degree steel drum liberates the organics from any packaging and turns it into a high-quality organic slurry. A dewatering pump at the primary bunker delivers excess liquid from the bunker to the SMIMO120, eliminating the need for an external water source to process the material. The packaging is expelled and conveyed to residue. The slurry is further processed by a SMIMO15 grinder, which prepares the material for wastewater treatment facilities by sizing it down to less than half-an-inch and removing the last bits of grit and glass.
A series of pumps and storage tanks between each processing step helps keep throughput at its maximum. The mid-system tanks constantly accept and meter out material, so it flows seamlessly from one unit to the next, avoiding any bottlenecks.