Wear part innovations for mobile waste shredders
Adapting to diverse material streams requires customization and modularity
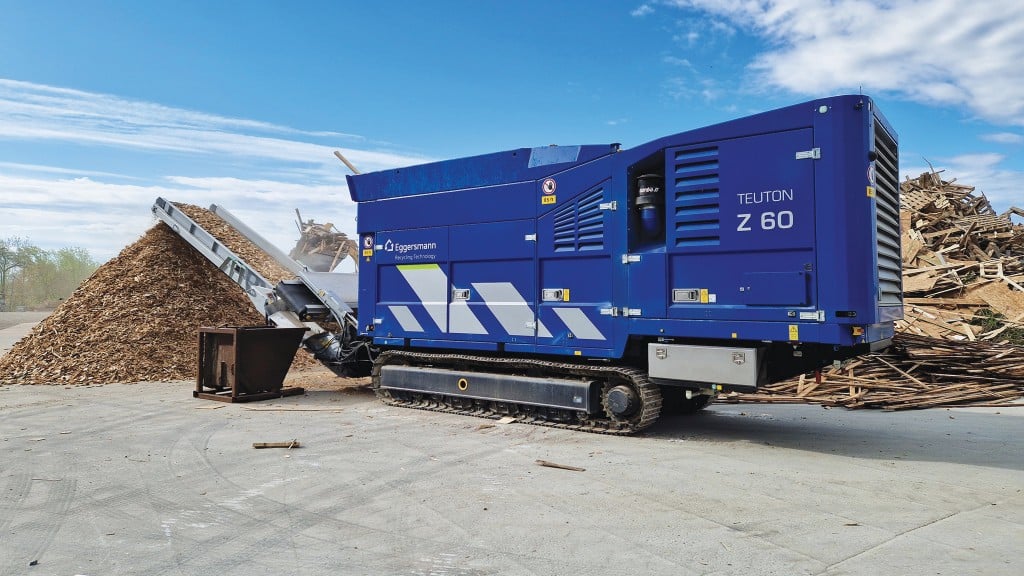
Modular rotor and tool systems have revolutionized mobile shredders, allowing operators to tailor machines for the specific materials they process. This customization not only enhances machine performance but also extends the lifespan of components.
Mobile shredders, known for their versatility, are critical in processing materials ranging from construction debris and plastics to metals and green waste. Their adaptability has made them indispensable for applications like waste-to-energy plants, municipal recycling facilities, and scrapyards.
Whether they're reducing bulky items for easier transport or preparing waste for further processing, mobile shredders are an adaptable solution for the ever-evolving demands of recycling operations.
Operational challenges
Despite their benefits, mobile shredders can face significant operational challenges. The constant shredding of abrasive and hard materials takes its toll on critical components like rotors, cutting teeth, and screens. Wear and tear are inevitable, and without efficient maintenance, repair costs can quickly skyrocket.
Traditionally, these issues have been a persistent struggle for operators. Replacing entire rotors or drums when teeth or knives wear down is a common but costly and time-consuming process that can lead to extended downtime. To address these concerns, manufacturers are placing greater emphasis on aftermarket solutions that extend the lifespan of mobile shredders. From modular designs that allow for the quick replacement of wear parts to smart technology that proactively monitors equipment health, manufacturers are paving the way for a new era of more resilient and versatile mobile shredders.
Innovations in wear parts
Wear on critical components like teeth and rotors is one of the biggest challenges in mobile shredding operations. Traditionally, machines required full rotor or drum replacements when these components wore down, leading to extended downtime and expensive repairs.
Manufacturers like Terex Ecotec and TANA have made advancements to combat this issue, focusing on replaceable parts that extend machine life and minimize operational disruption. Terex Ecotec's replaceable, bolt-on shredding teeth allow operators to replace only the worn teeth instead of the entire rotor. TANA's shredders feature individually replaceable rotor teeth and counter knives which similarly reduces the need for full overhauls, helping operators save on maintenance costs and improve overall efficiency.
Manufacturers like Viably (formerly Komptech) and Eggersmann have developed innovative ways to reduce wear. Viably's slow-running drums produce less friction and heat which reduces wear on critical parts, and their quick-change systems allow for screen baskets and tools to be replaced easily.
Eggersmann, on the other hand, offers slow-running shredders that avoid the need for the protective measures often required by high-speed machines. Their shredders reverse automatically when an obstruction is detected, protecting wear parts from damage. If larger obstacles are encountered, the shredding process halts automatically, signaling the operator to address the issue. This proactive maintenance system extends the overall lifespan of their machines.
Modular systems for shredding efficiency
Modular systems are transforming mobile shredders by providing flexibility and customization, allowing operators to configure machines based on the materials being processed. Viably's modular design allows operators to adjust settings depending on the type of material, reducing unnecessary wear on parts that don't need to work as hard. This customization helps the machine perform more efficiently across a variety of materials, improving its longevity.
Eggersmann's shredders also benefit from a modular setup with customizable cutting gaps and screen baskets, which enhance precision and reduce the need for secondary shredding. Their machines feature automatic rotor reversal when obstructions are detected, adding a layer of operational safety while extending part life.
Proactive maintenance with technology
In an era where efficiency and reliability are paramount, the integration of smart technology into mobile shredders is an obvious choice. The TANA ProTrack monitoring system provides real-time data on rotor performance and alerts operators when parts require replacement, preventing unexpected failures that could lead to extended downtime.
Similarly, Terex Ecotec's T-Link telematics system monitors machine performance, location, and operational data, allowing operators to track metrics such as fuel consumption, operating hours, and maintenance schedules. The system also facilitates remote diagnostics, ensuring that any issues can be addressed quickly and efficiently.
Viably also utilizes predictive maintenance algorithms in its Connect! system which streamlines administration, optimizes deployment planning, and facilitates remote machine monitoring. This system allows for targeted service when issues arise and provides real-time analysis for enhanced operational insight.
This trend of implementing monitoring systems is gaining traction across the industry, allowing shredding operations to reduce downtime and improve operational efficiency, which ultimately results in lower operating costs and increased profitability. The intuitive control systems from various manufacturers empower operators to monitor wear part usage and machine performance, make informed decisions, schedule maintenance at optimal times, and avoid costly breakdowns, ensuring smooth operation over extended periods.
The future of mobile shredders
As the recycling industry works to meet ambitious sustainability targets while processing an ever-expanding range of materials, the aftermarket for mobile shredders will be key to driving more efficient waste management.
With technology advancing rapidly and the need for higher throughput growing, the future will see mobile shredders equipped with even smarter, more resilient systems that improve performance, extend the lifespan of critical components, and minimize downtime.
The integration of predictive maintenance and smart technology will give operators real-time insights into machine health, allowing them to make data-driven decisions that keep operations running smoothly. These technologies will make shredders more reliable and better suited to handle the increasing complexity of recycling applications.
Modular wear parts will become more commonplace, simplifying repairs and enabling operators to tailor their machines to specific materials, reducing costs and boosting productivity. As manufacturers continue to innovate, mobile shredders will evolve into more adaptable and efficient tools, ensuring the recycling industry can keep pace with growing demands.
Company info
22 Whittier Street
Newton, NH
US, 03858
Website:
terex.com/ecotec
Phone number:
603-382-0556