Feess repurposes over 90 percent of C&D waste using Kleemann crusher
Old buildings are recycled on-site by a mobile impact crusher for sustainable new building materials
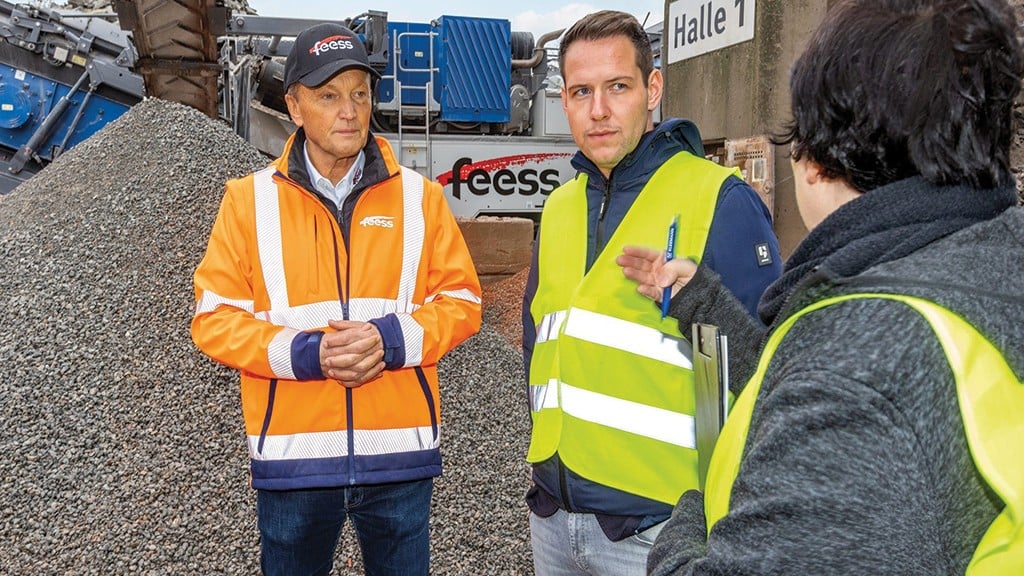
In Baden-Württemberg, Germany, an old district administration building had reached the end of its useful life and was being demolished. Instead of trucking the demolition material away to a landfill, Heinrich Feess GmbH & Co. returned over 90 percent of it to the low carbon building cycle.
Feess — whose core business is earthworks, demolition, and recycling — utilized a Kleemann MOBIREX MR 130i PRO mobile impact crusher to complete the majority of the recycling processes on-site. Feess tested the plant for Kleemann at the end of its development phase and was so impressed they decided to keep it.
Upgraded to serial production standards, the mobile imact crusher plant now plays an important role in the company's overall operations and contributes to its low carbon operations.
Technology for eco-friendly demolition and recycling
"For us, the [mobile impact crusher] is an extremely important component in the concrete demolition rubble processing chain. Up to now, we had one Kleemann impact crusher in operation," says Feess. "We used the smaller MOBIREX MR 130i EVO2 together with a separate screening plant. We still use the MR 130i EVO2, sometimes on the actual project sites. The compatibility of the parts is a practical aspect that makes it easier for us to store and organize the spare and wear parts we need."
The MOBIREX MR 130i PRO mobile impact crusher processes concrete demolition material and mixed rubble to produce materials such as mineral aggregates for low carbon materials and concrete.
"This meant that the aggregate for the [recycled] concrete for the new district administration office was produced from the construction materials reclaimed from the old building. In other words, we turned old into new," says Feess. "The largest proportion of the mineral construction materials was crushed directly on the construction site or at our recycling depots at a rate of up to 1,800 tons a day. The experience we gathered here is something I'd like to pass on, including to our competitors."
Using the MOBIREX MR 130i PRO was also cost-effective, according to Feess. Consolidation of crushing and screening functions into one machine reduces the need for multiple units, saving on fuel and maintenance.
According to Feess, the low fuel consumption, the high output, and the extremely efficient double-deck post-screening unit are key to cost efficiencies, as well as space saving.
"Space is at a premium here, and with this plant, we get two machines in one. We used to use a crushing plant followed by a separate screening plant — now, thanks to the high performance and the ability to discharge two classified final products, the MR 130i PRO is just what we need. It also means that we now only have to operate, service, and refuel one machine in our daily routine," says Feess.
In terms of fuel, it makes a clear difference to the bottom line. "The fuel consumption of the new MR 130i PRO is about the same as that of the MR 130i EVO2 we were using before. However, in the past, we had to refuel the screening plant as well. That meant another 14 to 16 litres of fuel. Today, we no longer need this extra fuel. And that's not all: the MR 130i PRO brings us up to 20 percent higher output, which is pretty amazing when you consider its fuel consumption."
Fuel and material prices will continue to increase due to scarcity and the carbon dioxide tax, according to Feess. "Recycling processes will also have financial benefits in the long run. To me, it is perfectly clear that we will not be able to achieve our environmental goals without a narrower focus on the establishment of strong recycling management."
The future is electric
The company is working toward further lowering emissions through electrification. Says Feess, "As the new setup is saving us 14 to 16 litres of fuel a day. We are already seeing a massive reduction of many tons of carbon dioxide. The option of operating the plant with electric power was a decisive factor for us. However, for this purpose, we have to expand our transformer station, that is, the power supply. We are already discussing a number of ideas for the realization of this. We are also considering expanding the overall area of our photovoltaic power generation systems. It would be great if we could run the plant at least to some extent with electricity from our own renewable energy sources."
According to Kleemann, fully electric plants are the future of the industry as they provide medium-term cost benefits in addition to practical and lowering carbon emissions.
With electric mobile plants, end users can position themselves on the market as future-oriented providers. Although the initial investment costs are higher, the company says they are quickly balanced out due to the fuel savings. A sample calculation for the German market showed that it's possible after around six years — if the plant can be supplied with energy via the customer's own photovoltaic system, it can pay off after around four years.
Electrification advocates understand that careful planning is required to maximize the benefits of using electric machines. Tobias Möß from Wolff & Müller GmbH says, "First of all, the actual energy requirements of the plant and that of all already existing consumers should be determined. How much power is needed on the entire company premises? The load profile must also be taken into account. When are the power peaks, when are the times with lower consumption? The individual load profile can be obtained from the power supplier or network operator."
Tobias Böckle, head of product management at Kleemann, lays out one practical application.
"Our mobile plant train in the sample calculation consists of a jaw crusher MOBICAT MC 120 PRO, cone crusher MOBICONE MCO 110 PRO as a secondary crushing plant, and a downstream screen machine MOBISCREEN MSC 953 EVO. The plant train consumes an average of approximately 77 litres of diesel fuel per operating hour. In the electrified version, it has an average fuel consumption of 302 kilowatts per operating hour. The maximum power requirement is 542 kilowatts. The energy requirement must first be met by the infrastructure and, ideally, by electricity from renewable energy sources. The power supply from the company's own photovoltaic system is sustainable and a very fast cost-efficient solution."
At the end of the day for Feess, it all comes back around to educating people about the possibilities, and he believes in the importance of his mission.
"It's clear that we have to act now. There is no point in merely talking about having to get a grip on carbon dioxide emissions. We owe it to our children and grandchildren to take action now and create corresponding legal and normative bases. But the great thing is that we already have the capabilities, the technology, and the expertise — all we have to do is use them. I will never tire of appealing not only to architects and engineers but also to local authorities and administrative bodies."
Company info
6030 Dana Way
Antioch, TN
US, 37013
Website:
wirtgen-group.com/america/en-us/products/kleemann
Phone number:
(615) 501-0600