LRS facility reshapes how recyclables are processed in Chicago
Operating at a capacity of 25 tons of recyclables per hour, the MRF is enhancing waste diversion efforts in the Midwest
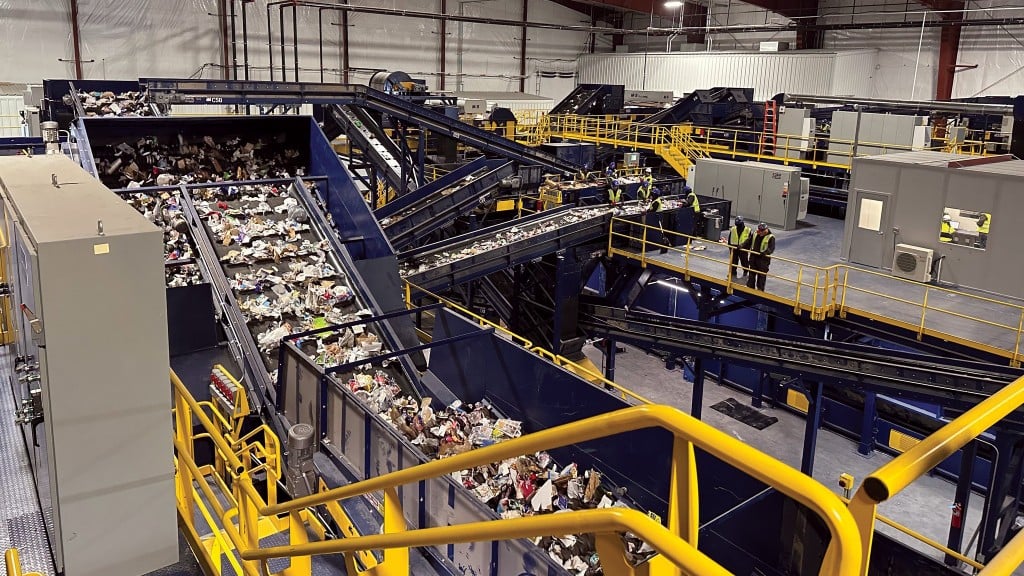
In the heart of Chicago's historic Stockyards neighbourhood, a game-changing facility is transforming the future of waste management. The Exchange, LRS's latest material recovery facility (MRF), is reshaping recycling practices across the Midwest.
With a holistic and innovative approach to single-stream recycling, the Exchange is not just another MRF; it's a symbol of forward-thinking solutions designed to minimize environmental impact. Operating at a capacity of 25 tons of recyclables per hour — with plans for future expansion to 35 tons per hour — the facility is already making waves in waste diversion efforts.
LRS stands as North America's fifth-largest privately held waste and recycling company, playing a crucial role in advancing sustainable waste management practices. Since 2013, LRS has delivered comprehensive, fully integrated waste diversion and recycling services to thousands of residential, commercial, and construction customers across eight states. With a service portfolio that includes roll-off container rentals, construction and demolition (C&D) recycling, portable restrooms, street sweeping, and more, LRS has rapidly expanded its reach and impact.
The vision
The Exchange was conceptualized when a merger between Recycling Systems Incorporated and Lakeshore Waste Services sparked the idea for a state-of-the-art materials recovery facility in Chicago. The vision was clear from the beginning: to build a high-tech, high-capacity single-stream facility that could handle the growing volume of recyclables in the Chicagoland area. By 2021, the project gained significant momentum when the company secured the City of Chicago's Blue Cart recycling contract.
Construction of the facility began in the Stockyards, close to the company's existing truck yard to reduce traffic and emissions. This strategic location optimized operational efficiency, with trucks now able to tip materials and park nearby, decreasing fuel use and environmental impact. A $50 million investment with critical capital support from trusted stakeholders expedited the opening of the facility in 2023.
The recycling process at the Exchange begins when trucks arrive and are weighed at the scale house to determine the incoming material's tonnage. The recyclables are then unloaded onto the tipping floor, where a fully electric material handler transfers them onto a conveyor belt. The material first encounters an auger screen that sorts items based on size, allowing larger items to pass over while smaller items, such as bottles and jars, fall through. These smaller items hit a glass breaker, with glass separated using a cyclone separator. The larger materials are directed to a post-sort area, where employees remove contaminants and bulky items.
Subsequent sorting involves screens that differentiate between two-dimensional and three-dimensional objects, with optical sorters and a giant drum magnet that captures ferrous metals. An EverestLabs AI robot monitors the last chance line to recover any aluminum cans and plastic bottles that may have been missed.
Finally, sorted materials are compacted by balers and stored before being shipped to factories and mills for recycling, with an average of 80 percent of materials being recycled successfully.
Innovation by design
The Exchange facility's design and equipment choices were driven by a thoughtful and deliberate intent to streamline the recycling process.
"We were evaluating for efficiency, safety, and lead time," says Mark Molitor, VP of post-collection with LRS. "CP Manufacturing hit all those marks with their innovative CP auger screen."
This piece of equipment streamlines the sorting process by allowing only larger materials to move to the first sorting line, significantly improving safety and efficiency for workers. The same strategic thinking was used when choosing to purchase Harris balers to incorporate full redundancy; having two balers ensures continuous operation even if one malfunctions.
With the increased use and disposal of lithium-ion batteries, fire safety was another key factor in choosing equipment for the new facility. The team at LRS opted to install three Fire Rover systems. These systems utilize thermal imaging and smoke detection cameras to monitor high-risk areas, provide early alerts for potential fires, and activate on-site fire suppression measures. By integrating these high-tech solutions, the facility enhances its operational efficiency and safeguards the health and safety of its workers and the environment.
A holistic approach
In 2024, LRS's dedication to reshaping the recycling industry earned it the Recycling Facility of the Year Award from the National Waste & Recycling Association (NWRA). This award recognizes organizations that have profoundly impacted waste diversion efforts, celebrating their achievements and commitment while inspiring others in the industry.
The Exchange MRF was honoured for groundbreaking advancements in sustainability and innovation. But, perhaps more significantly, the award reflects LRS's holistic approach to waste and recycling. By prioritizing transparency and community involvement in the circular economy, the Exchange has become more than just a recycling facility — it's a hub for education and advocacy.
Circularity and transparency
One pillar of LRS's mission is a firm commitment to advancing circularity within the recycling industry. Circularity shifts away from the traditional linear model of resource use — where materials are mined, made into products, and ultimately discarded as waste — toward a system that emphasizes reducing material use and recapturing waste to manufacture new products. LRS recycles materials efficiently and redesigns processes to make recycling more accessible and effective.
"LRS was founded with the DNA of recycling," says Joy Rifkin, sustainability manager at LRS. "We ask: How can we recycle anything that can be recycled, and how can we connect with our communities to make sure that sustainability and customer satisfaction are foundational in what we do?"
This comprehensive approach to advancing recycling innovation means LRS is dedicated to stringent quality control measures and rigorous contamination management. The Exchange MRF employs a post-sort system, where team members are carefully trained to identify and manually remove contaminants, ensuring the cleanest possible end product for manufacturers.
"We have such good relationships with the mills and factories where we send this material because we deliver such a clean, uncontaminated product," Rifkin says.
These relationships are crucial in keeping the circular economy running efficiently, as uncontaminated recyclables are more easily converted into new products. LRS's carefully sorted and baled materials — known as recycling cubes — are stored, weighed, and sent to North American mills, where they are processed into new items, continuing the cycle of reuse and reducing the need to extract raw materials.
LRS has also partnered with the American Beverage Institute and the Can Manufacturers Institute (CMI) to improve beverage container recycling through its Every Bottle Back initiative. The EverestLabs AI robot, used on the facility's last chance line, captures overlooked aluminum cans to boost recovery rates and promote better community recycling practices.
"We work really hard to educate our communities on the fact that aluminum is infinitely recyclable and in under 90 days that beverage can can be back on your shelf with a new beverage inside it," says Rifkin.
Education is key
Ongoing education (both internal and public) and innovation are at the heart of LRS's operations. Team members attend industry conferences and collaborate with leading manufacturers and mills, ensuring they remain at the forefront of recycling innovation.
In this spirit, LRS has partnered with EverestLabs to test AI-driven robotic technology in the Exchange facility. By working with strategic partners to assess potential improvements in sorting accuracy and efficiency, LRS can remain on the cutting edge when implementing new technologies to optimize operations and help educate others in the industry.
As new trends in recyclability emerge — such as the ability to recycle paper cups — LRS works closely with mills to stay ahead of the curve and incorporate these materials into the recycling program.
As part of its front-facing educational initiatives, the team at LRS has designed a custom online tool at chicagorecycles.org, which provides transparency into the recycling process for Chicago residents. As Rifkin explains, "This is a super cool education tool and interactive map that really showcases our commitment to the city."
The tool allows users to zoom in on specific neighbourhoods, homes, or schools and see how recycling works at the local level. It outlines the city's recycling zones and the roles LRS plays in collecting recyclables from four out of six collection areas. The interactive platform also illustrates where different materials go after collection, showcasing the circular journey of recyclables. With updated data, LRS ensures that residents are informed and engaged in the city's recycling efforts, fostering a deeper understanding of and participation in sustainability initiatives.
Another community education effort involves welcoming the public to its facilities, showcasing the inner workings of an advanced recycling process. With an open-door policy, LRS has hosted hundreds of visitors from academia, government, industry, and community groups. In 2023, over 800 visitors toured the Exchange MRF, gaining first-hand insight into the complex operations behind modern green recycling.
"So many people don't realize in addition to machines and equipment that are maintained to ensure we can sort at a high level, there are actual human beings who have to deal with these materials," says Rifkin. By lifting the veil on recycling operations, LRS educates visitors and builds advocates for sustainability within communities.
LRS also plays a crucial educational role by providing annual recycling audits for the City of Chicago. By isolating each zone and breaking down the types of materials processed, LRS helps the city and its residents understand the recycling stream better. These audits offer a detailed view of contamination levels and material percentages, enabling the city to improve its educational outreach and refine its waste diversion strategies. This open exchange of information showcases LRS's commitment to creating a circular economy while building strong relationships with the communities it serves.
Through these multifaceted efforts — facility tours, annual audits, and interactive online tools — LRS exemplifies how transparency and education can drive better recycling outcomes and inspire a more informed and engaged community as it aims to drive the continued evolution of recycling practices.
The future of recycling
LRS has established ambitious long-term sustainability goals, focused on achieving net-zero operations by 2040.
"We have a board-approved, net-zero plan," says Rifkin. Key strategies to meet these goals include route optimization to improve efficiency, boost operational effectiveness, and reduce fuel consumption and emissions. LRS is investing in equipment electrification, incorporating technologies like fully electric material handlers and exploring alternative fuels such as compressed natural gas (CNG) and higher biodiesel blends for its fleet. These initiatives are complemented by ongoing education efforts aimed at engaging and informing the community about sustainability practices and the importance of recycling.
"The future of LRS is continuing this mission toward sustainable business operations," says Rifkin. "That means profitability. That means safety and protecting our people. That means our commitment to the environment. Growing the company across the Midwest in a sustainable and community-centred way is the future for LRS."
Plans for growth include expanding beyond the Chicagoland area and bringing expertise in high-tech facilities, impeccable customer service, and commitment to the communities where it operates.
Meghan Barton is a freelance copywriter who specializes in crafting engaging B2B content.