Redesigned Tigercat carbonizer features efficient material reduction, carbon sequestration
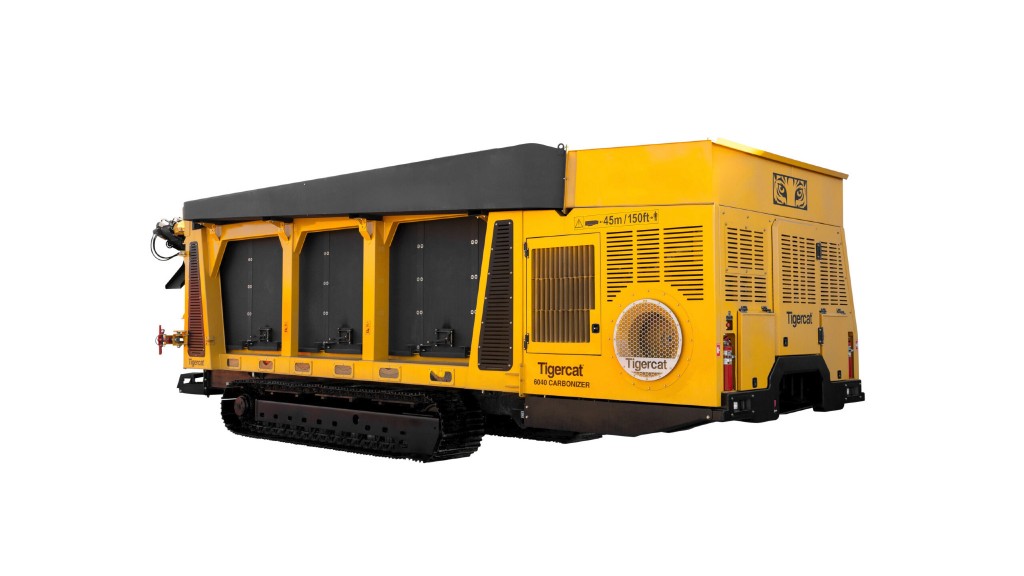
Tigercat Industries has released the 6040 carbonizer. This replaces the 6050 carbonator that Tigercat marketed after acquiring the product through the purchase of ROI in 2019. The mobile onsite wood conversion system is available after a full redesign of the 6050.
Tigercat says the 6040 is one of the most environmentally friendly wood debris reduction and conversion systems available. The machine inputs woody debris and produces organic carbon with up to 90 percent material reduction. It is an ideal solution for converting unwanted logging and agriculture residue into organic carbon that can be left on-site as a soil additive or marketed for commercial use. The process captures 20 to 30 percent of the available carbon in the feedstock and sequesters it. The conversion process operates at high throughput levels and produces low emissions because the gasses are combusted in the controlled combustion zone.
The 6040 redesign addresses performance-related issues experienced in the original design and represents the knowledge of the applications that Tigercat engineers and field support personnel have gained over the past five years.
Great care has been taken to create a machine that allows modular replacement over time. For instance, the grates in the carbonizing chamber are now made up of seven different sections that can be rotated 180 degrees to balance wear and extend life. Individual sections can be replaced as required. The undercarriage, auger trough, and conveyor system are all bolt-on sections to the main carbonizing chamber frame. Everything can be separated for service and replacement if required. The modular bolt-on design also allows for differing expansion rates of these major components.
The replaceable thermal ceramic panel seal plate design has been improved, reducing panel wear. The composition of the panels has been altered to decrease the back-face temperature while storing and utilizing more heat energy produced during the carbonizing process. This provides a more stable and sustained temperature within the carbonizing chamber.
The auger trough is designed for minimal air leakage, assisting with under-air efficiency, and further defining the secondary combustion zone, while reducing hotspots that could form from an inefficient base pressure or vacuum. Unlike the 6050, the auger trough, where the quenching process takes place, is entirely sealed. Once the organic carbon drops through the grates, it is fully quenched by the water bath. An onboard hydraulic water supply pump and integrated automatic water level control system reduce water consumption by about 50 percent compared with the 6050. Automated water fill, level control, and water retention provide the operator with a window of time to replenish the water supply if required.
The adjustable conveyor simplifies the handling and management of organic carbon products. It pivots 105 degrees from side to side and can be raised or lowered. The conveyor easily folds for transport and does not have to be detached from the machine frame.
Temperature control sensors are located throughout the machine. This, coupled with the Tigercat-designed operating software and telematics system, improves data access and support. The 6040 development also emphasized parts commonality among other Tigercat products including pumps, motors, valves, and filters, simplifying parts inventory management at the dealer and end-user levels.
The overall machine weight has been reduced from 43 550 kilograms (96,000 pounds) to 37 650 kilograms (83,000 pounds). Extended track frames improve load distribution on the trailer and reduce soil compaction on the ground.