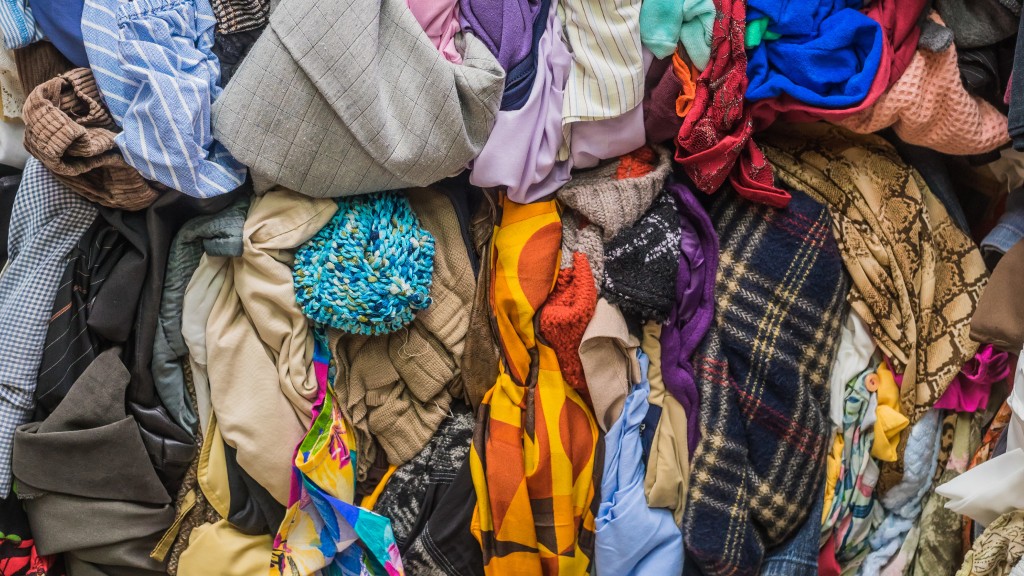
At the latest BIR Textiles Division meeting held in Copenhagen on May 29, a progress report on the journey towards a circular value chain for textiles was delivered.
Cyndi Rhoades, founder of Worn Again Technologies and co-founder of World Circular Textiles Day, said that the continuing predominance of a linear model for textiles based on virgin resources, adding what she described as the "quite shocking" statistic that less than one percent is being recycled into new textiles.
But "change is coming" and "technologies are on the way" to underpin the delivery of industrial-scale materials recycling, said Rhoades. Most important, she said, would be a move away from manual textile sorting to the development of automated sorting and pre-processing facilities (ATSP) capable of providing a low-cost, regional feedstock for fibre-to-fibre recycling. In the UK, she noted, the government had provided a grant of £4 million (around U.S. $ 5 million) for the development of an ATSP blueprint involving a consortium of 20 partners. The aim was for this facility to be up and running by the end of 2025.
While Rhoades acknowledged widespread concern over the time gap to creating processing plants, she insisted: "We have to take the leap of faith now."
Fellow guest speaker Maud Hardy explained how eco-modulated fees would play a major role in the 2023 to 2028 roadmap set out for France's ReFashion extended producer responsibility organization for textiles, of which she is managing director. Bonuses and penalties would be applied concerning durability, environmental certification, and incorporation of recycled materials.
The French government had also set the "huge" objectives of raising the collection rate in France from around 30 percent to 60 percent by 2028 and 80 percent recycling of non-reusable post-consumer textiles and footwear in 2027. Achieving these and other goals set out in the roadmap would require brands to invest Euro 1.2 billion (around U.S. $ 1.3 billion), Ms Hardy said.
During a panel discussion moderated by Alan Wheeler of the UK's Textile Recycling Association, reference was made to Renewcell which established an industrial-scale textile-to-textile recycling facility in Sweden but had since filed for bankruptcy. Robert van de Kerkhoff, founder and CEO of PEPPER-i2/Impact & Inspire in Switzerland, told delegates: "We know it's going to be a bumpy road. Yes, failures will happen. We need to step back and learn from them."
Asked about the necessary ingredients for achieving circularity success, Mr Van de Kerkhoff identified the need both for full transparency and for ensuring a level playing field given that the EU had taken the legislative lead in, for example, calling for compulsory separate collections of textiles by 2025. He also quoted an Euratex figure that up to 250 industrial projects would be required across Europe covering different types of fibre-to-fibre recycling.
According to BIR Textiles Division President Martin Böschen of TEXAID Textilverwertungs AG in Switzerland, current conditions for recyclers were "not so favourable" owing to low demand and falling prices. The short-term outlook remained "bumpy," not least because of concerns over synchronizing the various components of a more circular industry. However, he added, the longer term offered the prospect of good progress on textiles circularity.