Goudsmit Magnetics' three-stage metal separator for plastics recycling
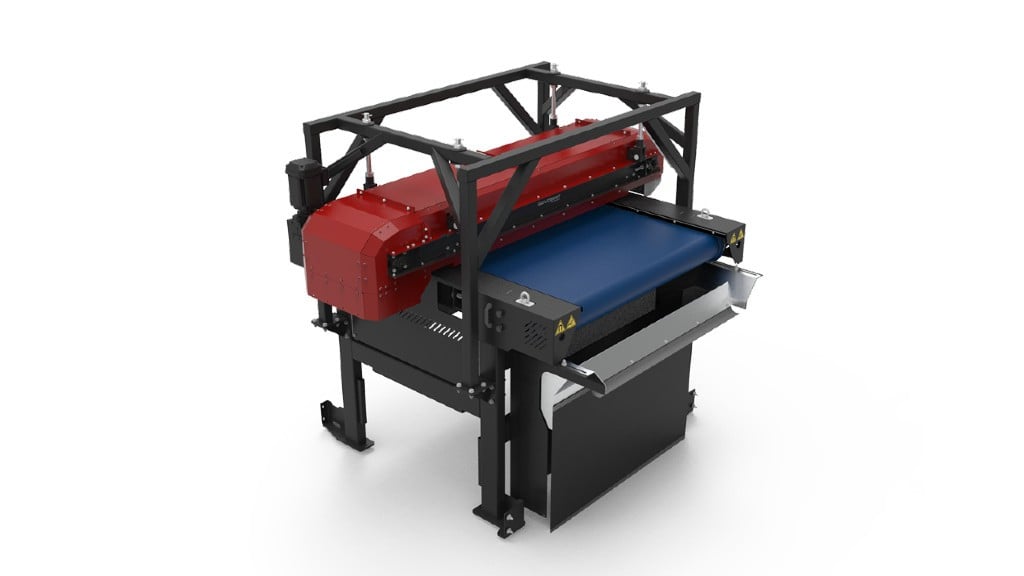
At IFAT 2024 in Munich, Goudsmit Magnetics will introduce a three-stage metal separator for plastic recycling, along with other solutions. The system consists of an eddy current separator equipped with an overband magnet and a high-gradient head roller magnet. In one run, the three-stage metal separator removes steel, iron and stainless steel fines, and non-ferrous metals such as copper, aluminum, brass, precious metals, and lead. Even metal-contaminated particles are separated from the product stream. This creates a cleaner final fraction for plastics processors. Lower contamination levels in the granules or flakes reduce costs in the downstream process; filters of melting screws and plastics chemical processing plants stay clean and do not jam.
Adaptable modular system for plastics
This three-in-one metal separator is designed for fine materials from 0 to 15 to 20 millimetres. It is particularly applied in plastics processing, but WEEE and ASR are also important applications where this magnetic technology can extract more valuable metals from the product stream. In this case, recovery is the goal instead of removal of metal contamination. The magnet producer opted for a combination with an overband magnet instead of a magnetic drum separator because the first separation step gives a cleaner final fraction, which is more marketable. If required, this modular system is also available without an overband magnet.
Three-stage separation
The material is fed wide and in a thin layer via a vibratory feeder. This monolayer facilitates further processing of the product flow. Then the overband magnet takes effect. This separates coarser steel particles from the material. The high-gradient head pulley separator removes fine iron particles plus stainless steel, including trapped steel and stainless steel particles, after which the 38 HI eddy current separator separates the nonferrous metal parts, even if they are attached to rubber or plastic. The thinner layer thickness and the pre-separation by the overband magnet allow the separators to do their job better. The combination of these three different separation techniques allow recyclers to create more value by being left with a cleaner end product, which is more efficient to process and therefore more profitable. This results in more intensive metal separation and therefore greater recovery of valuable metals.