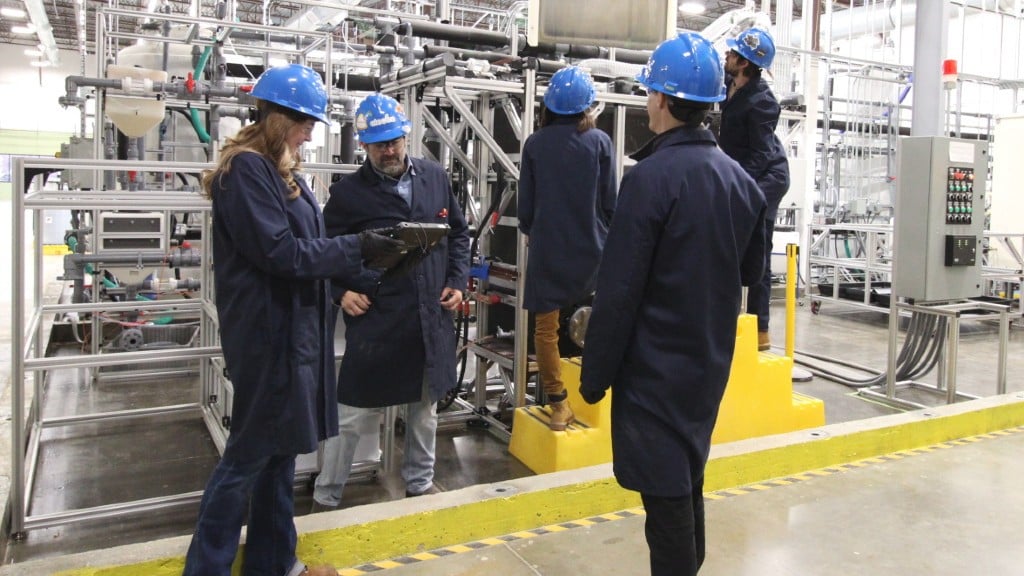
Electra has commissioned its pilot plant in Boulder, Colorado. The pilot demonstrates Electra's technology to produce metallic iron from already mined, high-impurity, commercially stranded ores to help accelerate decarbonization, sustainability, and circularity efforts across the ore-to-steel value chain.
With 90 percent of steel production's CO2 emissions coming from ironmaking, Electra's process takes on this challenge by operating at 140 degrees Fahrenheit, enabling the integration of intermittent renewable energy resources, making emissions-free iron possible at temperatures colder than coffee. The process intakes a wide range of ores and the principal iron ore impurities like alumina and silica are selectively refined as co-products. With what Electra says is greater than 99 percent purity, Electra's clean iron, combined with recycled scrap steel, offers high value-in-use for electric arc furnace (EAF) steelmakers, while also reducing the capital intensity, cost, and waste across the value chain.
The pilot is designed to produce clean iron in approximately one-metre square plates. Electra is looking to increase capacity in a phased approach to validate modularity. By repeatedly connecting the iron plates already demonstrated at the pilot scale, Electra says that the plant capacity is increased to millions of tonnes of iron production at the commercial scale. BHP supplied the iron ores for this pilot.
"Clean iron produced from a wide variety of ore types is the key constraint to decarbonizing the steel industry sustainably," said Electra CEO and Co-Founder Sandeep Nijhawan. "With support from our partners across the value chain, the pilot brings us closer to our goal of producing millions of tonnes of clean iron by the end of the decade."
Company info
Bay Adelaide Centre
333 Bay Street, Suite 2400, P.O. Box 20
Toronto, ON
CA, M5H 2T6
Website:
electrabmc.com