How the Inflation Reduction Act provides a competitive edge for U.S. steelmakers
The IRA has helped steelmakers ramp up their investments for sustainable steelmaking capacities
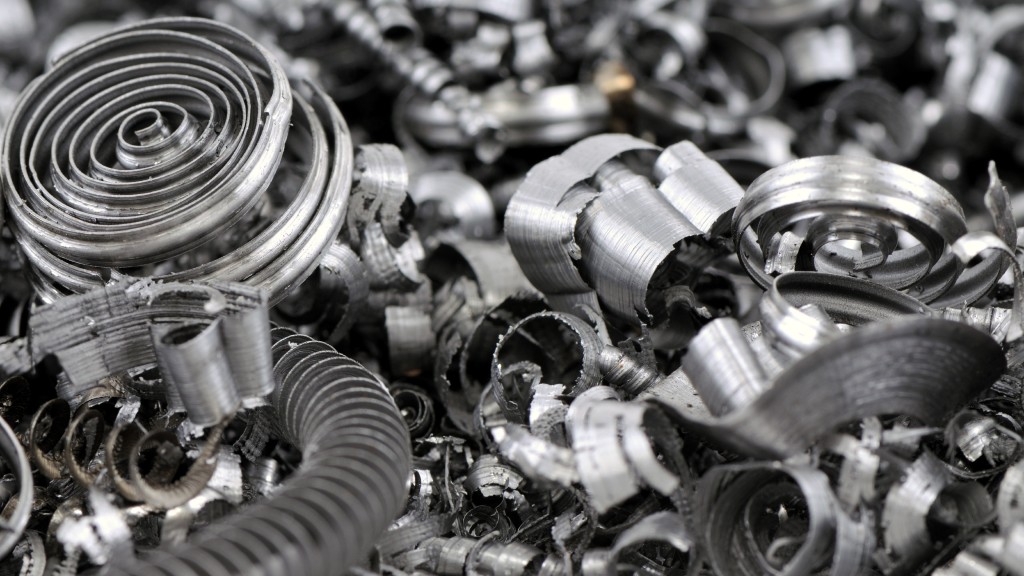
The Inflation Reduction Act (IRA), like the Infrastructure Investment and Jobs Act (IIJA) and the CHIPS and Science Act, has helped steelmakers ramp up their investments for sustainable steelmaking capacities, says Philip K. Bell, president of the Steel Manufacturers Association (SMA).
The impact of the IRA – which allocates $370 billion in tax incentives to promote clean energy – is being felt within a year of the Biden administration enacting it as U.S. infrastructure transitions to higher consumption of green steel.
In fact, according to a Goldman Sachs Asset Management, 280 clean energy projects have been announced across 44 U.S. states in the IRA's first year with an investment of $282 billion.
Moreover, the American Iron and Steel Institute estimates a requirement of 50,000 net tonnes (45,359 metric tonnes) of steel for every $1 billion in infrastructure spending.
Steelmaker Nucor approved funding in February for a new rebar micro mill in the Pacific Northwest. The plant that will be built with an investment of $860 million will produce around 650,000 metric tonnes of rebar annually, and will be Nucor's largest rebar micro mill with 50 percent more capacity than its North Carolina mill that is currently under construction.
In January, the company broke ground on its $3.1 billion steel sheet mill in Apple Grove, West Virginia. The mill is expected to produce around 3 million net tonnes of recycled steel sheet per year once it commences operations in the first quarter of 2026.
The company is betting on the continued strength of the rebar market given the increase in U.S. infrastructure investments due to legislation like the IRA as the product is used in the construction of roads, buildings, and other types of infrastructure.
"For steelmakers using recycled steel in production, who represent over 70 percent of American steel capacity, the significant investment in green manufacturing represents an endorsement of their decades-long investment in low-emissions steelmaking. To build renewable energy infrastructure and promote a circular economy approach to manufacturing, it makes sense to use the cleanest steel available anywhere," says Bell.
Why is decarbonizing steel important?
In November 2023, Nucor announced net-zero science-based greenhouse gas (GHG) targets for 2050 and established a new interim target for 2030. These include scopes 1, 2, and 3 emissions from the production of hot rolled steel as defined by the Global Steel Climate Council (GSCC). These new targets are more ambitious than Nucor's 2021 goal of a 35 percent reduction in steel mill scope 1 and scope 2 GHG intensity by 2030, using 2015 as a baseline.
The steelmaker already uses around 80 percent recycled steel in its production process, with its GHG emissions at one-third intensity compared to the average traditional extractive steelmaking process using a blast furnace.
Nucor will achieve its goals by increasing clean electricity usage, carbon capture and sequestration, and near-zero GHG ironmaking. It will also utilize technologies to reduce the consumption of injection and charge carbon while lowering the use of natural gas in its production processes.
Like Nucor, U.S. Steel also has a net-zero road map for 2050. To achieve these goals, the steelmaker will further incorporate and utilize electric arc furnace-based (EAFs) mini-mill steelmaking technology. The company's Big River 2 mini mill will be commissioned in the second half of 2024 after its board approved a further capital investment to take the total to $3.2 billion. The mill, which will be based in Osceola, Arkansas, will produce 3 million metric tonnes of steel annually.
Based on the number of mini mills deployed, the decrease in emissions could be 10 to 60 percent against the 2018 target. It also plans to adopt direct reduced iron/hot briquetted iron (DRI/HBI) technology with natural gas as the reductant for converting iron ore to fuel the growing numbers of EAFs. Eventually, the steelmaker seeks to use hydrogen to substitute natural gas in the production of DRI/HBI.
Meanwhile, Cleveland-Cliffs has invested in electrical steel capacities previously unavailable in the U.S. It is also investing in Ohio and Indiana to make hydrogen viable for steelmaking. Cliffs' Toledo, Ohio, facility - which opened in late 2020 - was designed hydrogen-ready. The company performed trials using hydrogen in early May 2023 at the blast furnace in Middletown for half a day with success, paving the way for commercial-level production using this input.
Cliffs also completed a blast furnace hydrogen injection trial at its Indiana Harbor blast furnace in January after commissioning the hydrogen pipeline at Indiana Harbor. This pipeline fed the input to the blast furnace during the trial.
Irving-based Commercial Metals Company (CMC) commissioned its second Danieli Mida micro mill in Arizona in June 2023 with a 500,000 metric tonnes per year production capacity. Barbara R Smith, then the chairman and chief executive officer of CMC, noted that the mill is starting operations at the right time, considering opportunities from the Infrastructure Investment and Jobs Act, the IRA, and the reshoring of demand from the construction sector.
The company is also constructing its fourth micro mill in West Virginia, which will produce 500,000 net tonnes of steel products annually. This will include 350,000 net tonnes of rebar and 150,000 net tonnes of small merchant items. CMC is investing around $450 million after tax breaks for this mill, which will supply steel to key markets like the Mid-Atlantic and Northeast, along with the Midwest.
Domestic preferences provide a competitive edge
One of the ways the IRA is giving a boost to manufacturing in the country is by including strong domestic procurement preferences that prioritize using the lowest emission goods for projects that are eligible for incentives under the law, according to Bell.
"For American steelmakers, that represents a pledge to favour domestically produced steel over imported steel, which often is made in non-market economies using high-emissions processes," says Bell.
Bell also states that the law is helping to modernize, decarbonize, and electrify the American steel industry. "The IRA money supports investment in virtually every link of the steel supply chain, including direct-reduced iron, hydrogen hubs, carbon capture, and nuclear energy to power steel plants. These types of projects make American steel not only more competitive, but also cleaner," says Bell.
Combined with the domestic procurement preferences of the law, those investments in sustainable steelmaking processes put American steel in a stronger position relative to imported steel while also reducing carbon emissions.
A report by management consulting firm Boston Consulting Group (BCG) states that IRA subsidies will give the U.S. an advantage in green steel exports, putting other potential exporters at a disadvantage. The cost of green steel production from green-powered EAF with 90 percent recycled steel and 10 percent merchant DRI would be $385 per metric tonne in the U.S. by 2030 versus $390 per metric tonne in Germany. Hydrogen DRI + green-powered EAF with 80 percent hot metal and 20 percent recycled steel would cost $560 per metric tonne in the U.S. with the help of tax credits compared to $640 per metric tonne in Germany.
The German Steel Association Wirtschaftsvereinigung Stahl (WV Stahl) has noted that international competitive conditions arising from the IRA would be challenging for Europe as an industrial location. It adds that these will be intensified by the protectionist orientation of the IRA in parts.
Against this backdrop, WV Stahl calls for competitive energy prices, as that has already affected the competitiveness of the German industry in the global market. It has also urged for the acceleration of hydrogen-based steelmaking, which if delayed, could shift investment projects from the EU to the U.S.
A push for green steel
Besides providing a competitive edge in the global market, Bell highlights the Act's role in driving new demand.
"First, it creates incentives for renewable energy and the electrification of the economy. That means additional demand for steel for wind turbines, electric grid components, hydrogen storage and transport, solar equipment, and other energy infrastructure. Second, it is fuelling a boom in conventional construction, including manufacturing facilities, data centres, and the roads and infrastructure that make our economy more competitive," says Bell.
Mayuri Phadnis is Editor (Europe) at Davis Index and can be reached at Mayuri.phadnis@davisindex.com.