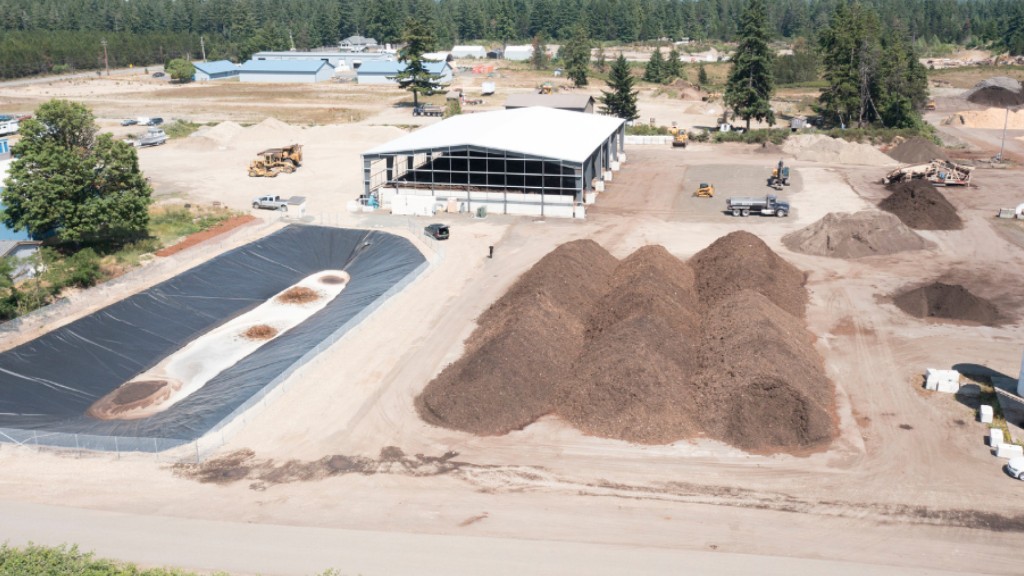
Brady Trucking Co. is operating a new food waste composting system at their existing mulch production facility in Shelton, Washington. The composting facility uses a "covered aerated static pile" process, or cASP, with technology and facility design services from Green Mountain Technologies of Bainbridge Island.
"Once we looked closely at the numbers and conceptual operating plans, we realized this was just the natural next step for our business," said Evan Brady, co-owner of Brady Trucking. "For years we've been purchasing compost in bulk to have availability for our mulch clients who also need compost. Now we're able to efficiently make our own compost while keeping food waste out of landfills."
Brady Trucking has run a successful mulch production facility and trucking company for decades. The company saw an opportunity to meet the growing need for diverting food waste from landfills driven in part by Washington law SB1799.
The new cASP composting facility is designed and permitted to process 50,000 tons per year, with a current constructed peak capacity of 30,000 tons per year. Up to 10 percent of the annual volume is food waste. Food waste currently comes from 3rd party collection services in Thurston County, Washington.
"To design, permit and build a large food waste composting facility in one of the wettest regions of the US, all in less than one year, was a pretty impressive achievement," said Ashley Brady, co-owner of Brady Trucking. "We are grateful for the team at Green Mountain Technologies, they've done a great job on the overall facility design, including stormwater management and ongoing operating support."
The aerated compost processing system is built under a covered roof structure. Compost feedstock materials are blended and formed into piles over the aeration outlets built into the concrete floor, and then the material is capped with a "bio layer" of wood mulch to contain odours.
The WebMacs aeration system from Green Mountain Technologies is computer-controlled to optimize temperatures across multiple zones to help accelerate the composting process while keeping pile temperatures at ideal levels. This reduces the need for mechanical turning of the material, speeds up the process, and ensures low operating costs for the facility, while mostly eliminating odours and anaerobic gas emissions such as nitrous oxide and methane.
"We have really enjoyed working with Evan, Ashley, and the team at Brady Trucking," said Jeff Gage, director of consulting for Green Mountain Technologies. "They saw this opportunity and took a very pragmatic approach to get it operational on an ambitious timeline, with our help. We see this facility as a model for other mulch grinding operations to follow."