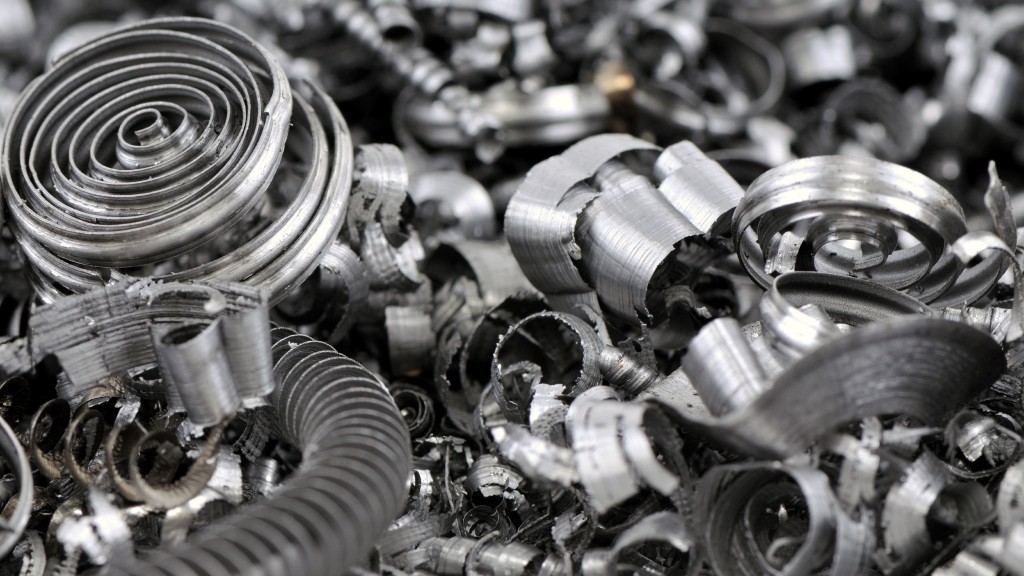
The REMADE Institute has licenced a new technology that utilizes an aluminum recycling innovation developed with REMADE's support. The license involves a technological innovation capable of removing metallic impurities from recycled aluminum melts, improving the quality of the aluminum and allowing it to be used for more diverse applications like electric vehicle (EV) manufacturing.
The innovation is part of a research and development project funded by REMADE in 2020. The R&D project, "Selective Recovery of Elements from Molten Aluminum Alloys," is still in progress and is led by Subodh Das, Ph.D., CEO of Phinix, LLC. REMADE's tech team oversees the project, ensuring it meets the Institute's and DOE's technological milestones.
"Congratulations to the entire project team, including Phinix's Dr. Das and our tech team at the Institute," said REMADE CEO Nabil Nasr. "A new technology license is a tremendous accomplishment. We believe this technology will be incredibly valuable to U.S.-based aluminum companies, including those that supply the automotive industry. Ultimately, it's yet another key technology that accelerates the U.S.'s transition to a Circular Economy and assists the nation in meeting its net zero by 2050 goal."
Details of the technological innovation are the subject of a pending patent. Proprietary process advantages include the removal of impurities and the increased availability and quality of recycled aluminum. These innovations allow aluminum to be used for a wider variety of manufacturing applications. The IP has been licensed by Phinix to a domestic recycled (secondary) aluminum producer.
According to the R&D project team, producing recycled aluminum costs less and saves more than 90 percent of the energy required to produce primary aluminum. Aluminum is one of the world's most recycled materials, but there is room to enhance its recycling rate, cost, recyclability, and sustainability. The U.S. Geological Survey estimates that the U.S. consumption of aluminum in 2022 was 5.100 million metric tons (MMT). Of this, about 2.740 MMT was imported, 0.860 MMT was produced from primary ores, and the balance of 1.5 MMT was produced from scrap.
Das, the R&D project's principal investigator, said the research project ultimately seeks to develop technologies to improve the quality and increase the usage of recycled aluminum in U.S. manufacturing.
"This technology is capable of benefiting aluminum companies significantly," he said. "It's capable of lowering their energy costs, increasing their profits, and increasing the overall value of recycled aluminum considerably."
REMADE Chief Technology Officer Magdi Azer said the tech license is another milestone for the public-private partnership, which seeks to increase the reuse, remanufacturing, recycling, and recovery of four energy-intensive materials: metals, including steel and aluminum; polymers, including plastics; fibres, including papers and textiles; and electronic scrap.
"REMADE is selective in funding R&D projects that have the greatest potential to reduce energy consumption, decrease greenhouse gas emissions, decrease the use of raw or primary materials, and increase the use of recycled or secondary materials," Azer said. "This particular R&D project is capable of developing technology to increase the quality and usage of recycled aluminum, and as a result, increase the resiliency of the U.S. supply chain and decrease the nation's reliance on imported virgin aluminum from other countries."
Company info
150 Lucius Gordon Drive, Suite #204
West Henrietta, NY
US, 14586
Website:
remadeinstitute.org