Q&A: Sorting and separation equipment’s role in boosting the circular economy and fighting the labour shortage
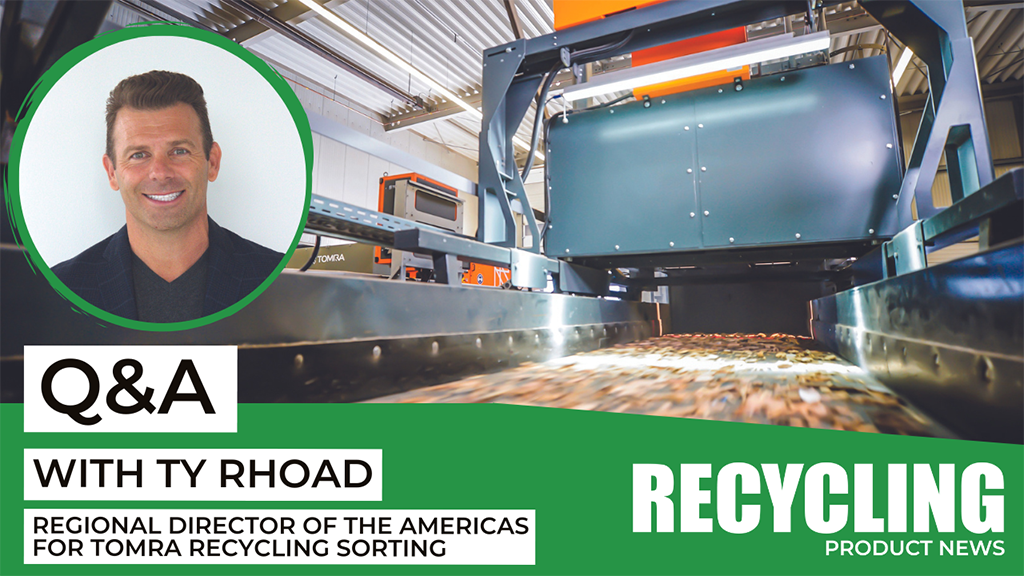
With labour shortages negatively impacting almost all sectors of the recycling industry, recyclers are relying more and more on automation to fill this gap. Machines such as optical sorters are increasingly being used in lieu of manual sorting so that human workers can be utilized elsewhere for maximum efficiency.
I caught up with Ty Rhoad, regional director of the Americas for TOMRA Recycling Sorting, to discuss the role that sorting equipment plays in addressing the labour shortage, as well as other pain points such as material contamination and film waste.
Slone Fox: What are some of the most prominent challenges facing the recycling industry currently, and how does TOMRA equipment address these issues?
Ty Rhoad: Labour continues to be the top challenge facing the industry, and there is no end in sight. Increasing circuit automation through the incorporation of optical sorters – both on the front end and back end of the circuit – can help to ease these labour shortages. Automation can also help to remove workers from the mundane task of hand sorting so that they can be reassigned to a safer, better position for their skill sets.
Cleaner material is also a major pain point for many recyclers in two ways. The need for recycled material continues to rise, and to meet these targets recyclers often must source recyclable materials containing a higher amount of contaminants. Secondly, recyclers must produce higher quality recycled materials meeting high purity standards. The advancements made in sensor technology and software developed to analyze materials with optical sorters, specifically with TOMRA's AUTOSORT, can be the answer to a better sortation.
Finally, film is a growing concern in the industry. Working closely with plant designers and optical sorter suppliers to analyze the incoming feed can help to ease the pain of moving film through the facility.
SF: Are there any emerging or innovative developments in sorting and separation that could potentially disrupt traditional methods in the recycling industry?
TR: I would be remiss in not mentioning artificial intelligence, or AI, here. AI is not only having a tremendous impact on our industry today and is the hot topic of the moment, but it affects just about everything we see and touch in our everyday lives. If you've ever used Google to search for an item, you've used AI.
However, TOMRA has leveraged AI for decades in our optical sorters to help increase sorting accuracy and material purity. But the most recent developments with AI's Deep Learning massive dataset is what is opening the doors to more advanced sorting accuracy and removing contaminants from the most complex material feed. Regardless of whether the optical sorter is using a valve block to eject material or an arm for the final QA material check, these machines are leveraging the capabilities provided by the Deep Learning datasets of AI.
For instance, we recently combined our AUTOSORT technology with our deep-learning-based sorting add-on, GAIN, to create a solution that distinguishes between and sorts different types of wood. A primary application for this technology is sorting non-processed wood (Wood A) from processed wood products like MDF, HDF and OSB, and chipboard. TOMRA was the first company in the world to employ deep learning AI to detect and separate different wood types, and we'll launch more applications in the future.
SF: In your opinion, what are the biggest challenges and opportunities facing the waste management industry in the coming years?
TR: Working for a global company that provides some of the best sorting technologies for the industry, partnering with the best plant builders in North America, and working with passionate customers driven to advance the circular economy - this question gives me both my greatest frustration and my biggest motivating factor each day. It's the unrealized potential due to the lack of a full commitment to recycling and advancing the circular economy.
I think most agree that recycling is a must for our future as well as the following generations. However, a full commitment to the circularity of the industry, in my opinion, just isn't there. It starts at the producer level in offering packaging that is more recyclable, carries through to the consumer who has a responsibility to recycle rather than throw it away, and includes the infrastructure of collection and recycling. This is one reason why we see plastics recycling rates below 10 percent. I believe a bigger commitment must be made to be truly successful.
We have seen that legislation can be a great accelerator to advancing a more circular economy. For instance, we see California being one of the frontrunners in the U.S. when it comes to recycling legislation. We recently worked with VAN DYK and Santa Barbara County to install a system at the Resource Center designed to meet the state's stringent organics recycling diversion targets set for 2025. Plus, it recovers valuable recyclable commodities from municipal solid waste that would have been landfilled just a couple of years ago.
SF: How can sorting and separation equipment be leveraged to promote a more circular economy?
TR: I think it comes down to getting the most out of the recycled material. What I mean is you want the cleanest, most effective feedstock to be recycled. To achieve this, sorting and separation must occur, and TOMRA technology has a proven, decades-long track record of success. And our equipment is designed compact, so it can be fitted into an existing circuit just as easily as it can be designed into an overall solution for a new circuit installation.
I just mentioned plastics, and the plastics industry demands the highest purity requirements. Only the purest fractions can be used for the extrusion process. Today's optical technology can help advance sorting recycled materials to be extrusion-ready flakes. Additionally, optical sorters can help recyclers take advantage of market opportunities.
As an example, we're working with Greenpath Enterprises in California to pioneer a mechanical sorting solution for mixed polyolefins. We're inserting our INNOSORT FLAKE technology into the existing line to identify and separate mixed polyolefin caps from carbonated and non-carbonated beverage bottles. Polypropylene and polyethylene together are the most abundant plastic family, but the market is limited for valuable applications for mixed polyolefins. By using the flake sorters to sort by both polymer type and colour, Greenpath's vision is to create the same type of mature recycling system for bottle closures that exists today for bottle recycling.
SF: What role does consumer behaviour and public awareness play in maximizing the effectiveness of sorting and separation equipment and reducing contamination? In your opinion, what still needs to be done?
TR: The consumer plays a significant role in developing an effective recycling program and reducing contamination of post-consumer materials. It basically starts with the consumer, and consumer behaviour starts at the collection point or disposal point, depending on how you look at it.
The most critical step to take is educating the consumer as to what can and cannot be recycled. "What can I recycle?" is still the biggest question I hear from people. Plus, it varies from location to location as to what materials are accepted for recycling. Therefore, education is the most important first step. Equally as important is the development of a collection infrastructure that makes it easier for the consumer to recycle. Right now, we still have a long way to go in making it easy for most people to return recyclable materials. I believe with improved education and the expansion of collection points for materials, recycling can grow tremendously.
SF: What new developments can we expect to see from TOMRA in the coming years?
TR: From improving sensors, to improving our software, to expanding into different market segments, TOMRA continues to innovate our technologies. We are continuing to leverage the deep learning subset of AI to expand applications for our GAIN technology. We began by purifying post-consumer polyethylene (PE) by removing PE-silicone cartridges and non-PE objects, and then we expanded GAIN for sorting wood chips. In the near term, look for TOMRA's future expansion of GAIN technology to advance sorting purity across different applications.
In June, we made significant strides in aluminum sorting with the introduction of our AUTOSORT PULSE with dynamic LIBS technology, or laser-induced breakdown spectroscopy. It's designed for the high-throughput sorting of aluminum alloys. By being able to sort between 5xxx and 6xxx series aluminum alloys, we're recovering pure mono-material fractions from mixed scrap to advance further processing into virgin-like material with high recycled content.
Also, look for digitization to play a more important role in helping plant operators increase profitability. Our cloud-based data platform, TOMRA Insight, allows facilities to use data to optimize the sorting process using near-live monitoring. The critical sorting data provided by Insight allows managers to anticipate operational issues, see future maintenance requirements, and be more in control of the entire sorting line.