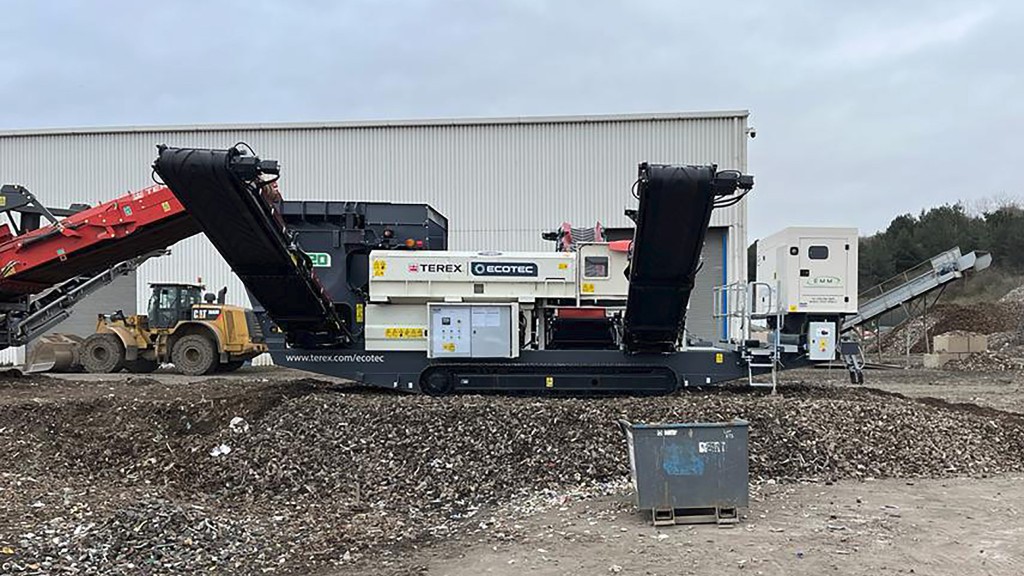
Celsa Recycling, a European producer of circular and low-emission steel, wanted to find a new way to gain value by extracting ferrous and non-ferrous metals from a variety of waste streams going through its U.K. facility. With the help of Environmental Material Management LTD (EMM), a consultant for waste material and material processing services, the recycler settled on a Terex Ecotec TMS 320 metal separator.
In order for Celsa Recycling to utilize the TMS 320 in the application they wanted, some changes had to be made first.
"Having worked with every brand of standard eddy current rotors on the market we choose to work with Terex Ecotec because out of all the equipment we tested on-site, it was the one worth tailoring to be more suitable for metal recovery," says David Constable, managing director of Environmental Material Management.
The machine wasn't suited for the harsh metals at Celsa's facility, says Thomas Coulter, regional sales manager at Terex Ecotec. Instead, it was developed for biomass and wood applications.
EMM worked intensely with Terex Ecotec and Molson Green, a distribution partner for Terex Ecotec in the U.K., to develop a machine that is suitable for the heavy demands of a solely metal processing waste stream.
The TMS 320 was configured with an eight-pole eddy current rotor to provide a deeper magnetic field. This magnetic field interacts with the full body of the larger particles that are more common in the metals recovery industry. This also enabled a heavier-duty belt to be fitted that would withstand the large volume of sharp metal passing over the unit, resulting in increased belt life and reduced downtime for repair. Other modifications included increasing the stockpile heights of the conveyors to handle greater material split towards the recovered metals when compared to biomass and wood applications. Finally, noise reduction technology was added to the TMS 320 to reduce the noise created by the increased quantity of processed metals passing through the machine.
The TMS 320 metal separator is now at Celsa Recycling. The material is initially processed by two Finlay screeners to separate the material stream by size. Material over 100mm is then processed by Celsa's static plant. Anything below 100mm is processed by the TMS 320 to extract ferrous and non-ferrous metals. The machine is processing over 10 tonnes of non-ferrous metals per day to the value of £9,000 per day – material that previously would have been going to landfill. The remaining organic material is being used as recycled fill.
"The demands of our customers are constantly evolving and meeting their needs with a sustainable approach that supports them in extracting as much value from waste is a core value of Terex Ecotec," says Coulter. "Having the Terex Ecotec TMS 320 metal separator . . . is a huge testament to the ability of our machines to support the circular economy and reduce the carbon footprint of operations."
Company info
22 Whittier Street
Newton, NH
US, 03858
Website:
terex.com/ecotec
Phone number:
603-382-0556