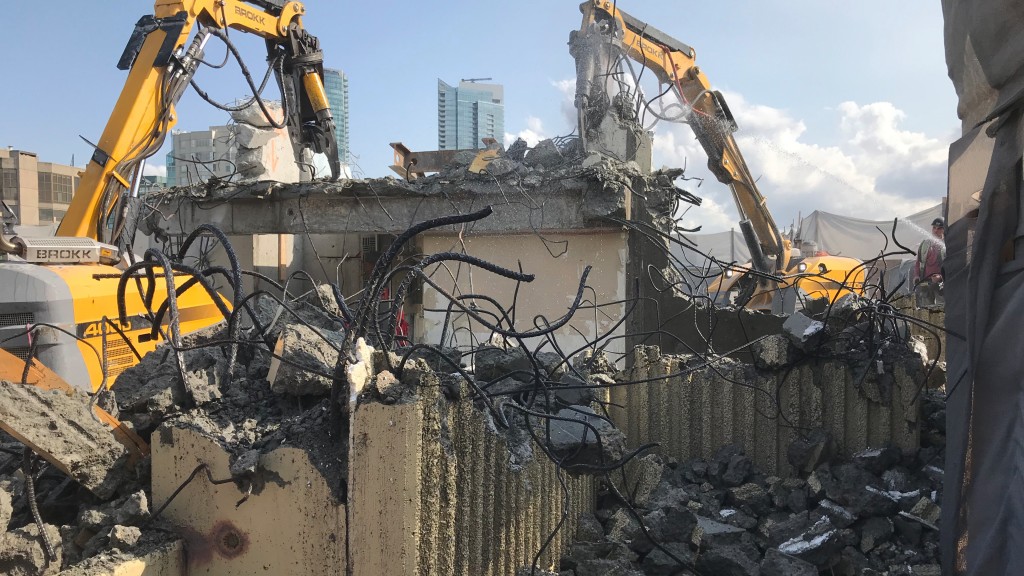
For interior and top-down demolition, many contractors have come to rely on remote-controlled demolition robots – for good reason. These machines provide ideal power-to-weight ratios. The smallest models easily fit through standard doorways and are light enough to transport using a passenger elevator, making them ideal for demolition in tight spaces. Despite this compact footprint, they can provide hitting power on par with excavators three times their size.
This power comes from a pairing between carrier and breaker – standard equipment for these machines. For ideal performance, manufacturers design their demolition robots starting from the tip of the breaker to ensure that hydraulic flow and pressure are perfectly calibrated. This increases efficiency and breaking capacity but also results in less wear and tear on the carrier for a hardier unit overall.
However, solely relying on a breaker is selling these machines short. A range of attachments are available from manufacturers, allowing operators to tackle a variety of tasks, such as material handling, excavation, surface preparation, and much more. Forward-thinking contractors are capitalizing on the versatility provided by the right suite of attachments. The proper combinations can streamline their job sites as well as open up new applications to grow their business – turning a demolition robot into a remote-controlled tool carrier.
Selecting the right attachments is key to unlocking the full potential of these machines. Here are four attachments to consider for optimum efficiency with remote-controlled demolition equipment.
Concrete crushers
Next to hydraulic breakers, crushers are probably the most common attachment for demolition contractors. These attachments reduce noise and vibrations, so they can be used in a number of sensitive environments.
Where breakers use force to knock down a wall, crushers simply chew up the concrete, leaving rebar exposed. To do this, crushers require access to an exposed edge of the structure being demolished – either the top, side, or end – in order to break it down. Imagine trying to take a bite from the middle of a piece of bread. It doesn't work without bending the bread. Taking a bite from any side, on the other hand, doesn't require any special maneuvering. For top-down applications where noise and vibration constraints are primary concerns, crushers allow contractors to work during the day – in some cases without the neighbours even noticing.
Recently, a Canadian contractor was able to remove 38 stories using crushers and remote-controlled demolition robots. The company's primary focus was mitigating disruption to the local area with the dust and noise that accompanies any demolition project. After erecting a hoarding system around the top of the building, the demolition area was essentially hidden from the ground and neighbouring buildings. The contractor worked down through the building's floors, systematically crushing concrete and cutting reinforcement steel. Working with two demolition robots, crews were able to complete one floor every three to four days, taking down the entire 38 stories in just 9 months. Curious residents, unable to see or hear what was going on, questioned if the project was actually progressing until the protective hoarding structures were removed and the top of the landmark structure had disappeared.
In addition to "silent demolition" crushers also make material handling easier. The resulting debris is a uniform size, and steel is separated for recycling during the initial demolition instead of having to remove it later.
For maximum efficiency, pay attention to the jaw opening and crushing force. To easily take on concrete slabs 17 to 22 inches (440 to 560 millimetres) thick, a crushing force of 44 to 54 tons is best. Wear-resistant, replaceable steel alloy crusher tips and cutter blades, as well as a full 360-degree rotation, are also recommended.
Metal and combi shears
Shears are another attachment that, when paired with demolition robots, can significantly increase safety and productivity on a demolition job site. As with breakers, crushers, and grapples, manufacturers have taken advantage of the maneuverability and precision available from demolition robots to optimize their shear attachments, reducing the need for larger crews and handheld torches in a number of applications.
Because of floor load limits or other access restrictions for larger equipment, contractors have traditionally relied on handheld torches for metal-cutting tasks on interior demolition projects. The use of hand tools for cutting concrete reinforcement, sprinklers, conduits, wires, and cables come with potentially life-threatening risks for workers. In addition to electrical shocks, burns, fumes, fire hazards, and falling debris, these tasks often require scaffolding. The potential hazards add up to increased health concerns for workers, which is reflected in worker's comp claims and higher insurance premiums for employers.
Using a remote-controlled tool carrier with a shear attachment for these tasks eliminates many of the associated risks. Shears pierce or cut through material, rather than burn through it like a torch. By removing heat from the equation, operators are also eliminating sparks, flying embers, and fumes. Additionally, compact demolition robots are able to access confined spaces and areas with low floor loads. Using shears in these situations offers a mechanical solution that keeps operators safely on the ground while providing a good view of the work. And, while contractors should still ensure electricity is shut off before cutting wires or other conduit, it's much better for a robot to take an electrical shock than a human.
Look for shears with a high power-to-weight ratio. This allows for ideal cutting power in a smaller package, making it easier to maneuver the shears in tight spaces. Additionally, a hydraulic 360-degree rotary drive provides pin-point accuracy.
Multi-purpose grapples
Perhaps the most underutilized demolition attachment is the grapple. This tool is ideal for soft demolition, separation, and sorting applications. It can also be used for support tasks before, during, and after the primary demolition.
Grapples function like a rudimentary hand with two fingers and a thumb for pinching, pulling, and sorting. When paired with a flexible remote-controlled machine, the grapple can provide significant time and cost savings over manual demolition methods in tight, confined spaces. In many cases, it removes the need for harnessed workers on ladders or scaffolding. For example, the highly articulated attachment can be used to grasp structural elements such as drywall, ceiling sections, piping, steel drums, and HVAC ducts which the remote-controlled carrier machine can then easily pull down. Remote operation also means workers can position themselves away from any falling debris while maintaining a good view of the work.
Another example would be elements that require support, like a four-inch-diameter overhead pipe that needs to be cut with a torch. The grapple clamps onto the pipe and holds it while a worker torches through it on either end. Once it is free, the grapple safely lowers the pipe to the ground.
And grapples aren't just for demolition. Grapple attachments can also be used for lifting, moving, and support during construction. Depending on the jaw opening and carrier size, these tools can lift materials up to 30 inches in diameter. When paired with a demolition robot with exceptional reach, this means operators can remain safely on the ground and out of the drop zone for a number of overhead tasks.
Additionally, once materials have been pulled down, the precision and flexibility of the remote-controlled demolition machine with the grapple attachment make it easy to pick up and sort even small debris.
Jaw opening is important for overall productivity. A 360-degree hydraulic rotation circuit should also be considered for fast and accurate positioning. For picking, sorting, and material handling, boltable grip plates allow operators to complete those tasks without switching attachments.
Buckets
No suite of robotic demolition attachments would be complete without a bucket – or two. These multi-purpose tools increase efficiency for a number of confined applications such as excavation, digging trenches, material handling, sorting, separating, and loading debris.
Since they are primarily designed to optimize breakout forces for hammering above and in front of the machine, the demolition robots' boom design provides ample power for digging in rocky soil and heavy clay. It also provides increased reach and maneuverability compared to most similar-sized mini excavators. A three-part arm allows demolition robots from leading manufacturers to work closer to the carrier body, minimizing the need to reposition. Compared to the two-part excavator boom, the demolition robot's flexible three-part arm also requires less height to extend, making it ideal for confined spaces. Most models only require 72 to 84 inches (182.9 to 213.4 centimetres) of height clearance for excavation, allowing operators to work in a number of situations with low overhead clearance, such as tunnels and utility applications. Smooth, precise movements and a remarkable range of motion mean operators can dig both toward and away from the machine by simply switching the direction of the bucket, and a stronger boom means the demolition robot can handle larger buckets and heavier loads than similar-sized excavators.
Using a bucket and remote-control demolition robot also provides increased safety compared to an excavator. Remote-control operation keeps employees safely on the ground and outside the immediate work zone, protecting them from dust and flying debris. It also eliminates the need to climb into or out of a cab, which is a leading cause of job site injury often resulting in sprains, strains, and other minor ailments.
Manufacturers offer customized buckets to fit an operation's specific needs for maximum efficiency.
Tackle any task
These tools are just a small representation of what some manufacturers offer – the ideal suite of tools for interior and top-down demolition. With more than 80 attachments to choose from, manufacturers aren't kidding when they say they have a tool for every application. From planers and descalers to rock drills, saws, and shotcrete guns, a demolition robot can become a true multi-purpose machine that opens up new revenue opportunities and speeds up ROI.
Jeff Keeling is the vice president of sales and marketing for Brokk Inc. He works closely with regional sales managers to develop and grow the Brokk brand in key segments across the United States and Canada. He is also responsible for educational initiatives aimed at helping customers maximize their Brokk machines' potential.