TOMRA’s newest machine leverages dynamic LIBS technology for aluminum sorting
The AUTOSORT PULSE can be used across a wide range of applications to create high-quality secondary metals
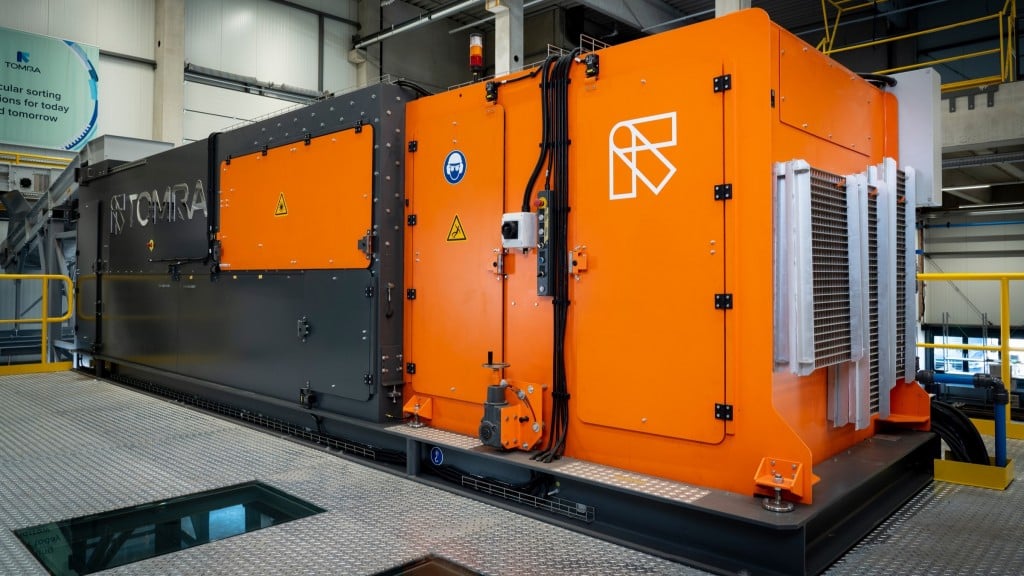
TOMRA Recycling Sorting has introduced a new machine featuring dynamic laser-induced breakdown spectroscopy (LIBS). Designed for high throughput sorting of aluminum alloys, AUTOSORT PULSE can be used across a wide range of applications to create high-quality secondary metals.
As the metals industry strives to increase recycling rates to reduce both energy consumption and the use of raw materials, the use of sorting technology is essential. The recovery of pure mono materials from mixed scrap allows further processing into virgin-like material with high recycled content.
Frank van de Winkel, market strategy segment manager metals at TOMRA Recycling Sorting, explains: "Aluminum scrap consists of multiple alloys. Depending on the application, they contain a mix of different alloying metals that define the material's properties. To recycle a specific alloy without downgrading quality, it must be separated into specific alloy classes - a task that can only be done with the most sophisticated technologies, such as LIBS. Our team of in-house engineers has dedicated significant time and effort in the development of this technology to make it excel in performance. AUTOSORT PULSE gives recyclers the means to sort aluminum by alloy classes and produce furnace-ready products for demanding applications."
AUTOSORT PULSE enables high-throughput production of green aluminum. Featuring the patented, dynamic LIBS technology, it enables the separation of, for example, 5xxx and 6xxx aluminum alloys. The machine's 3D object scanning detects each object regardless of its size and surface, while multiple single-point scans enable sharper detection of materials in any condition. Due to its AI-based object singulation feature, even overlapping and adjacent objects can be accurately separated to maximize yield. Multiple material tests have demonstrated that purity levels of more than 95 percent can be achieved.
High volume processing
With a bulk infeed system and a processing capacity between 3-7 tons/hour, operators can create high volumes of recycled content to meet industry standards across a wide range of applications. Its relatively compact equipment footprint integrates an extensive set of advanced technologies and a conveyor belt, making it easy to install without the need for additional, complicated material handling equipment. The AUTOSORT PULSE design also protects workers from any potentially harmful or penetrating light emissions.
Matthias Winkler, product manager at TOMRA Recycling Sorting, states: "We have a long-standing legacy in the metals segment and our finger is on the pulse of the market. Based on our extensive in-house knowledge, we started developing the dynamic LIBS technology when we sensed alloy separation could help businesses reduce downgrading material. After an extensive innovation phase, we have now extended our product portfolio with AUTOSORT PULSE to complement the new generation X-TRACT. Customers testing the machine are impressed by its results and the operational benefits it offers. They can run high throughput and create high-quality products, which gives them access to new material streams and makes them benefit from operational flexibility and a quick return on investment. I strongly believe that AUTOSORT PULSE will solve the sorting challenges of tomorrow."
Data-driven results
The insights generated from sorting operation data play a critical role in facilitating plant operators' quest to run a profitable business with little to no downtime and maximum output. Available as an additional service for AUTOSORT PULSE, the cloud-based data platform TOMRA Insight allows for a data-driven optimization of sorting processes through near-live monitoring. As critical sorting data is available anywhere and anytime, operators can anticipate operational issues and future maintenance requirements and be in control of the entire sorting line.
Aluminum is a very versatile material that is a highly demanded commodity for the automotive, building and construction, and packaging industries, all of which contribute to an unprecedented demand for aluminum. In Europe alone, demand is expected to grow by 40 percent from 2018-2050 with no signs of a trend reversal. At the same time, the aluminum industry is undertaking considerable decarbonization efforts to reach worldwide climate goals, such as those set in the EU and United States for 2050.
To bridge the gap between supply and demand and support the transition to a climate-neutral society, the industry resorts to recycled aluminum, which offers a two-fold benefit. First, recycling aluminum is 95 percent less energy-intense compared to primary production. Second, it prolongs the lifecycle of already produced materials and gives new value to an abundance of scrap aluminum.
Terence Keyworth, segment manager metals at TOMRA Recycling Sorting, states: "Our intensive and long-term collaboration with some of the world's largest scrap recyclers and aluminum producers is the foundation of our development process. With AUTOSORT PULSE and our new generation X-TRACT, we provide the technological force in driving the aluminum sector's net-zero transition as it delivers high-quality alloy scrap fractions for producing low-carbon aluminum."