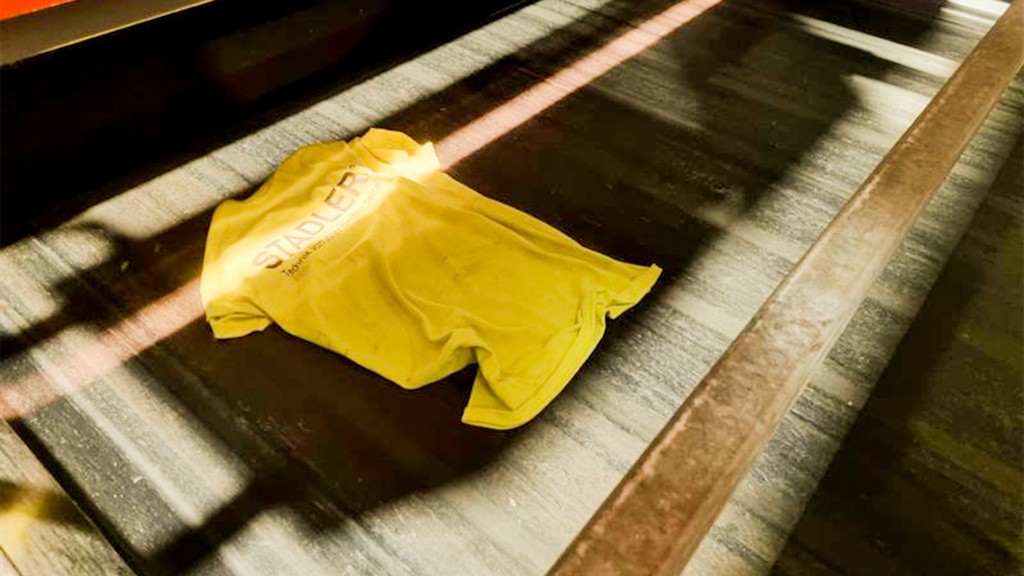
Only a tiny fraction of discarded textiles are recycled. While the clothing industry has doubled production in the last 15 years, the time garments are worn has fallen by more than 30 percent. At the same time, the rising demand for low-cost fast fashion is driving a decline in the quality of the materials, which makes them more difficult to reuse or recycle. According to the Ellen MacArthur Foundation, it is estimated that 114 million tonnes of textile waste are generated every year. Of the clothing that is collected for recycling, 12 percent is downcycled into lower-value applications such as insulation material, and less than one percent is used to make new clothing in a closed-loop circular economy. The high content of polyester in fast fashion also means that an increasing quantity of discarded textiles are incinerated in waste-to-energy plants because of its high calorific value.
The environmental impact of textile waste
The rising consumption of clothing, coupled with the decreasing wearing time and increasing use of synthetic materials such as polyester and nylon, is worsening the negative impact on the environment. Large quantities of plastic microfibres shed through the washing of textiles are leaked into the ocean, accounting for 35 percent of microplastic pollution. Improper disposal can also result in flat textiles being released into the environment, endangering wildlife on land and marine life.
Regulatory drive for the development of textile recycling
Policymakers have a key role to play in driving an increase in recycling. In Europe, in 2022 the commission presented an E.U. Strategy for Sustainable Textiles, which includes extending the lifetime of textiles by recycling the materials they contain into new quality products. The revised Waste Framework Directive requires E.U. member countries to establish systems for separate collection of textile waste by the beginning of 2025, and at the same time, new collection and recycling targets will kick in. The infrastructure for collecting, sorting, and recycling these materials will need to expand fast in readiness for the new regulations.
The textile sorting challenge
Clothing is made of different fabrics, fixtures and accessories, such as buttons or zips, and they contain a variety of raw materials – combinations of natural and synthetic fibres, plastics, and metals. This makes disposing of it sustainably a complicated matter.
"The recycling industry requires pure fractions or very specific mixtures," explains Annika Ludes, engineer for digital solutions at STADLER. "This means removing the fixtures and accessories from the fabric. The different materials in the garment – the outside fabric, the lining, the seams – need to be separated, then the different fibres in each fabric (cotton, elastane, polyester, etc.) must be sorted."
Textile sorting is done manually, and only a small portion of the output material is suitable for recycling. However, research is ongoing on automating the process with the aim of producing the high-quality fractions required to address the recycling challenge.
Automated sorting: the path to a textile circular economy
STADLER is researching automated sensor-based solutions for textile sorting. In 2017, in partnership with TOMRA, it designed and built a small pilot project plant in Avesta, Sweden, in the second phase of the government-funded Swedish Innovation Platform for Textile Sorting (SIPTex) project, which aims to develop a sorting solution tailored to the needs of textile recyclers and the garment industry. This was followed in 2020 with the third phase of the project which is capable of achieving the purity and recovery required for recycling and reutilization.
This facility, located in Malmö, processes pre-consumer waste from textile producers (clippings and rejects) and post-consumer waste, which consists of clothing and household textiles, and may contain non-textile parts such as buttons and zippers. The material is delivered in bales weighing from 350 to 500 kilograms and is sorted whole. The plant has the capacity to process up to 4.5 tonnes/hour in one line.
The textile sorting process
The process developed by STADLER, with the cooperation of TOMRA in the SIPTex project, starts with the waste textiles entering the plant in batches, dosed, and fed by conveyor belts into four sensor-based TOMRA AUTOSORT units.
"Because of the nature of the textile material fed into the plant, the feeding system and dosing are very important to the success of the sorting process," explains Dr. Bastian Küppers, engineer for digital business development at STADLER. "The STADLER dosing drum features mechanical components specially designed to handle the soft, flexible textile materials, of various shapes and unpredictable sizes, prone to tangling. Similarly, the design and layout of the conveyor belts, hoppers, and chutes need to be designed to avoid tangling of long pieces of fabric."
The TOMRA NIR (near infrared) sorting technology is also key to the process and capable of recognizing and differentiating various types of textiles in a first step. A second optical sorter is added for further cleaning of impurities.
Towards a textile circular economy
As the textile industry is moving towards a circular economy, driven by public opinion and legislation, the demand for textile sorting equipment is set to grow at an accelerated pace. STADLER has already seen an increase in textile sorting plant interest and has been approached by companies in the recycling sector. "At STADLER we are seeing many interested parties who would like to visit the textile sorting plant we designed and built in Malmö," comments Annika Ludes.
STADLER brings its experience to the table in the design and construction of sorting plants it has acquired through the SIPTex project, as well as the expertise of its technology partners such as TOMRA. With its approach, it is able to develop solutions tailored to the requirements of individual recyclers.