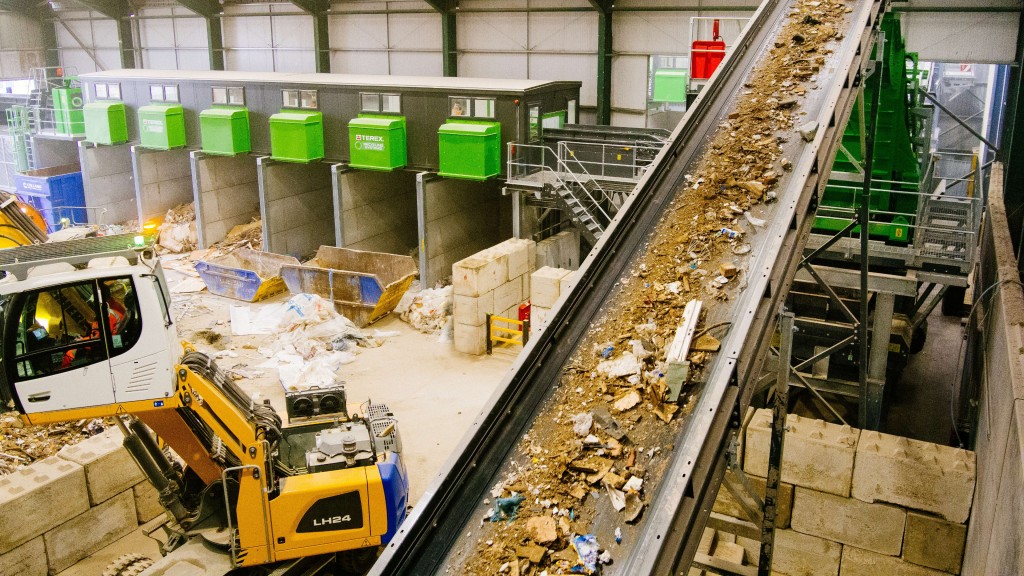
Collard Group has chosen a Terex Recycling Systems plant to increase the processing capacity of its site and recover cleaner products of higher value without adding to the manual labour requirements. Collard Group initially intended to upgrade the plant but opted for a full plant installation after being pleased with the first phase of the installation.
The plant, which is the first Terex Recycling Systems installation, was tailored to suit Collard Group's site and the material which would be fed into it. Terex Recycling Systems developed a process which incorporated advanced mechanical separation that would increase Collard Group's processing capacity and recover products of a higher purity than what was previously achieved. The team worked within restricted space and constraints of fitting the plant inside and around the existing building, all whilst planning the installation around Collard Group's site works, including the erection of a new building.
"We are delighted to have sold and installed Terex Recycling Systems' first plant to the Collard Group," says Thomas McKiver, sales director at Molson Green, distributor of Terex Recycling Systems. "This plant will help them achieve their desired targets of increasing processing capacity and to recover greater percentages of cleaner recycling products, thus diverting more material from landfill."
The process starts with skip material being loaded into a waste feeder and conveyed to a combi screen, which separates material into four size fractions using a combination of 3D and flip-flow screening (0 to 10 millimetres, 10 to 50 millimetres, 50 to 100 millimetres, and over 100 millimetres). Over-band magnets recover ferrous metals from 0 to 10 millimetres, 10 to 50 millimetres, and 50 to 100 millimetres, and air separators remove light material from 10 to 50 millimetres and 50 to 100 millimetres. A manual quality control picking station has operators working to remove any remaining contaminants from the 10 to 100mm heavy fraction. Following this, an eddy current separator recovers non-ferrous metal from the 10 to 100mm heavy fraction. Another manual picking station has operators recovering materials such as wood, card, and plastic from the over 100-millimetre fractions, and an over-band magnet recovers ferrous metal. Finally, an air separator removes light material from the over 100-millimetres fractions.
The outcome is a plant that is processing skip waste – a mixture of commercial and industrial (C&I) and construction and demolition (C&D) waste – to produce 0 to 10 millimetres fines, ferrous metals, clean 10 to 100 millimetres heavy fraction (inert), non-ferrous metals, wood, plastic, paper and card, and clean over 100-millimetre heavy fraction (inert) materials.
"We at the Collard Group are driven by a zero waste to landfill commitment, we take waste from site and process it to make it useful again," says Robert Collard, managing director at the Collard Group. "We call this recycling the past for the future. To achieve this goal, it is important that we have the latest equipment that is optimized to meet our specifications.
"Terex Recycling Systems and Molson Green worked with us to ensure the design, delivery and installation of our new plant worked around our site operations, also taking into consideration our site preparation works to include foundations, building modifications, and power supply. Close collaboration between all parties ensured our requirements in terms of output were met, whilst also keeping the plant footprint to a minimum to aid their site operations."