Get more buck for your bulk with handheld material analyzers
Increase recycling profits with rapid identification for metals and alloys
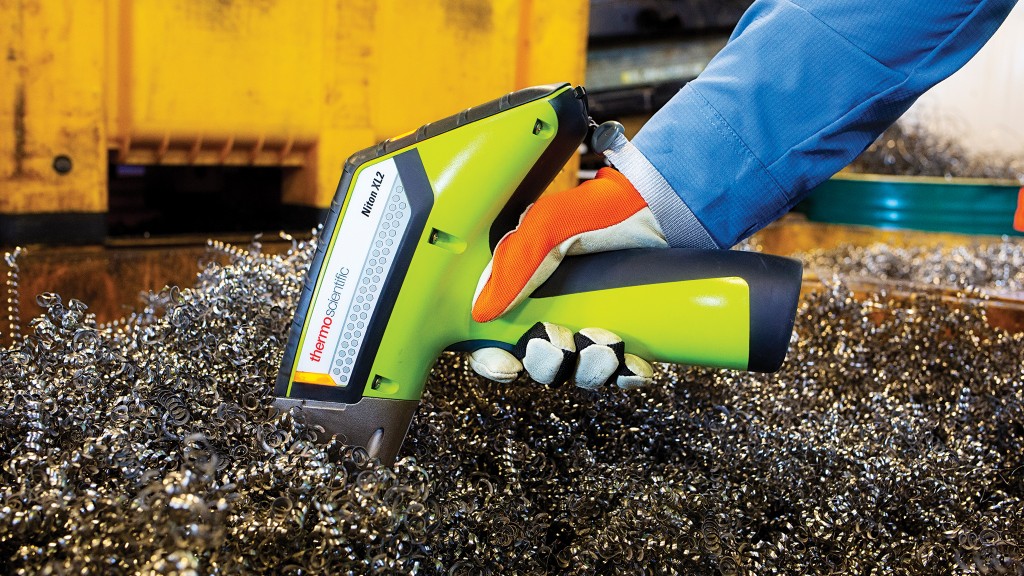
Recycling metals saves precious resources and is also cheaper compared to mining new minerals since less energy is required. However, this approach would not be feasible without efficient ways to determine the composition of the materials earmarked for recycling.
There are a number of non-destructive methods available that can do this - including X-ray fluorescence (XRF) and laser induced breakdown spectroscopy (LIBS) - that are commonly used for positive material identification (PMI) across many different industries to rapidly identify metals and alloys, including sorting and classification of alloys in bulk scrap. Both XRF and LIBS have their advantages and drawbacks, and choosing which of these two technologies is most appropriate for any one application is not straightforward.
Scrap recycling is a growing industry, driven by environmental concerns and an increasing scarcity of raw materials. However, it is extremely important that the exact chemical composition of any material for recycling is known, and that it has been checked for contaminants and hazardous elements to ensure quality, safety, and regulatory compliance when selling scrap metal to industrial consumers. Quickly pinpointing the most valuable materials in scrap can also be very profitable and soon provides a return on investment on analytical equipment.
Handheld devices such as XRF and LIBS analyzers offer recyclers tools to rapidly and accurately determine the composition and grade of incoming scrap. This eliminates the need to send samples away for analysis or rely on the old ways of verification - using spark or chemical tests - that require material grinding, as well as the storage and handling of hazardous materials. In contrast, XRF and LIBS analyzers can rapidly verify high-value elements in virtually all types of metal alloys, from trace levels to commercially pure metals. These latest analyzers are even capable of distinguishing alloy grades that are nearly identical in composition to one another such as 304 and 321 stainless steels, or L grade versus H grade 316. Both offer different benefits when performing sorting, particularly in terms of their accuracy for analyzing different types of materials. So, how do they work, and what's the difference between what they can achieve?
Accurate scrap metal sorting helps to ensure industrial customers receive materials that meet their production needs, as well as increasing the recycler's profits and ensuring product safety.
XRF analyzers
Handheld XRF analyzers produce X-rays that are directed at the surface of a sample. The X-ray energy displaces electrons in the sample atoms, causing each element in the sample to produce a set of characteristic fluorescent X-rays which can be used like a unique fingerprint to identify it. The detector collects the characteristic X-rays and converts them into electronic pulses, which are sent to the central processing unit (CPU). The CPU produces a detailed compositional analysis and grade identification of the material. This is a non-destructive process that has no impact on the sample being inspected with results available in seconds.
Handheld XRF analyzers are tried and tested in the world of scrap metal recycling, and are well established in many organizations as the best-known method for operators aiming to sort scrap quickly and accurately. The technology is very useful for distinguishing between different grades of material, such as determining different stainless steels within a container. However, XRF is unable to identify lighter elements - generally below magnesium in the periodic table - as the energy released by these low atomic number elements is too low to be detected.
LIBS analyzers
Handheld LIBS analyzers use a high-focused laser to ablate the surface of a material, forming a plasma made up of electronically excited atoms and ions on the surface. As the atoms decay back into their ground states, they emit characteristic wavelengths of light, which act as a unique fingerprint for each element in the sample. The emitted light is transferred through fibre-optics, and enters the spectrometer, where it interacts with a diffraction grating, splitting it into component wavelengths before it passes on to the detector. The resulting spectral data is processed by the CPU to provide a detailed composition analysis of the material. Although this technology is minimally destructive, the impact on the sample can be considered very small.
LIBS analyzers are still the new kid on the block when it comes to scrap metal analysis, with XRF having been the technology of choice for many years. But LIBS has some significant advantages that mean it should be seriously considered.
Since it is an optical method that measures light in the NIR, visible, and the UV spectrums, it can analyze a broader range of elements compared to portable XRF, which cannot measure those lower atomic number elements. This is particularly relevant when it comes to measuring carbon, because customers need to be aware of the carbon content of alloys as this has a direct impact on welding properties, hardness, and toughness of the material. Aluminum is also easier to sort with LIBS technology, but is not as effective when it comes to sorting heavy metals, high-temperature alloys, and stainless steel.
Which technology should you choose?
XRF analyzers are often still the technology of choice in scrap recycling centres, but handheld LIBS and XRF should be considered complementary rather than competing technologies. When used together, they can measure a greater range of elements across the periodic table. Both types of analyzer are portable and can identify a material in just a few seconds. LIBS has the advantage of requiring minimal safety training or special storage, since it does not use X-ray radiation. Overall, they are both very useful tools for identifying the most valuable scrap and also ensure that recyclers can provide customers with safe, correctly identified products.
Jim Pasmore is a consultant at Thermo Fisher Scientific.