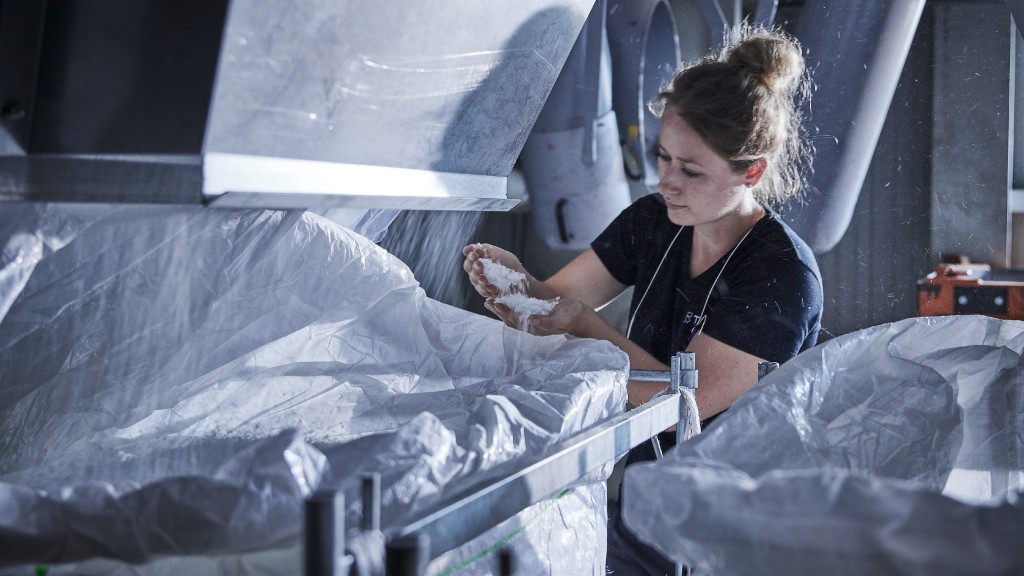
Brand owners and packaging converters in the plastics industry are facing major bottlenecks in recycled content availability. To overcome this challenge and meet ambitious recycling targets, recyclers and material recovery facilities (MRFs) are using advanced technologies to produce feedstock for high-grade applications, expanding their business opportunities.
As legislation continues to push for a reduction in plastic waste, the drive for greater plastics circularity and maximizing resource use is a topic of global concern. Plastics are durable, efficient, and convenient, which makes them beneficial to consumers and businesses alike. Making consumer products and packaging more sustainable is a major challenge of our time. As brand owners look to increase the share of recycled content used to reduce their production emissions and meet consumer demands, they are met with a new set of challenges. High-grade applications like automotive and packaging require high-quality recycling processes and advanced sorting technologies to effectively source feedstock from post-consumer and post-industrial plastic waste.
Supply & demand gaps
Over a 50-year period from 1966 to 2016, global plastic production increased nearly 20-fold, from 20 million metric tons (MMT) to 381 MMT. In 2019, 19 percent of global plastic production occurred in North America, and plastic production is projected to increase by 200 percent and 350 percent by 2035 and 2050 respectively. In the quest to create a circular economy for plastics, the share of virgin material in manufacturing should be reduced and replaced by secondary raw materials.
Plastic recycling has certainly had its share of bad publicity, not least due to downcycling - after all, there is a limited demand for items such as park benches, flowerpots, and speed bumps. The recycling industry, working in collaboration with members of plastic value chains, has now made it possible to create virgin-like recycled content with advanced mechanical recycling. Not only does this prove to be an economically feasible and practical alternative to primary materials, but it gives recyclers and MRFs the opportunity to create new revenue streams. Even in the case of highly contaminated plastic waste streams, like municipal solid waste (MSW), it is now possible to source quality feedstock that can be used to create new products.
The S&P Global Platts Analytics predicts that by 2030 more than 1.7 MMT of virgin polymers will be replaced by mechanically recycled plastics - compared to 688,000 metric tons in 2020. To date, less than 10 percent of recyclates have found their way into the production of new materials. Most of the recyclates are used for lower-grade applications. So, how can industries such as automotive, food and beverage, and cosmetics ensure a reliable supply of high-quality recycled feedstock? Bridging the gap of material shortages starts with the effective collection of recyclables and continues by deploying the latest sorting technologies in modern processes and configurations.
On the front end, deposit return systems (DRS), for instance, are a global best practice for the recycling of beverage containers in a closed-loop system. Mid-recycling supply chain, innovative optical sorting, and other separation technologies maintain yield and quality. On the tail end, advancements in flake sorting have significantly contributed to closing the remaining quality gaps for many plastics.
However, there is no one-size-fits-all solution. To achieve circularity, complementary solutions are needed to capture and recover various packaging materials. Mitigating contamination and increasing the quantities of recovered recyclates across all waste streams is crucial to the future of plastics.
Advancing U.S. recycling infrastructure
In addition to conserving valuable natural resources, recycling is a key economic driver in the United States. Released in 2019, the EPA's National Framework for Advancing the U.S. Recycling System mentions that recycling and reuse activities in the United States account for 757,000 jobs, $36.6 billion in wages, and $6.7 billion in tax revenues. Astoundingly, recyclable materials with a commodity value of approximately $8.9 billion are still sent to landfills each year.
A regenerative approach is required to increase material recycling and reuse efforts, drive greater plastics circularity, and provide a long-term supply of recycled content for the market to reduce dependency on primary materials. For this reason, many countries around the world and several U.S. states are considering or have already introduced Extended Producer Responsibility Schemes (EPR), which give producers significant responsibility for the product's lifecycle - from design to the post-consumer stage. These policies incentivize producers to consider environmental factors when manufacturing packaging and to contribute to a reduction of the product's environmental impact.
Aligned with companies creating a profitable business model, legislation plays a fundamental role in supporting infrastructure investment, including effective collection, sorting, and recycling of plastic waste. Plastic directives and mandatory minimum recycled content targets can establish the proper framework for prioritizing circularity and breaking the bottleneck of feedstock recovery.
Binding frameworks constitute a necessary intervention in the market. They support sustainable waste management and stimulate the industry to increase the use of recyclates while securing demand and infrastructure investment. The EPA's National Recycling Strategy focuses on enhancing and advancing the national MSW recycling system and supports the implementation of the National Recycling Goal to increase the recycling rate to 50 percent by 2030.
In July 2022, California enacted the country's most sweeping restrictions on single-use plastics and packaging. The law requires single-use packaging and plastic single-use food service items to be recyclable or compostable by 2032, and it requires a 25 percent reduction in the sales of plastic packaging plus 65 percent of all single-use plastic packaging to be recycled within the same time period.
As much as it seems that we are headed toward a circular economy, we have a long way to go. The Last Beach Clean Up and Beyond Plastics report, "The Real Truth About the U.S. Plastics Recycling Rate," documents a recycling rate of just five to six percent for post-consumer plastic waste for the United States in 2021. Juxtaposed against declining recycling rates for plastics, the per capita generation of plastic waste has increased by 263 percent since 1980.
In sharp contrast to abysmal plastic recycling rates, paper enjoyed a recycling rate of 65.7 percent in 2020, according to the American Forest & Paper Association. Post-consumer paper, cardboard, and metals all enjoy high recycling rates in the United States, proving that recycling works to reclaim and save valuable natural resources. It is plastic recycling that has been the failure point, never reaching 10 percent, even before China enacted its National Sword policy.
While directives are a decisive step forward, there is still room for improvement. For instance, there is little legislation specifying the use of post-consumer recycled content (PCR) that could fill the gap between demand and supply. The state of California leads the most ambitious targets for PCR in beverage bottles. The recently established California Recycled Content Laws set PCR targets at 15 percent by 2022, 25 percent by 2025, and 50 percent by 2030.
Advanced mechanical recycling and collaboration along the value chain
Increasing the use of recycled content requires the entire industry to act, design recyclable packaging, and improve the supply of quality recyclates with both new and existing instruments. Applying the Holistic Resource Systems approach to waste management combines DRS, separate collections for selected material streams and mixed waste sorting to recover plastics for advanced mechanical recycling.
Beyond dedicated collection streams, the addition of mixed waste sorting is also proving to deliver high-quality plastic for recycling. In California, Santa Barbara County's new ReSource Center recovers recyclable materials from commercial and residential waste, pushing the region's landfill diversion rate above 85 percent and reducing Greenhouse Gas Emissions equivalent to those generated by 28,668 cars. A case study with AVR, a residual waste sorting plant in the Netherlands, demonstrated that mixed waste sorting with high-performing technologies can capture 12 times more plastics for recycling, cutting down on CO2 emissions.
Today, recyclers and sorting plant operators are faced with the task of cleaning contaminated waste to a level suitable for further processing or local trading. At the same time, brand owners and converters that buy PCR are demanding high-purity mono fractions, sorted by polymer type and colours. By adopting new sensor-based sorting technology, plant operators can effectively sort and purify high-value plastics from waste streams to supply PET or PO fractions to the market. To create more valuable products, a combination of pre-sorting and flake sorting solutions is needed.
First, near-infrared (NIR) sorters separate targeted plastics from contaminants such as unwanted polymers and foreign materials. The purified plastics are then shredded, washed, and dried. The resulting plastic flakes are then processed in a secondary step with a high-precision flake sorting system that can sort flakes as small as 0.80 in (2mm). These ultra-flexible systems enable operators to define whether they'd like to sort materials by polymer type and/or colour, creating products specifically tailored to even the most demanding requirements. The sorting technology featured in these systems can sort a vast range of colours, including the highly demanded natural, clear, and light blue flakes, as well as all bright colours while ensuring maximum polymer purity. Thus, operators are given the means to minimize contamination levels and supply the industry with high-quality materials they can process into virgin-like recyclates.
While most recyclers prefer plastics coming from single material streams with lower contamination levels, operators can source more materials to meet demand by ‘cleaning' plastics of impurities. Post-consumer packaging waste, for instance, can be an excellent source of recyclable polymers and is available in large quantities. Although more contaminated compared to post-industrial plastic waste, sophisticated sorting systems can automatically recover and purify the materials by utilizing advanced mechanical recycling processes. This too would increase the availability of PCR material on the market.
Collaboration is key in plastic recycling. Improving recyclability and increasing the quantity of recycled content demands that the industry go upstream because high-quality recycling begins in the design phase. Brand owners are incentivized to implement design-for-recycling to help facilitate the sorting process. The more complex and colourful the product's design, the more difficult it is to sort and recycle. Thus, to maximize resource recovery, product design, sorting technology and the overall process must complement each other. With all methods, from the product's design to its end-of-life management going hand in hand, it is evident that change does not come from a single actor in the value chain. To innovate and transform the industry, everyone must play their part, and we all must come together in new ways.
The recycling sector offers tremendous potential, but limited recycled content availability, low-quality recyclates, and a lack of financial incentives seemingly impair its evolution. Consumer values and purchasing behaviour, legislation, and supply chain vulnerabilities signal that it is time to reduce waste and make recycling a priority. Highly efficient sorting processes that enable MRFs and recyclers to create high-purity mono fractions from even the most contaminated waste streams will ensure a long-term supply of recycled content. As part of the roadmap to the circularity of plastics, the capability to create virgin-like recycled content opens new revenue streams for sorting facilities and recyclers while reinforcing local trading. Using sensor-based sorting technologies provides an economic advantage to the entire plastics value chain.
Eric Olsson is the area segment manager plastics at TOMRA Recycling Sorting
Company info
TOMRA of North America - 4820 Holtz Dr.
Wixom, MI
US, 48393
Website:
tomra.com/en/collection