Q&A: Amy Brackin of Liberty Tire talks industry challenges, EOL programs, and the future of tire recycling
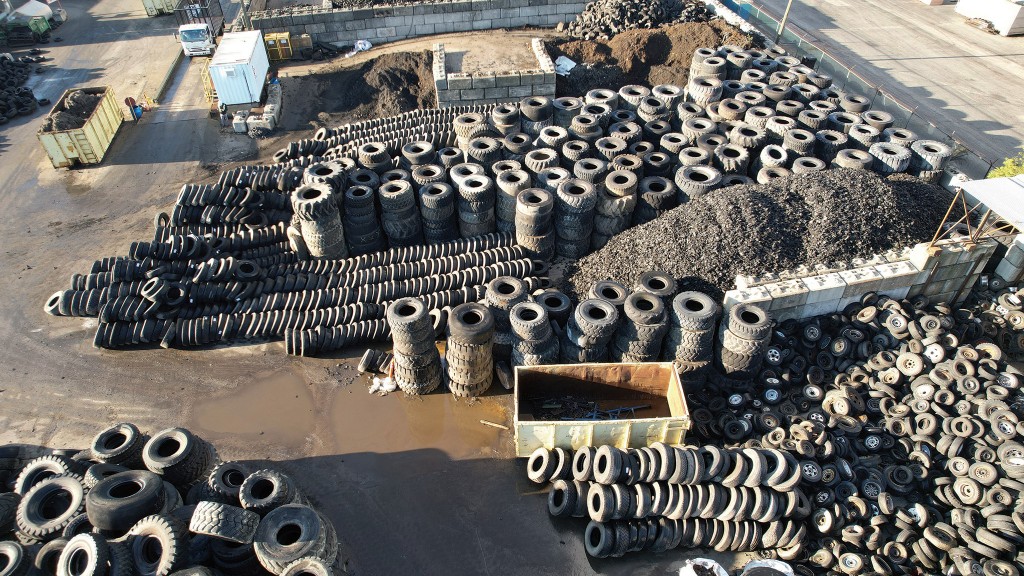
As the recycling industry continues to push toward the adoption of a more circular economy, waste that was once viewed as a burden is now being recognized as a resource. This is especially true with end-of-life (EOL) tires, which have become one of the most recycled materials on the planet, according to a report by the U.S. Tire Manufacturers Association.
Liberty Tire Recycling is at the forefront of ongoing efforts to turn these scrap tires into usable materials, and has been for decades. Through collaborative partnerships, remediation efforts, and extensive R&D, Liberty Tire manages the collection of nearly 200 million tires each year with more growth on the horizon. I caught up with Amy Brackin, senior vice president of sustainability at Liberty Tire, to discuss supply chains, market challenges, recycling program efficacy, and more.
Slone Fox: Can you describe your supply chain for these end-of-life tires?
Amy Brackin: Liberty Tire is North America's largest network of tire recycling facilities with operations across the U.S. and in both British Columbia and Alberta. We have a vast and complex supply chain, accepting and processing virtually any kind of tire - passenger car, truck, agricultural, commercial, and even large mining tires that are 13 feet in diameter. We have over 400 trucks in our transportation fleet, and we're able to effectively manage the collection of nearly 200 million tires from over 39,000 retail and customer locations every year.
From these collection locations, the tires are transported by our truck fleet to Liberty Tires' various recycling facilities, where they're shredded, ground, and go through multiple material removal processes. The resulting products then move to secondary manufacturers, and finally, are transported to an area for end product use.
In addition to our typical collection efforts, we support tire cleanup efforts both through the remediation of illegal dump sites and local and regional amnesty programs that encourage the public to dispose of end-of-life tires.
SF: Can you explain the tire remediation side of the business in a bit more depth?
AB: A major portion of our remediation evolves from companies that start a business or idea without understanding the challenge of balancing inbound EOL tires with outbound markets. Over time, these companies build a large stockpile of used tires with no outlet and are forced to walk away, leaving the pile for state, municipal, or other levels of local or regional governments to clean up.
Liberty Tire works in conjunction with various levels of government, individuals, businesses, and customers to seek out and participate in cleanup efforts of both relatively small and very large waste tire piles. These projects include a range of different activities, such as providing workforces to facilitate multiple shoreline and roadside cleanups; directing personnel and equipment at local amnesty events which encourage individuals to drop off higher than usual numbers of EOL tires; and the mobilization of heavy equipment and specialized transportation methods for larger scale collection activities. Over the past 20 years, we've remediated more than 50 million tires from several hundred project sites.
SF: What types of machines and equipment are used during the tire recycling process in terms of sorting and separation, steel removal, etc.?
AB: Depending on the ultimate end market for the material, we use a variety of shredders, magnets, air systems, granulation equipment, screens, and bagging stations to produce quality products.
As a tire comes into our facility, it's unloaded from a transport truck where it's placed on a conveyor belt that leads into a sequence of shredders. Along the way, wire is removed using a series of magnets, and fibre is separated using sophisticated air systems. To achieve the highest quality end products, oftentimes various grades and sizes of materials will be passed through a series of screens to ensure they consistently meet customer specifications.
SF: What are the current end markets for the materials produced during this process? Are there any emerging end markets on the horizon?
AB: There are many well-developed markets for the use of recycled rubber in everyday items ranging from your front door welcome mat to landscaping mulch for your flower beds. Items you may not even realize are sourced from recycled rubber include the base of an orange traffic cone at a road construction project where crews may even be paving with rubberized asphalt. Our products could also form part of the splash block at the end of your rain gutter, or the landscape edging used around your garden. Even the rubber flooring you see in your local gyms – and the weights you use while you're there – are being made from recycled tire rubber every day. When we engage in EOL tire conversion, we recycle all parts of that tire including the metal, which is sent back to smelters and repurposed in the manufacturing of new steel.
There are exciting new emerging technologies such as devulcanization, gasification, and pyrolysis that are opening the doors to many new market opportunities because these technologies produce net new raw materials. We also see a growing market in the use of finely ground recycled rubber going back into the manufacture of new tires. Rubber is becoming more prevalent in extrusion applications where it may be blended with plastics and compounding efforts. We've even seen early research regarding the use of recycled tire rubber in graphene – a highly technical and sophisticated application.
In order to create a sustainable future for end-of-life tires, there is no silver bullet that is going to get us there. We need all of these markets and more to eliminate the disposal of tires and continue to move product offerings up the value chain to more renewable solutions. It will take time and requires the innovation and contribution from all segments of the industry to get there, but we firmly believe we're headed in the right direction.
SF: From your perspective, how effective are current end-of-life tire programs and what are some of the challenges and opportunities that they present?
AB: Across our operating landscape, there are a variety of ways end-of-life tires are managed in the U.S. and Canada, and we view all of them as successful. For decades, we've been committed to supporting a more circular economy by finding new and better ways to not only collect and recycle end-of-life tires, but to support innovation and new market development for recycled rubber products. Our focus is on ensuring a high recycling rate and responsible management of end-of-life tires, and we've been able to effectively operate in a variety of different environments and regulatory structures.
The biggest challenge for any of these programs is that in general, we do not believe that the mere introduction of a program such as extended producer responsibility (EPR) or individual producer responsibility (IPR) necessarily drives market growth or development, which is the ultimate desired outcome. We've also found that in some cases, entities use EPR and IPR programs as marketing tools for their business which misinterprets its true intent. The intent is to ensure that EOL solutions continue to improve, and we're pleased to see that happening in most jurisdictions across the U.S. and Canada.
SF: What are some of the main challenges that the tire recycling industry is currently facing?
AB: While the industry has its challenges, the reality is that tires are one of the most recycled materials on the planet and one of the most widely studied.
Liberty Tire is investing capital and energy into a range of opportunities, including the development and growth of new products and new markets. This requires collaboration across the industry and honest conversations about options for end-of-life tires. Interestingly, the growth of the electric vehicle [EV] market will actually increase the number of tires being recycled every year. An April 2022 study from Clean Fleet Report shows that for a variety of reasons, including increased weight and higher torque, tires are proven to wear out roughly 20 percent faster on an EV than on an internal combustion engine vehicle.
SF: Where do you see the tire recycling market heading in the future?
AB: We're very excited about the future and believe that looking at ways to vertically integrate will strengthen our ability to establish new markets. As the focus on sustainability continues to grow in the minds of the consumer, and companies increase efforts to provide solutions for a truly circular economy, innovation will pave the way to creative new uses for a material that has so many valuable properties.