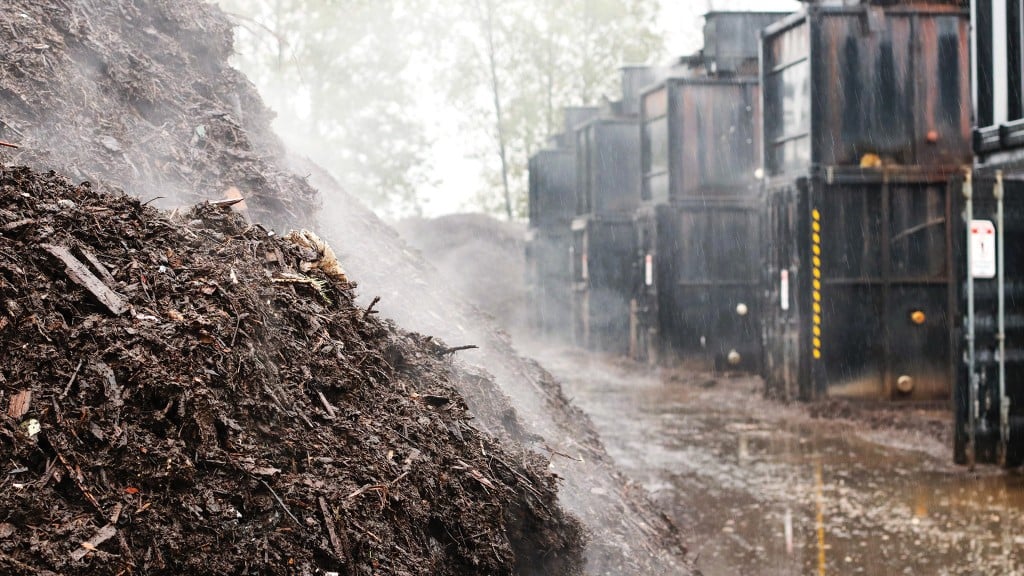
Russell Zishiri has always had an entrepreneurial mindset. He first got his start in the recycling industry over a decade ago while operating his own hauling business in Vancouver, British Columbia. Each day after collecting a box truck's worth of organic materials, he would make the bumper-to-bumper, two-and-a-half-hour round trip commute to the rural processing facility. He wasn't the only hauler making this trek.
Experiencing this frustration day in and day out sparked an important realization for Zishiri: if the lengthy drive is such a widespread issue, why not bring the processing facility closer to the city? By addressing the factors that have historically prevented organics facilities from existing within city limits – odour, land costs, and permitting – processing could exist closer to home and cut down on commutes and costs for haulers.
This led Zishiri to embark on a research project supported by the National Research Council of Canada's Industrial Research Assistance Program. After analyzing close to a hundred existing technologies currently in the marketplace, he decided that there was still more that needed to be done.
"There was nothing that could do what we wanted, which was something with a high throughput, low footprint, low capital expenditure, and the ability to be permitted in the city," says Zishiri.
Drawing upon his expertise and existing relationships in the commercial waste industry, Zishiri established organic waste processing company Anaconda Systems to help solve some of these common pain points within the industry, successfully opening a pilot facility in Vancouver in 2017. The facility's convenient location allows haulers to tip waste mid-route without leaving the city, helping municipalities and private waste companies increase efficiency and reduce costs.
"We have customers that are institutional, industrial, and commercial. So the waste comes from any sort of food production, from restaurants to hotels, and that's through the commercial haulers. And ultimately, for them, it's an effective way to be able to increase productivity with short trips," says Zishiri. "Our facility is centrally located, so if you're in downtown Vancouver you can empty your truck within 15 minutes. That's a valuable option for companies, allowing them to double productivity with their trucks by collecting more material and competing more effectively in the marketplace since they need less equipment to do the same work."
The challenges of urban waste management
Processing organic waste in urban areas comes with plenty of challenges. There are capacity issues, tricky permitting processes, strong odours, and the large amount of land required for processing which can be extremely costly in the city. And since most cities generate more organic waste than they can process, this leaves two options: shipping it out of the region, or leaving it to rot in a landfill where it will generate methane, producing significant greenhouse gases.
Faced with these two undesirable options, Anaconda Systems created an alternative choice: a proprietary, in-vessel composting system capable of turning organic waste into high-quality fertilizer supplements in 96 hours, about 1/9 of the standard processing time. The enclosed design and assembly line process uses aerobic digestion with no mechanical agitation, allowing for high-speed throughput and processing that reduces odours and maintenance.
"From end-to-end, our materials go through an enclosed system, even the pre-treatment," says Zishiri. "It's enclosed, it has a low footprint, and we can rapidly move through the materials and have no adverse effects on the surrounding community and environment. And obviously, being in Vancouver, acquiring the permits that are required to do this kind of work in the city is a demonstration of the ability to be able to process these materials within the region."
Aerobic versus anaerobic digestion: which is better for urban waste streams?
At the most basic level, the differences between anaerobic and aerobic digestion are simple: aerobic systems require oxygen, and anaerobic systems do not. While anaerobic digesters take organic waste and transform it into biogas, urban organic waste is volatile, and often too contaminated with materials such as yard waste, plastics, and metals to be a viable feedstock for that process. There are other challenges as well.
"The costs of anaerobic digestion can be prohibitive, especially for smaller municipalities. And the permitting around anaerobic systems is much more complex and lengthy because of the gas and all of the extra risks that come with that," says Zishiri.
Due to the complications and challenges associated with anaerobic processing, aerobic digestion was the natural choice for Anaconda Systems. With technology specifically designed to work around the contamination challenges of urban waste streams, Anaconda Systems utilizes aerobic digestion in its operations to simplify the process and cut costs, making its technology affordable for most municipalities and private waste services. Utilizing an aerobic system also has the added benefit of producing a high-quality end product that is suitable to sell on the market, further increasing revenue streams for the company.
Most traditional processing methods can only operate outside of populated areas due to the smell, something that has proved to be a key pain point when it comes to processing waste within city limits. Located just a few blocks away from residential areas on only 3.5 acres of land, Anaconda Systems' facility is also 87 percent smaller than most facilities, allowing it to fit almost anywhere and scale to meet customer needs, while also reducing the odours that are traditionally associated with organic waste.
"Being able to process the material rapidly in less than 10 days is what allows you to save space and cut costs. Each unit has 90 tonnes of static capacity, so the longer the materials are in the vessel, the more containers that you need. Ultimately, in order to take up less space, you need to be able to process materials in short cycle times," says Zishiri.
"In terms of developing our technology, a key focus was to maximize the biological reaction that's happening inside the vessel so that material is digested and pasteurized in the shortest time possible. This allows us to move through organic waste with less vessels and land. The sweet spot for us is 30 to 60 kilotonnes of organic waste per annum, and we only need three to five acres of land to build a facility. For larger municipalities, multiple facilities can be built and be distributed throughout a region."
Anaconda Systems' proprietary process
Anaconda Systems' pre-treatment process separates contaminants and inorganic materials from organic waste. After adding its own unique formula to the treated waste, the company is left with a homogenous material ideally suited for rapid digestion using Anaconda's proprietary aerobic system.
"The key is our pre-treatment process and recipe that creates the substrate that we need before it goes into the processing unit," says Zishiri. "Our recipe combined with our proprietary aeration strategy allows our system to rapidly process organic waste.
"Once the material is loaded into the unit, the pile in the vessel is fully aerated all the way from top to bottom. Without mechanical agitation, 100 percent of the material reaches a temperature of 55 degrees Celsius, and that temperature is maintained for three consecutive days to meet regulations. Each vessel is fitted with a biofilter to take care of any odours and funky smells that may be produced. And in less than 10 days, the organic material is fully processed."
The output from the entire process is a high-quality fertilizer supplement that is then sold to local farms to grow food, helping Anaconda Systems create a circular waste stream by processing any resulting food waste back into usable fertilizer to start the process over again.
"Ultimately, our NPK [nitrogen, phosphorus, and potassium] ratio is actually higher than regular output. We've tested it against regular composted material and it's about 50 to 60 percent more potent. We have some commercial farmers that we've been working with over the last few years that are looking at it as a replacement for synthetic fertilizer. It's not just the nitrogen, phosphorus, and potassium that is in there, but all the other minerals, too. Outside of the nutrients, our output also increases the water retention of the soil, allowing for healthier root growth. And because of our pre-treatment process, we have basically no contamination in the output product which is important to farmers."
Growth on the horizon
What began as one man searching for a solution to a prevalent problem within the collection industry has now grown into an operation that processes over one million pounds of organic waste each month with the potential to reach over four million pounds in just one facility alone. Although investing in organic waste treatment can be complex and costly, Anaconda Systems has found a way to treat materials close to home in a viable way, eliminating virtually all pain points that previously prevented such facilities from operating within city limits.
By demonstrating the facility's ability to process waste within the city while also producing a valuable end product, Zishiri anticipates Anaconda Systems' technology will continue to expand in the waste industry, allowing for more in-city tipping and processing with very little greenhouse gas emissions, benefitting both companies and the environment.
"We weren't after disruption," says Zishiri. "What we were after was finding a solution for when I was trucking it. That's how it came about."
As the years progressed, Zishiri and the Anaconda Systems' team knew they needed new infrastructure to be able to process organic waste in the way that they envisioned. And while larger municipalities didn't want to pay hundreds of millions of dollars to build new facilities, many smaller municipalities hit the sweet spot of between 30 and 60 kilotonnes of organic waste per year, making them the perfect candidates for Anaconda Systems' technology. Following the success of the Vancouver pilot facility, Anaconda Systems has plans to expand its solutions to other municipalities by commissioning and installing both small- and large-scale facilities.
"Where there's no land and consumption abounds, there's an opportunity for us to be able to create a circular system," says Zishiri.