How investing in shredding equipment is maximizing efficiency and revenue for metal recyclers
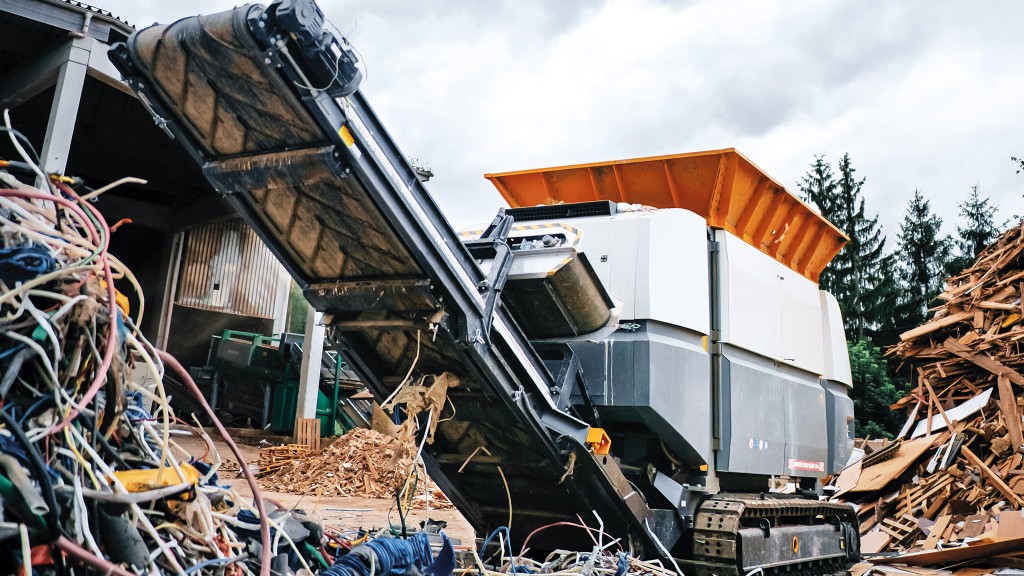
The scrap market represents one of the most established circular concepts to exist in the material recycling industry – smelting old metal to manufacture new metal. But that doesn't mean waste contractors must be reliant only on traditional handling techniques and conventional recycling machinery.
Some scrap merchants continue to use the equipment they feel most comfortable with. They default to traditional shears to cut metals down, for example, because the perceived high-wear nature of the application means alternative methods are considered too expensive. But failure to look beyond these large, cumbersome pieces of equipment means that ever-smarter sorting, grading, separation, and size reduction technologies are dismissed. An investment in such technologies shouldn't be considered a non-recoupable expense, because as engineering advancements continue at pace, it's possible to enhance the efficiency, sophistication, and potential revenue yield of metal recycling lines through the improvement of metal recyclate quality.
The metals "locked" inside waste
First, it's important to think about where metals can be found. While some products have obvious metallurgic content, in other waste streams the metals are "locked" inside, making them a less appealing recycling focus. However, while they may once have been considered difficult to process, they can now be handled with relative ease, thanks to technological innovation.
Think about e-scrap (or WEEE – Waste Electrical and Electronic Equipment - as it is known in some parts of the world). Consumer demand for electronic products is currently rising by 2.5 million tons per year, making WEEE the world's fastest-growing waste stream. But if this producer trend continues at the current accelerated rate, it's estimated that the worldwide total would be an eye-watering 74.4 million tons by 2030.
However, only 17.4 percent of 2019's 53.6 million tonnes of e-waste was formally collected and recycled – not only posing significant risk to the environment, but representing millions of dollars of lost revenue and resources. This is a huge quandary for the supply chain to solve and it won't be easy, but when it comes to the actual processing of e-scrap, there is evident progress to be made.
Some certified and specialist handlers prefer to break down redundant equipment manually, by hand – affording the opportunity for inspections that explore reuse potential too. However, there are instances where this method is too time consuming, onerous, and labour intensive – not to mention often more limiting in terms of recycling effectiveness. This is when the mechanical processing of e-scrap may be more appropriate.
Shredding the scrap helps break down the "waste" into its component parts, so that the various ferrous and non-ferrous metals, precious materials, and plastic can be liberated. Downstream separation equipment is then better able to segregate these clean, high-value material streams with ease for onward recycling and remanufacturing. The result is a more commercially and environmentally robust operation.
This approach is relevant not only to e-scrap, but to other waste streams where metals may otherwise remain locked inside the material – anything from mattresses to uPVC windows, and even pulper ropes from the paper manufacturing industry.
Think also about commercial and industrial waste processed in MRFs and alternative fuel production plants. Fe and non-Fe magnets can extract material from the lines, but if the metal is contaminated with other substances, such as plastic film, it is almost worthless. However, a shredding operation - perhaps with density separators and other sorting technologies such as NIR for further segregation - can clean up the metal, resulting in maximum volumes of high-quality ferrous and non-ferrous scrap for resale.
Building a shredder to meet recyclers' specifications
Robust four-shaft shredding equipment – with a screen to regulate output particle homogeneity – is often the go-to choice when processing metal. Ideally, the machine should be high torque and slow speed for reduced dust, low wear, increased uptime, and added efficiency. Typically, such technology can be found in compact models for light e-scrap, such as computer hard drives, through to much larger alternatives for heavier-duty applications.
Single-shaft machines have also evolved to further change the face of what's possible in this arena. UNTHA has customers using the XR3000C-HT waste shredder with high-torque drive, for example, to shred tricky material like cables – including Steel Wired Armored, MICC or MI, domestic electrical, pluggy cable, automotive wiring harnesses, and plugs and sockets – at high volumes. Throughputs vary depending on the application and output specification requirements, but they can reach up to 20 tph for this material type.
Innovation has continued further still, with the recent development of the ZR2400 two-shaft pre-shredder, engineered specifically to process tricky materials at high volumes. The ZR2400W model is ideal for the shredding of metal scrap (Al-Cu coolers, Al mixed, Al profiles/Al wires/Al sheets, Al-ISO profiles, Al wheels), and large domestic appliances - such as washing machines - as well as WEEE. The goal is to achieve a rough material breakdown (90 percent <300mm) for optimal downstream sorting, making this the ideal machine for metal processors, recyclers, and aluminum and metal manufacturers. This machine is also low speed yet high torque to guarantee throughputs without the wear, which protects the machine from damage and ensures a higher-quality shred.
An interesting feature in the ZR machinery is its independent, bi-directional shaft rotation. This means the shredder's aggressive cutters can grab, shear, and liberate even bulky and heavy-duty material in forward and reverse for a machine action that always shreds.
Both the XR and ZR are also supplied with the UNTHA Eco Power Drive with water-cooled motors – an environmentally efficient concept which has the ability to reduce energy consumption by up to 75 percent. This, and a number of other carefully engineered design features, means that the technology delivers low whole life running costs, greater margins, and strong green performance.
What does the future hold for metal recycling?
Industrial shredding won't always be required to support the metal recycling process. However, for operators who want to prioritize throughputs and on-specification particle sizing to yield maximum environmental and botF-line outputs, it's worth reflecting on the role that such equipment could play in driving progress.
Gary Moore is the sales director at UNTHA UK.