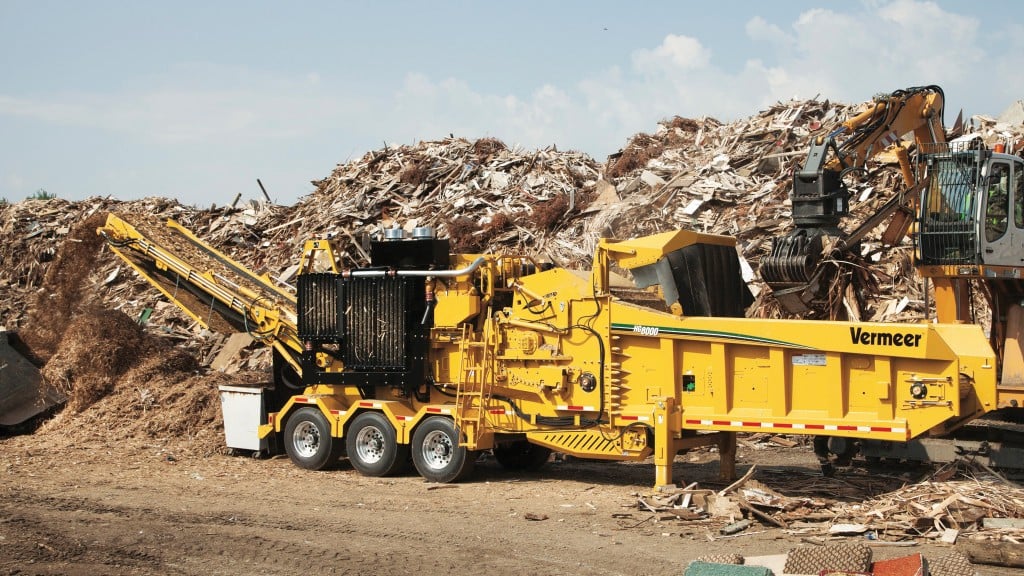
There's no getting around the fact that routine equipment maintenance and upkeep takes time. But savvy operators can help minimize the duration of work stoppages – both expected and unexpected – by taking a proactive approach to equipment maintenance management for machines like horizontal grinders.
But what exactly does that mean? Proactive maintenance is generally about being more attentive to both your equipment and operating conditions and setting yourself up to act quickly and nimbly when a maintenance need arises, according to Ted Dirkx, sales manager for environmental equipment at Vermeer.
Get organized
It starts with good organization. With the knowledge of recommended daily inspections, maintenance, and service tasks, you can organize tools in a way that helps streamline those jobs so you can start up your horizontal grinder and get to work.
Routine maintenance is better conducted when you have the proper tools on hand or close to the job site where your horizontal grinder is working. Dirkx advises operators to think about what maintenance may be required while on the job and keep essential tools close by to perform tasks in a timely manner.
"One best practice is having an entire maintenance trailer or truck readily available for operators to have the tools and means necessary to maintain a horizontal grinder the way it deserves to be," says Dirkx. "But you can really benefit by having a well-organized set of tools necessary to conduct routine maintenance without a lot of excess. Sometimes you want to have only the tools you need to do the job; it may not do you much good to have every tool under the sun on the job site when you have to sort through everything to find one wrench you need, for example."
Go for a walk
The next step in a proactive maintenance strategy for your horizontal grinder is simple: go for a walk. As you inspect the machine prior to beginning work on the job site each morning, keep an eye out for signs of things like minor hydraulic leaks that could become more substantial maintenance issues if not caught early on. Proactive fixes like tightening loose hydraulic fittings where there's evidence of even small leaks can enable you to tend to them as minor maintenance issues before they may turn major, says Dirkx.
"It goes without saying that a machine's cleanliness is directly correlated with how well it's maintained. If covered in dirt or dust all the time, it's likely not being maintained well," Dirkx said. "Piles of debris will not only hide potential warning signs of an early failure, but could cause corrosion issues. Discolouration or paint peeling in the frame or other components around a bearing indicates it's getting hotter than normal and could foreshadow a more major maintenance issue that a proactive walkaround can expose."
Operate by feel
A good operator uses all of their senses to tell if a horizontal grinder is functioning optimally. Oftentimes, even slight damage or wear to parts like the drum, hammer, or conveyor will make its presence known through a difference in vibration or output sizing. Damage like this can affect overall productivity.
In building a proactive maintenance strategy, it's typically best to assign one or a small number of operators to each grinder so that the subtle operational differences that precede a potentially disruptive issue will be repaired before reaching that point.
Know your wear parts
Another area of focus in a proactive maintenance strategy is attention to wear parts, especially how different components fit together operationally and from a cost standpoint. Running cutter tips beyond their expected lifespan can inflict damage to the more expensive hammer component. Being attentive during operation and proactively replacing cutter tips before they reach that point is one tactic that contributes to a proactive overall maintenance strategy.
"It can be risky for an operator to try to milk out an extra four or six hours from a cutter tip because he or she doesn't want to shut down to change the tips. You can push through that point in the name of productivity, but as soon as those tips are beyond their wear point and you start chewing into the hammer, you can do more long-term harm and add cost," Dirkx said. "It's hard to rationalize that in the short term because you're being more productive. But over 5,000 hours, that can add up to significant additional operating costs."
Another wear part that calls for frequent monitoring is the set of screens within a horizontal grinder. As they wear, openings expand, resulting in output that's not sized accurately. Staying on top of screen condition and replacing when the operator notices grindings aren't consistent in size is part of a proactive maintenance strategy.
Loading your grinder
More attentive, proactive equipment maintenance isn't confined to the horizontal grinder itself. The equipment you use to load that grinder – and attention to how the machines interact in the process – can have a lot to do with its performance over time. Wheel loaders and excavators, for example, load material differently, and the process can have varied impacts on the long-term performance of belts, cutter tips, and other wear parts.
"Typically, the heaviest contaminants shuffle their way to the bottom, so using a wheel loader with a grapple bucket loads in more of those contaminants. An excavator works from the top of the pile. The operator can see what he or she is grabbing," says Dirkx.
Create checklists and labels
A lot of work goes into a proactive equipment management strategy, especially for a machine with the number of components and systems like a horizontal grinder. As a way to get organized and streamline the process, Dirkx recommends referring to your operator's manual to help create a daily checklist with only the high-priority components to check when conducting walkarounds prior to beginning work each day. The same is true with component labels; having things clearly labelled on the machine can help operators be more efficient with routine maintenance so they can get to work quicker.
"A checklist in a format that you can print off or apply as a decal on the machine near the operator's station can make for a quick reference," Dirkx said. "And it can be a big help to label everything on the machine - things like where to grease, how much fuel to add, or where the operator should pay extra attention to cleanliness or lubrication. Labelling is a really inexpensive way to be more proactive with routine maintenance."