AMP Robotics launches automated secondary sorting facilities in Atlanta and Cleveland
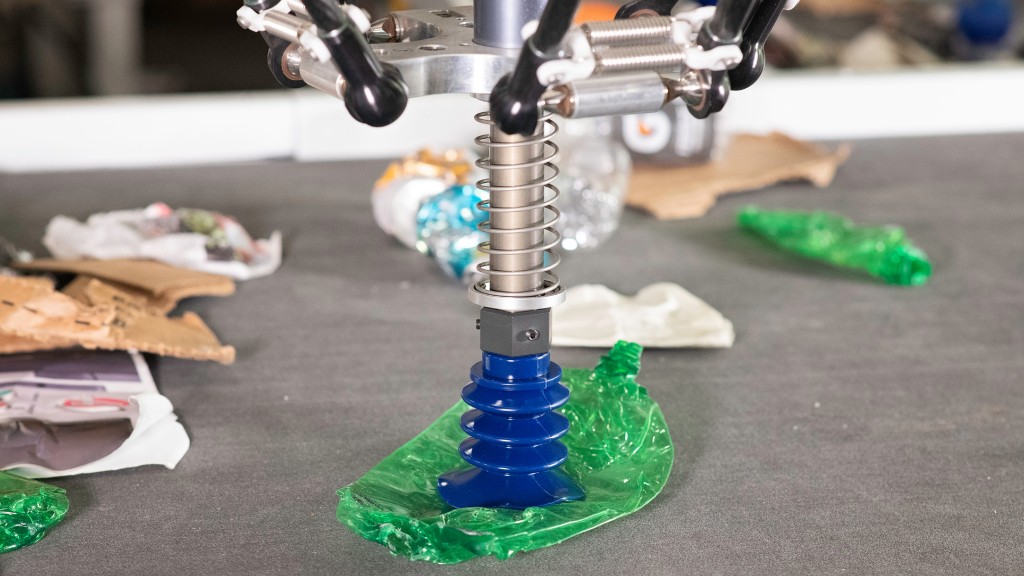
AMP Robotics Corp. has introduced two new high-diversion production facilities based on its infrastructure model for advanced secondary sortation. The company-owned facilities, located outside of Atlanta and Cleveland, are designed to process and aggregate low volumes of difficult-to-recycle mixed plastics, paper, and metals sourced from residue supplied by primary materials recovery facilities (MRFs) and other material providers.
"With the success of the pilot facility we launched last year in Denver, we've been working hard to bring online additional facilities powered by our application of AI for material identification and advanced automation," said Matanya Horowitz, founder and CEO of AMP Robotics. "This secondary sortation model is helping to address the millions of tons of recyclables and billions of dollars worth of material feedstock lost to landfill despite the demand for high-quality recycled content from consumer packaged goods companies and brand owners."
AMP's AI makes secondary sortation technically and economically feasible. AMP's AI platform, AMP Neuron, recognizes 50 billion objects on an annual basis–a number that continues to increase as the company's install base expands. Through its secondary sortation model, AMP recovers mixed paper, metals, and a portfolio of #1 to #7 plastics in a variety of form factors and attributes with ideal precision and purity with a special focus on plastic blends uniquely enabled by AI. The company resells these commodities, including bespoke chemical and polymer blends needed by processors and manufacturers, to end-market buyers. AMP is continuing to update its AI capabilities to identify and recover film and flexible packaging, which create operational challenges for MRFs and historically have been complicated to recover and expensive to reprocess into raw materials.
AMP's secondary facilities drive down the cost of recovery while creating contamination-free bales of recycled material for resale. AMP's business model also introduces market certainty, lower disposal costs, and new revenue streams for established MRFs by creating a destination for residue that they would otherwise have to pay to landfill, as well as demand for mixed or impure plastic streams that may not have strong end markets.
"We've had AMP's AI-guided robotics systems installed since 2019, and they've helped us lower labour costs, increase recovery, and boost capacity," said Joe Benedetto, president at RDS of Virginia. "Now that we're working with AMP on residue, mixed plastics, and containers for secondary processing, we're seeing lower disposal costs and a new source of income. Moreover, we're better fulfilling our commitment to ensuring more recyclables are actually recycled."
AMP plans to introduce additional facilities in the second half of 2022. The company is seeking relationships with waste management companies to accept or buy residual or secondary materials as well as strategic partnerships with plastics reclaimers, chemical recyclers, and other plastics manufacturers for the offtake of recovered plastics.
The launch of AMP's newest secondary sortation facilities comes amid the ongoing expansion of the company's AI-enabled robotics system business. AMP has approximately 230 deployments of its AMP Cortex robotic sorting systems in upwards of 80 facilities across three continents and has doubled year-over-year revenue for three consecutive years. Demand for robotics to retrofit existing recycling infrastructure continues to grow; the industry needs capacity to meet the 2025 goals of CPG (consumer packaged goods) companies that have committed to the use of PCR (post-consumer recycled) content.
In addition to secondary sortation, AMP's AI enables AMP Clarity, the company's material characterization and robot performance software solution. The company is introducing new features including mass estimation; robot pick assignments, alerts, and status tracking; and expanded reporting capabilities to help MRFs and converters take a data-driven approach to optimizing operations, increasing recovery revenue, and reducing costs.
"Data is at the heart of what we do. Our AI platform, AMP Neuron, continues to achieve breakthroughs in data accuracy and classification of different polymers, form factors, and other packaging types. Our neural network is built on a data engine that has recognized more than 50 billion containers and packaging types in real-world conditions," said Amanda Marrs, senior director of product at AMP Robotics. "These advancements in material recognition continuously improve performance for our customers and open the door to other categories of packaging that have been historically challenging to identify, such as plastic films and flexible packaging–an area we're heavily focused on in new product development."
Data is seen as key to improving recycling and recovery rates for a circular economy. As part of the National Recycling Strategy released last year, the U.S. Environmental Protection Agency cited measurement standardization and increased data collection as one of its five objectives.