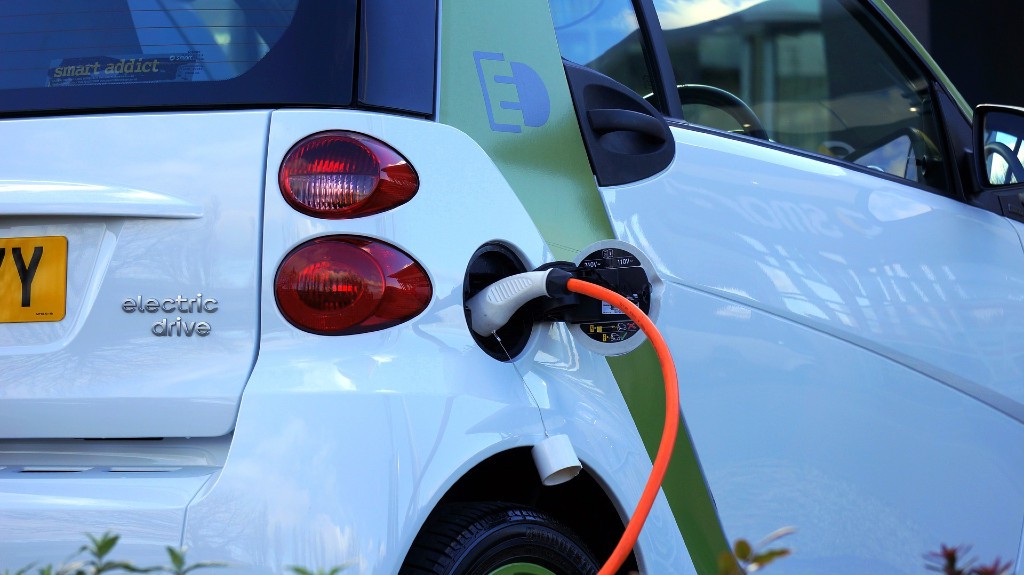
Aqua Metals has recovered the company's first copper from lithium-ion battery black mass at the company's Tahoe-Reno location. The plating of the high-quality copper, which is selectively plated atom-by-atom, is another step in building out Aqua Metals' capabilities for recovering all the high-value materials in lithium-ion batteries. To date, the company has also produced high-purity lithium hydroxide from lithium-ion battery black mass and successfully lab-tested cobalt plating.
Copper, which currently trades at more than $10,000 a tonne, is an important raw material for manufacturing the copper foil for lithium-ion batteries. Plus, copper also has many other applications relevant to the new energy era. Electric vehicles can contain more than a mile of copper wires, using 4 to 16 times more copper than gasoline-powered vehicles. Other components of the green energy revolution, such as electric charging points, solar panels, wind turbines, and smart power grids, have heavy copper wire and cabling needs. As of 2021, the world consumed 30 million tonnes of copper per year, and by 2050 it is predicted to double to 60 million tonnes. Efficient and clean recycling methods for recovering copper from spent lithium-ion batteries are critical to meeting this global demand.
"To prove that our AquaRefining technology is the most sustainable and economical method, we are being very thorough in implementing a methodical step-by-step scaling approach as we verify each phase of the process," said Ben Taecker, Chief Operations and Engineering Officer of Aqua Metals. "We are very proud of the R&D teams' progress and are confident that we will remain on schedule for running a fully integrated pilot in the coming months."
Li AquaRefining recycles spent lithium-ion batteries in a clean, economical way that is fundamentally non-polluting by utilizing the renewable electron as the reagent instead of chemicals or high heat. The room-temperature process uses about 1/200th of the chemicals of a standard hydro process and does not generate the carbon footprint of a high heat approach. Li AquaRefining is a closed-loop process that recycles the chemicals it uses. Consequently, it has a fraction of the waste streams, estimated at approximately 99.5 percent less than the standard hydro process. Aqua Metals, which to date has been awarded 72 patents with 49 patents pending, is developing its Li AquaRefining process to license lithium-ion battery recyclers worldwide.
"What differentiates us from other metals recycling processes is that our technology produces high purity metals. Cathode materials can be produced from pure metals, and starting with high purity metals is the best approach to making cathode materials," said David Regan, vice president of commercial for Aqua Metals. "We believe our technology will provide our partners with the ability to recycle more economically and cleanly, and provide a superior business opportunity with the option of selling product back into the battery supply chain or selling high purity metals to the metals industry. We think our partners will find this flexibility a great asset for their business."
In addition to lithium and copper, Aqua Metals' R&D program is working to recycle the other critical elements of lithium-ion batteries such as cobalt, nickel, and manganese. Aqua Metals will continue to update the market when meaningful progress is made in the recycling process.