Bunting project demonstrates 15 percent aluminum recovery from dross
Testing concludes that a three-stage separation process most effectively recovers metal from the dross on Middle East project
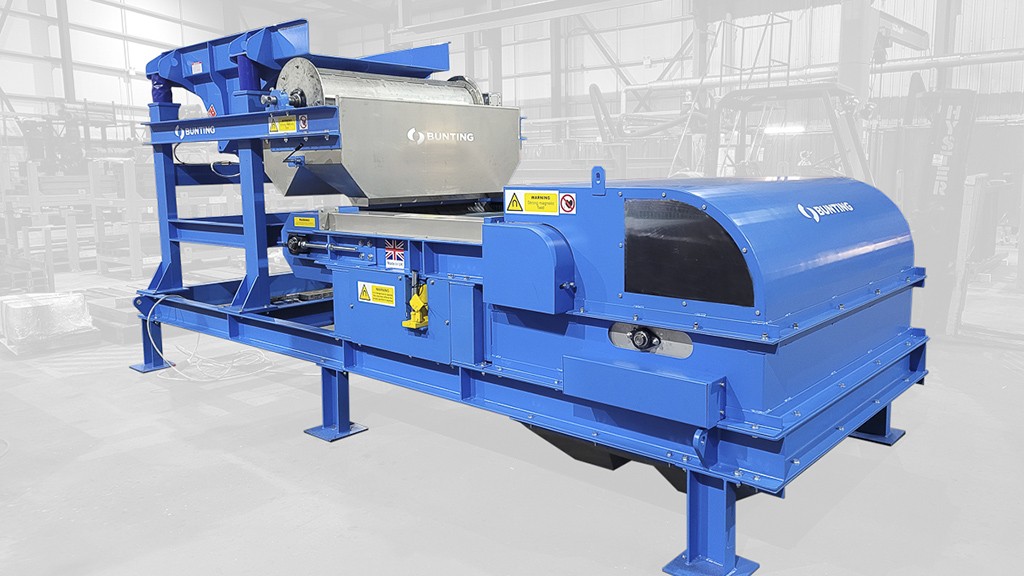
Aluminium dross is a byproduct of the aluminium smelting process. After crushing, mechanical separation enables the recovery of valuable, residual aluminium from the aluminium oxide.
An aluminium dross processing plant in the Middle East recently purchased an Eddy Current Separator, Drum Magnet and ElectroStatic Separator from Bunting Magnetics Co. The separation equipment, designed and built by Bunting at their Redditch manufacturing facility in the UK, is expected to help the facility recover a total of approximately 15 percent or more aluminum fines from their dross material.
Controlled Tests of Aluminium Dross Samples
The first stage of the new project in the Middle East involved Bunting conducting controlled material separation tests on three samples at their Customer Experience Centre in the UK. Each sample had different particle size ranges. The tests, undertaken on a range of laboratory-scale separators, confirmed the amount of aluminium that could be recovered by using three different types of equipment.
The tests concluded that a three-stage separation process most effectively recovered the metal from the dross. The first stage of separation focused on removing magnetic particles with a high-intensity Rare Earth Drum Magnet, which is beneficial to subsequent processing. Test results showed that magnetics accounted for approximately 1% recovery.
The Rare Earth Drum used has a stationary permanent magnetic element mounted within a rotating non-metallic shell. A vibratory feeder delivers an even and controlled flow of material onto the shell and into the magnetic field. Magnetic particles are attracted to the surface and deposited in a collection area underneath the drum. Non-magnetics flow in a normal trajectory and are recovered separately.
The second step of the process focused on separating small pearls of aluminium from the dross. An eccentric Eddy Current Separator recovered 14 percent aluminium from the dross.
The eccentric Eddy Current Separator has a high-strength magnetic rotor mounted in the top corner of a non-metallic shell. The rotor, with a series of alternating magnetic poles, spins at high speeds. According to Bunting, when aluminium enters the changing magnetic field, a current is induced into the particle. This creates a magnetic field, which is in opposition to the rotating magnetic field, forcing the particle to repel and enable separation from unaffected non-metallic material.
On the Middle East project, for finer sized fractions, remaining material was passed through an ElectroStatic Separator. Separation occurs by induced an electrostatic charge into a conductive dry-liberated particle such as aluminium. The ElectroStatic Separator recovered a further 6 percent of aluminium.
According to Bunting, their tests concluded that approximately, or more than, 15 percent of aluminum could be recovered from the dross using a combination of the three separators.
Production-Scale Separation Equipment
The production-scale equipment at the Middle East plant was sized to handle approximately 3 tonnes per hour of 1.5-20mm aluminium dross. The particle-size range of the feed would be controlled to maximize separation performance. In operation, the aluminium dross would feed onto a Vibratory Feeder, which would deliver a controlled flow of material onto a 1250mm wide 350mm diameter Rare Earth Drum Magnet. After extraction of the magnetics, the material passes onto a 1250mm wide Eddy Current Separator with adjustable splitter. The Vibratory Feeder, Drum Magnet and Eddy Current Separator are all mounted on one frame and operated through a single, separately located control cabinet.
The remaining material is fed, in designated finer particle size range fractions, through an ElectroStatic Separator. The 1000mm wide ElectroStatic Separator recovers fine aluminium unrecoverable on an Eddy Current Separator and features a control and adjustable splitter.
The importance of separation technology
"As with many of our projects, we worked closely with the customer to understand and then confirm the separation capabilities of our equipment," explained Adrian Coleman, General Manager of Bunting-Redditch. "The combination of established and new separation technology has maximized the level of aluminum recovery. The drive for most recycling companies is to recover as much clean metal as possible and with new technology, such as our ElectroStatic Separator, we are able to provide a complete separation solution."