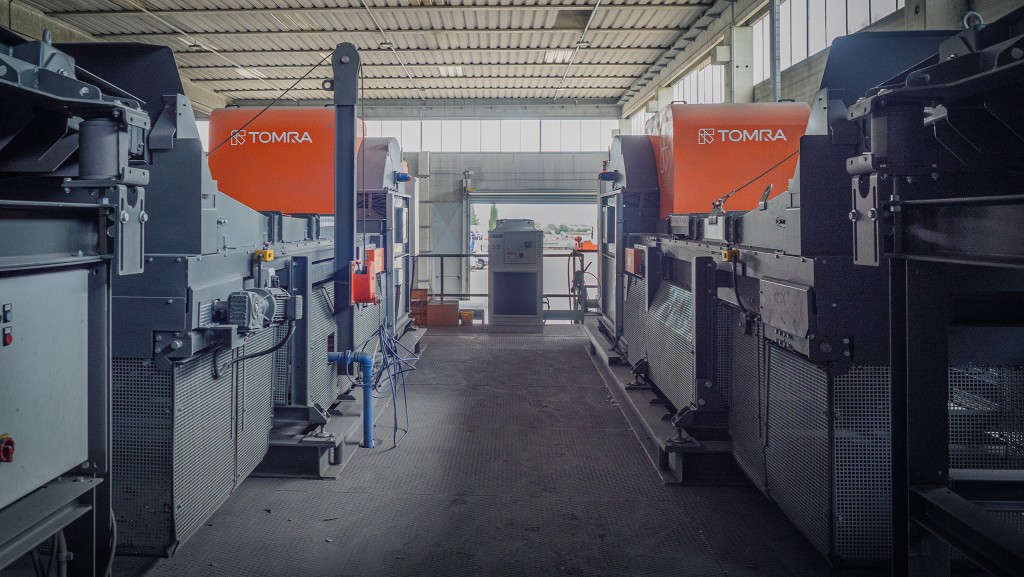
In the province of Latina, Italy, scrap recycler Centro Rottami supplies a nearby foundry with recycled aluminum that has been sorted by TOMRA's machines to produce a green billet with 85 percent recycled content. This is an outstanding example of how to create a quality finished product with lower energy consumption and less pollution.
Aluminum is a precious material, which when recycled maintains its surface characteristics. A 100 percent recyclable resource that can and must be enhanced, the recycled alloy offers a 95 percent savings of the energy that would be needed for the production of primary aluminum from bauxite - with consequent reduction of CO2 emissions.
Italy ranks first in Europe in the production of recycled aluminum with 70 percent recovery, far exceeding the objectives set by the European Union (50 percent by 2025).
Centro Rottami and Indinvest, a shining example of recycling from scrap into a new product
Founded in 1985, Centro Rottami of Cisterna di Latina, Itlaly, has been working with aluminum scrap for 10 years. Gennaro del Prete, technical director of the plant, says: "We started as a scrap iron shredder. Then five years ago we decided to specialize in aluminum refining. This specialization has been possible thanks to TOMRA's technologies."
The center processes about 1,500 tonnes (1,650 tons) of aluminum and 1,000 tonnes (1,100 tons) of ferrous scrap each month. The incoming aluminum comes mainly from old window profiles. They contain some contaminants such as plastics and rubber, as well as other metal materials like copper, brass, zinc and steel, all of which must be separated to produce pure aluminum fractions.
The company, which has been working with TOMRA for 12 years, currently has three TOMRA FINDER and three TOMRA X-TRACT sensor-based sorters. Once the incoming material is shredded and presorted by both magnets and eddy current seperators, the material follows two lines. The material dropped by the eddy current separator is processed by a FINDER unit, which recovers metals such as stainless steel. Advanced technologies such as SUPPIX and Z-TECT enable FINDER to detect metal objects with ultra-precision, delivering exceptional purity levels for greater salability.
Simultaneously, the three TOMRA X-TRACT units purify aluminum ejected by the eddy current separator. Thanks to advanced X-ray transmission technology, X-TRACT detects the remaining contaminants and sorts them by their respective atomic density. This way, shredded aluminum is freed from heavy metals, such as copper, brass and cast aluminum with outstanding precision and reliability, while using little energy and increasing production capacity.
Del Prete recalls, "In 2019, we purchased two more TOMRA X-TRACT units because the aluminum market demands ever-increasing quantities and quality standards. We then combined the three machines into a single line, subdividing the pieces to be screened in order to go into more detail and make the most of the quality of the aluminum recovered in the shredding process. This choice was also made to take advantage of synergies with Indinvest, the aluminum smelter neighboring the company."
Del Prete explains the collaboration with Indinvest: "Relying on a technology that gives a guarantee of a selected and pure aluminum is essential to establish a relationship of trust with foundries, to which it is of utmost importance to continuously realize high qualities . Thanks to TOMRA, we have achieved the highest possible quality: alloy material and zinc and copper meet the requirements for the production of the profiles."
From post-consumer scrap to green billet at Indinvest
Indinvest LT is an important company in production and extrusion of aluminum profiles, used in the sector. The company, located next to Centro Rottami, has its own integrated billet foundry with a production capacity of 60,000 tonnes (66,140 tons) per year and five extrusion lines with a total capacity of 60,000 tonnes (66,140 tons) per year of extruded profiles.
Ezio Porreca, Casthouse manager for Indinvest LT, says: "For about five years, Indinvest has been buying post consumer scrap from Centro Rottami. Thanks to the use of the TOMRA X-TRACT machines by Centro Rottami, we have been able to significantly increase the use of post-consumer material in the melting furnaces from about 20 percent to approximately 40 to 50 percent. This has not only allowed us to reduce the use of primary material, but also to realize energy and gas savings of 5 percent, which on our volumes is significant."
Indinvest LT targets to produce alloys that meet certain specifications. They have developed their own melt recipes to create these alloys by relying on a mixture of three materials: primary aluminium, internal post-production scrap and the post-consumer scrap supplied by Centro Rottami. By making the mix, the reference alloy for the production of the billets is obtained. The higher the quality of the scrap, the less raw material used.
Porreca continues, "By using cleaner recycled aluminum, production has increased significantly. If not properly cleaned, recycled aluminum can still contain some contaminants such as paint, plastic and other material, which, in turn, form slag in the furnace. By using the clean material from TOMRA, we have fewer pollutants and can clean the furnace less. Cleaning the furnace involves opening the door and dropping the temperature from 1,100 degrees to 800 to 900 degrees. And getting it back to 1,100 degrees takes time, gas and electricity."
Roberto Antichi, President of Indinvest LT, says: "For us, the concept of collaboration is very important when following a joint goal. We started this project together, are using synergies, and can clearly see that it has paid off."
It's a collaboration that has led to the production of excellent and greener aluminum product. "Two years ago, we created a billet called Creal, containing 85 percent post-consumer aluminum with mechanical and, above all, surface results comparable to those of primary aluminum created by aluminum manufacturers from bauxite," Antichi says.
Indinvest was able to achieve this incredible result thanks to the selection of TOMRA machines. Otherwise, according to company representatives, the recycled aluminum content could have been as low as 35-40 percent.
Antichi continues: "Recent years have shown us that our recycled aluminum is well received by the market and is increasingly asked for. Especially now, with the 2030 Paris Treaty mandating a reduction in CO2 consumption, all customers are pushing the production of profiles with recycled material."
Aluminium: a growing market
Concludes del Prete: "One of the few positive notes of recent years is the growing trend in the aluminum sector. Thanks to the immense availability of recycled material and thanks to its mechanical properties (flexible, resistant, etc.) it will be the material of the future together with wood and glass. That's why we are focusing on recycled aluminum. Many companies approach us because they know the technologies we use, and they know they can count on a recycled product of absolute quality. We already resell our aluminum to companies working in the most important sectors that use this material - automotive and construction. But in the future we reserve the right to explore the rest of the market as well. We have the best team and equipment!"
Company info
Strada Prov.le Ninfina Ila, km 1,200
Cisterna di Latina,
IT, 04012
Website:
indinvest.it/en