BCA "Beast" shredder quickly processes high-volume metals, e-waste and tires
ES2000 shredder design addresses vulnerabilities of conventional shredders with cluster drive system using eight small hydraulic motors
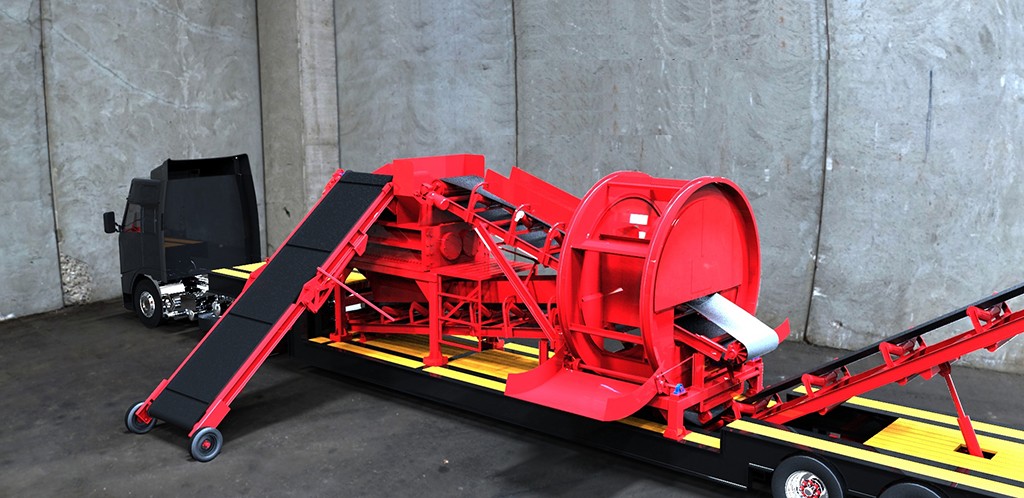
High-volume reduction of oversized metal feedstock and other materials has long frustrated recyclers because it can slow and even cripple production when shredding equipment breaks down. BCA Industries' latest generation of advanced shredding technology includes a massive machine called "The Beast," specifically designed to help recyclers reliably shred even the toughest scrap metal to chips at high volumes, using unique advances in hydraulic systems.
The Beast custom shredder from BCA
The customizable ES2000 shredder, called "The Beast" is designed to process ferrous/nonferrous metals, electronic waste, truck tires etc. in both stationary and portable units. With 24" diameter hard-faced knives using a base AR-500 alloy, 55" to 72" x 44" cutting chambers, and 8" 4130 Chromoly steel shafts, the unit can quickly reduce even the largest metal scrap.
With 24,000-38,000 lbs. total gross weight (not including power supply), it is designed to shred 15-35 tons of metals or dense materials an hour with 179,000 foot-pounds of torque per knife. When even more throughput is required, it can be rated up to 800HP, and utilize dual cutting chambers. To maximize high-torque throughput and efficiency, it utilizes a pressure compensated variable displacement pump that allows the RPM to increase and decrease based on load.
According to BCA, their Beast design addresses the vulnerabilities of conventional shredders by utilizing inexpensive cluster drive system of eight small hydraulic motors which create redundancy in the power supply that eliminates much of the possible downtime. These cluster drive motors are off-the-shelf, and readily accessible, and they minimize cost while increasing reliability. Use of the cluster drives ensures continuous operability (at slightly lower output), even if one or more need to be replaced.
In addition, instead of 7-inch shafts, the Beast uses 8-inch chromoly shafts increase usable life, and in place of old HEX shaft design or a double key round shaft, the unit uses a 6 key design where the knife literally rides on disposable keys, not directly on the shaft. With the keys taking any abuse instead of the shaft, the design eliminates shaft washout and simplifies knife changes. And because the unit is designed with a double labyrinth style drop zone and outboard bearings, this eliminates any direct path to the shaft bearings. It also allows compressed material a path to exit the shredder, eliminating the "catastrophic costs" of bearing and shaft replacement.
Terry Frank of Ellwood City, PA says, "As production and maintenance supervisor of the largest US industrial battery recycler, I recommended "The Beast" (ES2000 shredder) to ownership based on both the cluster drive and variable displacement hydraulic design. The other single speed shredders we worked with over the years were far too slow for our needs. The machine BCA delivered has far exceeded our throughput expectations, doing 4 times the tonnage and near double the knife life of our other equipment. The downtime has been a small fraction of what we had gotten used to as well."
To further enhance production, BCA says innovative shredders like this strike at the root of the processing bottleneck. Instead of using many shredders to progressively reduce the size of scrap, new shredder "knife" technology like BCA's patented Triplus system (when used in the shredder) can uniformly cut to any size in a single pass without a screen, very quickly reducing scrap to a reclaimable proportion. It utilizes a unique bed knife design in a dual shaft shredder to cut the width of the material of the shredder. The size of the end-product is based on the size and geometry of the rotary and fixed knives as well as their gap distances.
A shredder using this design can produce over 85% correctly sized material in one pass with less than 10% oversized material, according to Neuens. He notes that the knife system can reduce scrap to the appropriate size with much less energy than typical shearing and grinding equipment. Power efficiency approaches 150% over any standard shredder.
When the knife technology is used with ferrous/nonferrous metals, electronic waste, tires, ragger tail, C and D waste, MSW, as well as paper and plastics, it can dramatically reduce shipping costs by minimizing voids in containers due to oversized material.
While such units are typically hydraulic, all-electric versions are an attractive option if a very large chamber size is required, but not high-torque (i.e.-mild steel). All-electric versions are simpler, quieter, less costly, and even easier to maintain since the devices have no valves and cannot leak hydraulic fluid since none is used, according to Neuens.
With the Beast shredder's programmed "nip cutting" function, customers can save labor during the processing of materials such as bales, compressed copper wire or aluminum when shredding the entire amount in one stream is not possible. Nip cutting (rotating shafts to cut big hunks into small pieces) saves the operator time trying to disassemble, reduce bale size, or cut the material to size.
Moving beyond conventional shredder limitations
According to BCA Industries, for truly high-volume recycling operations, the size of the shredder can restrict production flow if it is not large enough to accept oversized metal scrap and materials. Hydraulic shredders operating at a single RPM, using a single rotary piston or gear pump, also never maximize throughput regardless of load.
The lack of robust construction, designed for reducing tough materials at high-volume, inevitably leads to breakdowns and unscheduled downtime for repair and replacement.
"Typically, shredder companies use 4140 knives, traditional hard face welding or even tool steel for their systems, but inferior knives increase recyclers' top maintenance cost - knife rebuilds," says John Neuens, Sales Director at BCA Industries.
Neuens outlines a host of other shredder design vulnerabilities that can lead to "catastrophic failures," if not addressed.
Expensive shaft washout, due to undersized material along with poor shaft or clamping nut design, as well as old-style hex shafts, can allow stack loosening during operation.
Bearing failure, caused by contamination, often occurs when bearing seals and shaft armor insufficiently protect against shredding chamber compression forces.
Perhaps the most consequential point of failure can occur when shredder manufacturers build hydraulic power supplies using a single but very expensive hydraulic pump or motor, which can cost up to $90,000 to replace with lead times of 12+ weeks, resulting in excessive downtime.
Company info
4330 W. Green Tree Rd.
Milwaukee, WI
US, 53223
Website:
bca-industries.com
Phone number:
414-353-1002