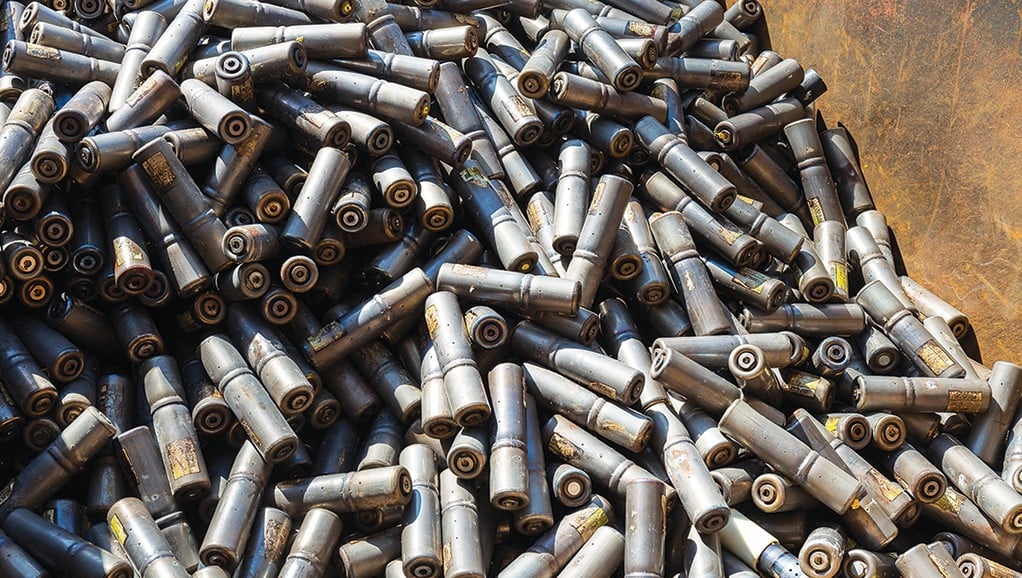
New categories of consumer and industrial products that need to be diverted from landfill, but which do not have a long history of infrastructure and best practices in place for their end-of-life management, are coming at us with increasing pace. One of these end-of-life products is the automobile safety airbag, with modern cars using upward of a dozen per vehicle. These airbags are not just plastic balloons embedded in a vehicle. They use an inflator component made of valuable metals, including heavy melt steel and copper wires, and contain an explosive chemical propellant used to deploy the airbag. Between the two largest sources of vehicle airbags for recycling - OEM recalls and end-of-life vehicles (ELVs) - there are growing stockpiles of this hazardous, but valuable, recyclable material stream in North America and around the world.
Toronto-based Lacero Solutions Inc. began to recover vehicle airbags in 2018 in response to an opportunity. According to Keshav Kochhar, CEO and co-founder of Lacero Solutions, the initial interest came from companies looking to find a way to safely manage a growing stream of recalled airbags. It began with one of the largest-ever auto industry recalls, in 2017, by former airbag manufacturer Takata Corporation.
"There wasn't any clear solution on how to handle these airbags," explains Kochhar. "Your traditional scrap metal recyclers refused to take them, as they can explode violently if mishandled."
He says it did not make sense for scrap recyclers to put their million-dollar shredders or other equipment and people in jeopardy to recover $1 worth of metal. "OEMs, auto repair shops and recyclers were simply stockpiling the recalled Takata airbags, or they were ending up in landfill, because there was no clear, set solution in place."
One of Lacero's early customers had approximately 225,000 defective airbags sitting in Calgary, Montreal and Toronto. They had no solution for recycling them and while some were going across the border, Kochhar says strict regulations and the classifications around airbags as a hazardous waste and Class 9 dangerous good means it is not easy to move them internationally.
"Obviously the logistics adds up as well, so OEMs were trying to find a local solution," Kochhar continues. "We started looking at this problem and we saw the opportunity. We became a middleman between auto industry OEMs and the scrap metal recyclers."
Traceability and an unseen hazard
An end-of-life airbag is categorized as Class 9 dangerous good and hazardous waste in Canada because of the chemical propellant contained in the airbag inflator component. Attached to the outside of the inflator is the plastic bag that inflates upon vehicle impact, and which is the essential component in preventing injury. The main component of an airbag, from a recycling point of view, however, where both the value and the hazard are found, is the airbag inflator. Made of a metal casing, the airbag inflator contains explosive chemical propellant, most commonly sodium iodide or ammonium nitrate.
"The airbag inflator is a metal container with tiny holes in it," explains Kochhar. "What happens is that when a car is involved in an accident or slows down suddenly, it sends a signal to the propellant in the airbag inflator, which is ignited using an electric match. It produces a small, contained reaction and burns the chemical inside the inflator, creating hot gas which then exits from the tiny holes, filling and deploying the airbag.
"We now have a cost-efficient, proprietary process to deploy and deactivate these airbags in a safe manner, changing their status from a hazardous waste to an inert, very valuable recyclable material, and it avoids the need for disposing of the propellant chemicals in the airbag. We make sure all the chemical inside that airbag is extinguished, and we are then left with just an empty metal container." Kochhar also notes that for most of the chemicals, especially within the defective airbags that have been recalled, their chemical structure changed over time due to heat and humidity, which the airbag manufacturer did not take into account.
"We work with OEMs and help them realize that there's value for them to just take the inflator out," he says. "The whole airbag is not defective, it is just the inflator that is defective. That's the dangerous part, and the part which has the highest value materials for recycling.
"The other service that we offer to our clients, which sets us apart, and which attracts OEMs to come to us, is that we give them full traceability. OEMs don't want defective airbags to enter the market. We designed our own in-house software which allows OEMs to track every airbag from the time it leaves their warehouse, to when it's fully destroyed and recovered. We've also recently developed a phone application, for Android, iPhone and PC, where customers can track every shipment on every airbag.
"What this does is it gives OEMs full accountability on every airbag we receive," he continues. "We also issue destruction certificates for compliance departments, which proves the dangerous chemicals are destroyed, making the airbag an inert material for recycling."
A main reason for the traceability requirement is to avoid end-of-life airbags entering the gray market. This unregulated market is where defective airbags can be sold to foreign buyers, or domestic used auto repair shops who do not follow the rules, and reused as an airbag replacement, even though the product is defective and potentially very dangerous to the new owners.
Kochhar says a lot of people have died or been injured by defective airbags. If the explosion happens in a car when it is not supposed to, or happens without properly deploying the airbag, it's like a small metal bomb exploding - metal shrapnel and extremely hot air can fly directly into the face of a driver or passenger.
"With our process, we are as transparent as possible and there are a lot of external parties involved. It's not just us, it is our downstream recycling partners, OEMs, Automotive Recyclers of Canada (ARC), Recycling Council of Ontario, the Ministry of Environment and other ministry organizations. There are a lot of people monitoring the situation, because they know that if these airbags end up in the wrong hands, they can do a lot of damage."
For auto recyclers, Lacero strongly encourages the removal of all airbags from ELVs prior to the shredder. If they are not separated from ELVs, they can end up going through the process and explode, or go through untouched and unnoticed and end up in landfill or at a downstream recycler while still containing a live, explosive chemical. Kochhar says savvy recyclers simply remove airbags and stockpile them because they don't want to risk shredders or personnel. Kochhar also notes that for ELVs, most of the airbags are non-defective working components and are unlikely to damage shredders or injure anyone. But still, there have been bad experiences in the scrap recycling industry. Airbag inflators should be separated from ELVs prior to the shredder, and the airbag inflator component should be sent to a qualified recycler such as Lacero for safe recovery.
The Lacero airbag recovery solution
With respect to volumes processed, Lacero's total airbags recovered since starting operations is approaching 300,000. Pre-COVID, they were processing about 40,000 airbags monthly. Over the last year, this number has been more like 20,000 per month. Kochhar says airbags being shipped to Lacero for recycling must be properly packaged and transported as per transportation guidelines for dangerous goods.
"We receive airbags at our site, usually on wooden skids or in cardboard boxes, all of which is also sent downstream for recycling," he explains. "In our preparation stage, each airbag will first get scanned and tested, wires are taken out, and the plastic airbags themselves are detached, so that the airbag inflator is ready to be treated."
Lacero Solutions uses specialized, custom machines with highly trained operators to safely deactivate airbag inflators. The machines ensure the chemical is fully extinguished, leaving only an inert metal container. Once that is done, Kochhar says they have additional QC checks and processes, visual checks and tests, before the inflators are ready for recycling.
"We change its classification from a hazardous waste to a metal bearing waste, which is just any empty container," says Kochhar. He says their operators confirm the airbag has been deactivated, and then the metal inflator casings are allowed to cool down in the machine, because when the chemicals in the airbags are treated, they reach a temperature anywhere from 350 to 800 degrees.
"One thing I'm proud of is that even after we've dealt with approximately 280,000 airbags since we started, we've had zero injuries to date. Not even a single paper cut."
He says Lacero's operations can also boast no waste generated, no wastewater discharge and zero emissions, outside of the emissions which come out of the airbag when it is deployed, in the form of the gas produced.
Downstream recyclers and evolving industry regulations
Lacero has established solid, dependable downstream recycling partners for their metals and plastics, as well as wood and cardboard packaging produced from their process. Their cardboard packaging is currently picked up on a contract with GFL Environmental, and one of their most established partners for the recycling of metals produced from their process is Toronto-based Ram Iron & Metal.
"Scrap metal recyclers love it when we send our recovered material to them," says Kochhar. "We certify it to be inert, and we take full responsibility. If it damages their machine, we take responsibility. So, we have to make sure that our QA/QC procedures are in place, that we can make sure every airbag leaving our site has been deactivated before we send it."
He says the deactivated airbag inflator, an inert metal cylinder, is classified as heavy melt steel and is valuable. "Our heavy melt metal garners three to four times the price of regular scrap metal," he says, adding that the second highest valuable material recovered by Lacero is copper, from the airbag inflator wires.
With approximately 280,000 airbags recycled since 2018, Lacero has recovered 670,000 pounds of recoverable materials. Kochhar notes that there are large differences in how much they recover by weight, depending on the type of airbag. A driver's side inflator weighs roughly 500 to 550 grams, and out of each inflator, there is about 25 grams in copper material and wires, as well as 55 grams in plastic connectors. The rest of it is about 450 to 500 grams of high-quality scrap heavy melt steel. Passenger-side airbags are much bigger, weighing roughly 1,300 to 1,500 grams.
Besides airbags, Lacero is also in the business of recovering auto seat belt tensioners.
"We just got into this about nine months ago," says Kochhar. "Seat belt tensioners work on a very similar mechanism to how airbags work. They receive a small electrical signal when an accident occurs, which locks the seat belt in place. Sometimes we have recalled seat belt tensioners, which need to get disposed of in a safe manner as well. Seat belt tensioners have a lot of metal components, about 70 or 80 percent metal, and some plastic.
"Ram Iron & Metal visits us regularly and takes all our inert metal inflators and seat belt tensioners, and we have been doing that since about three months after our plant started operating."
The future for Lacero Solutions
"We want to be the industry leaders in the safe recovery of airbags and seat belt tensioners, with proper deactivation and recycling, and to keep our process as transparent as possible," says Kochhar. "We want OEMs to be comfortable sending their airbags or seat belt tensioners to us, or any manufacturing scrap waste, for safe disposal. At Lacero, we have the right expertise and group of people on staff to safely and cost-effectively recover defective airbags."
Another key objective currently for Lacero Solutions is to educate OEMs, government and the entire recycling industry about the need for proper regulation and recovery of airbags. He says that they have found a way to profitably handle a very specific type of hazardous waste - and they want to spread the word. Most recently, Lacero launched their new website at www.lacerosolutions.com. In the next few years, plans are to set up another facility in the U.S. based on the significant amount of volume there, and they are already getting interest.
"We want to become the hazardous waste or dangerous goods management solution for these companies with defective or otherwise end-of-life airbags and seat belt tensioners that no other recycler wants to take. We have the expertise, and we can do something that no one else wants to do."
"Airbags should not be treated as waste," concludes Kochhar. "They are hazardous and have to be dealt with properly, and they contain very valuable metal and other materials. We want government officials, OEMs and recyclers to know this. We want to create awareness and push for stronger regulations around airbag recycling.
"Currently, for the most part, we are treating something as waste which has a lot of valuable materials in it. We have now proved that airbag inflators can be recycled safely and profitably."
This story was originally published in the May/June 2021 edition of Recycling Product News, Volume 29, Number 4.
Company info
2351 Royal Windsor Dr,
Mississauga, ON
CA, L5J 4S7
Website:
lacerosolutions.com
Phone number:
905-824-5836