How to choose the best high-speed wood waste grinder for your recycling operation
Consider factors such as the type and volume of materials, machine safety, cost of operation, and ease of maintenance
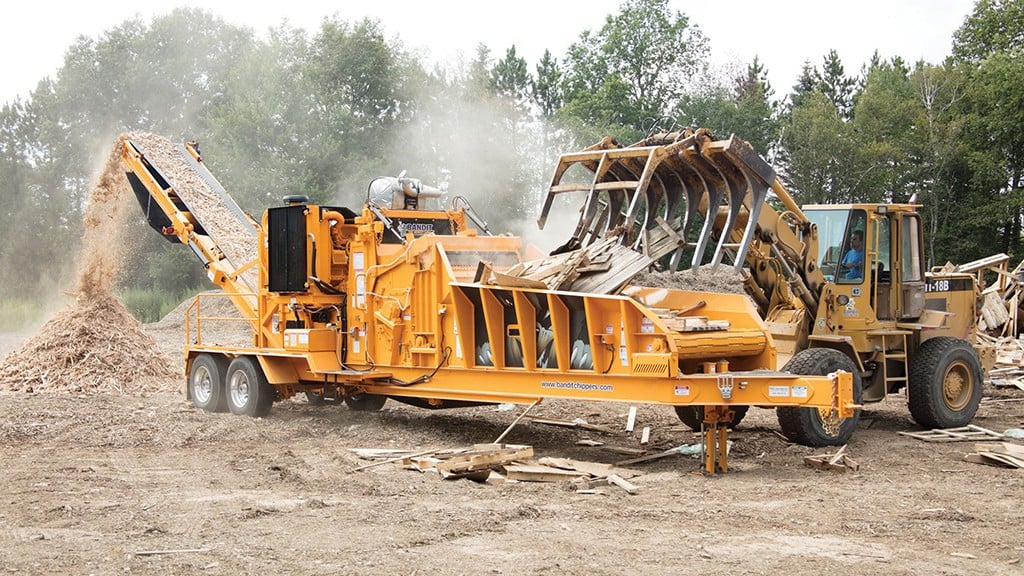
Key factors to consider when choosing a wood waste grinder
Wood waste recycling options are diverse, offering recyclers flexibility in organic material recovery. Slow-speed, high-torque shredders work well in lower volume applications with variable infeed, while disk or drum chippers excel in processing clean, round wood. For most large-scale wood waste recycling and composting operations, the high-speed wood waste grinder takes centre stage, available in horizontal or tub configurations.
Overall, the wood waste grinding industry has become more sophisticated over the last decade - for the most part, organics recyclers no longer make decisions based purely on engine horsepower or mill opening size. Organics recyclers now navigate a landscape with multiple end-market opportunities and tight profit margins. Modern operations prioritize tracking fuel and wear part consumption against throughput, with many investing in asset protection plans.
Adapting to an evolving recycling market, today's high-speed grinders handle a broad spectrum of materials, from wet and stringy wood to hardwood, stumps, asphalt shingles, corn, hay, C&D wood, plastic, and food waste. These versatile machines feature fast-changing screens, teeth, knives, and drums, facilitating the production of various products with a single machine. Integrated metal sorting systems enhance efficiency, allowing for the simultaneous grinding and colouring of landscape mulch, and are available with a huge range of options designed to enable recyclers to customize their grinder to their operational needs.
Before investing in a wood waste grinder, recyclers should consider material types and volumes, machine safety, operational costs, maintenance ease, reliability, desired end-product size, production rates, and market demand. Thorough research into suppliers and machines sets the foundation for a worthwhile investment. Below are some major factors to consider when adding a grinder to an organics recycling operation.
What is the difference between horizontal grinders and tub grinders?
The main difference between horizontal grinders (HOG) and tub grinders is that horizontal grinders generally use a chain-based feed roller and a moving floor to feed the hammermill, which is more complicated to maintain but provides more consistent feed, especially for longer materials such as whole trees. On the other hand, a tub grinder relies on gravity and a rotating, conical top-feed tub to feed the hammermill. Both types of grinders can handle most materials they encounter, but in general, horizontal grinders will handle longer materials more easily when compared to a tub, while a tub grinder can provide more productivity for large materials such as stumps and pallets. Some horizontal grinders are also available with an angled cuttermill for improved gravity-driven infeed.
Horizontal grinders generally require less product sizing compared to tubs. Despite this, many prefer tub grinders for wood waste grinding due to their effectiveness in volume reduction and mulch production. Tubs "smash" wood, generating fewer splinters than horizontals, which tend to "rip" material apart. Tub grinders, being slightly less complex, are highly productive and easier to work on and maintain.
Regarding safety, tubs have had a historical reputation as being less safe due to their exposed grinding mechanism, posing a risk of hazardous material being thrown. Modern tubs (and some horizontals) address this concern with options like tub covers and full enclosures to prevent such incidents.
Ultimately, productivity and safety rely on operators. Keeping a tub grinder consistently full reduces the risk of dangerous flying material, as the material on top acts as a barrier, preventing material from the bottom of the tub, near the hammermill, from becoming a hazard.
Electric grinders for emissions-free wood waste processing
The advancements in Tier 4 technology have significantly enhanced fuel efficiency in diesel-powered grinding equipment. However, the notable difference lies in electric grinders, which generate no greenhouse gases (GHGs) and generally provide a lower cost per ton (or cubic yard) for the finished product compared to their diesel counterparts.
Electric grinders are particularly well-suited for stationary applications where three-phase power is readily available. Moreover, they offer versatility with mobility packages, including trailer mounts and electrical connections, making them suitable for expansive sites and multiple locations. This adaptability ensures that electric grinders are a compelling choice for those seeking both environmental sustainability and cost-effectiveness in their grinding operations.
Match the machine to the task at hand
Determining the hourly material processing capacity is a critical consideration in choosing grinding equipment. The throughput per hour directly influences the processing speed of the entire line. Recyclers must assess current grinding volumes and anticipate future potential volumes. A general rule of thumb is that higher volumes necessitate higher speeds.
Considering the location of grinder usage is crucial. If noise is an issue and volume requirements are low, opting for a lower-speed, high-torque, single-shaft shredder running at speeds ranging from 90 to 300 rpm may be more suitable. Higher speeds typically result in a noisier machine.
Selecting a grinder that integrates seamlessly with existing equipment and setup is the best choice. Oversizing a grinder to accommodate "fringe" materials increases the cost per ton or cubic yard produced. Operating an empty grinder with the engine or motor running means you're essentially grinding air.
Metal separation requirements are another vital consideration. Removing nails and other scrap metal from wood residue is essential for the marketability of the end product, especially in construction and demolition (C&D) and asphalt recycling applications. The level of separation needed is determined by the specifications of the fiber buyer or the end use of the processed material. Cross-belt magnetic separators are commonly employed, and two-stage metal separation with a magnetic pulley head is ideal for applications prioritizing very high purity, such as composting and fiber-to-animal-bedding. Knowing what percentage of separation you need will determine what kind of extraction system you need in your grinder.
What are the costs associated with wood waste grinders?
There are three major cost components to wood waste grinding: power, labour, and ongoing operating costs. Diesel machines tend to be more expensive to run than electric, but they are usually self-contained and portable, making them a good choice for mobile applications. For energy costs overall, electric-powered machines will cost less to run and require less downtime for routine maintenance. It should also be noted that if high volume is not a main consideration, the operating cost for low-speed technology, such as a shredder, is typically lower than a high-speed grinder.
When it comes to labour costs, they vary greatly from one region to another. Many grinders offer the flexibility to be batch-fed or integrated in line with conveyors and other material handling equipment. A grinder designed only to be fed in batches can result in more labour costs than one that can be dump-fed or fed automatically by a conveyor.
Outside of energy, operating costs for high-speed grinders come down to the reliability of the machine and the routine and preventive maintenance plans that are in place. Productivity can be as high, but excess downtime will quickly eat away at profitability gains. This is where the right maintenance regimen and solid dealer support with quick parts availability become key.
Other uses for wood waste and organic materials
Markets for wood fiber, recycled asphalt shingles (RAS), and other products that can be produced with the right grinder continue to grow and change, and the movement toward a circular economy will continue to push this trend. There are solid and developing markets for coloured mulch, natural mulch, biofuel, refuse-derived fuel, fuel pellets, compost, animal bedding, and other engineered fibers, as well as hot mix asphalt supplement - all of which can be made with the right grinder.
Today's grinders are available with a wide range of options to accommodate flexibility, including track-mounted and mobile models, integrated mulch colouring capability, metal separation, as well as quick-change drums, grinder teeth, and screens designed to equip one machine for multiple applications and varying end products. For example, easy change-out chip drums for horizontal grinders are now available from some manufacturers, which enable operators to quickly and easily switch from turning wood waste to mulch to making a uniform-sized wood chip preferred over standard grindings by wood-fuelled waste-to-energy plants and pellet mills.
Other options that can be integrated into grinders include a secondary hammermill for very fine particle sizing applications; customized infeed and outfeed set-ups, including conveyor belts, vibrating conveyors, and metal separation; and high-abrasion packages for processing tough materials like asphalt shingles, C&D, and yard waste. In addition, the modern grinder includes sophisticated, intelligent machine control and monitoring systems, remote capabilities, as well as feed controls, and infeed protection systems that automatically stop the machine before metal and other contaminants contact the hammermill, preventing catastrophic damage.
Choosing the right equipment dealer
Today's grinders can produce several hundreds of tons per hour of saleable material if all the parameters are just right. But when downtime occurs, production and profitability gains can be lost very quickly. Manufacturers will tell you that regular maintenance and consistent production are key to maintaining the highest long-term output, including a lower cost-per-tonne or cubic yard.
Most manufacturers in the industry will also tell you that support is the number one factor you want to consider before purchasing a grinder. Parts and service can make or break a recycling business, so this has to be an initial consideration. For grinder owners and operators, parts should be available locally, or if not, should be able to be shipped directly to the customer in one day.
Research your supplier, and once you've decided, take advantage of the relationship on an ongoing basis. Today's major manufacturers of horizontal and tub grinders for wood waste recycling are experts who can offer help determining what size and type of grinder will fit for an operation or application. They can also help in finding end markets for products produced, optimizing a machine's operation over its entire life, and obtaining financing options for an equipment purchase.
For recyclers looking to purchase a grinder, especially if they don't have a solid, positive experience with a given supplier to work from, good market research is paramount. Ask a lot of questions, and ask to talk to current customers. It is the right supplier, over the long run, that will make the greatest amount of difference to your bottom line, with respect to lower downtime and lower overall cost of operation per tonne produced.
This article was originally published in the April 2021 edition of Recycling Product News, Volume 29, Number 1. It was updated on December 14, 2023.
Company info
P.O. Box 5288
665 Murlark Ave. NW
Salem, OR
US, 97304
Website:
westsalem.com
Phone number:
800-722-3530