Getting the lead out at Terrapure with lead-acid battery recycling
For an award-winning, diversified innovator like Terrapure Environmental, closed-loop lead–acid battery recycling is just one of many success stories
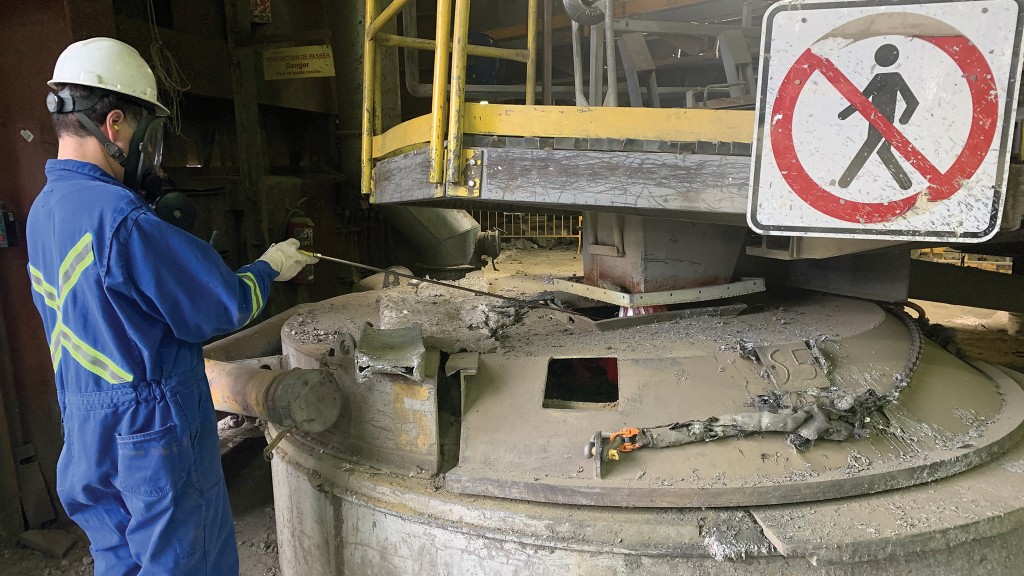
Between two dedicated recovery and recycling operations, one in Ontario and one in Quebec, Terrapure Environmental processes about 225,000 metric tonnes (500 million pounds) of lead-acid batteries yearly, of which about 75 percent are automotive. According to Ross Atkinson, senior VP, lead recycling, and an employee for over two decades, "Our volumes are massive. We process about 8 million units per year or about 12,000 full transport trucks of lead-acid batteries," which he says are currently worth approximately $20,000 per truckload.
Outside of automotive batteries, about 10 to 15 percent of their incoming volume is forklift lead-acid batteries, which are used in part for counterweights on those machines and are very large and heavy. "They're huge 2,000-pound batteries, whereas an auto battery is 35 to 40 pounds."
Terrapure also takes in a wide range of smaller batteries, such as backup power batteries used for institutions and commercial facilities such as banks, and for remote power, as well as smaller consumer non-lead alkaline and lithium-ion batteries. (Which get mixed into their incoming streams and which they do not recycle, but sort and send to specialized recyclers.)
Lead-acid battery recycling is only one of Terrapure Environmental's core competencies. Born out of what was once the industrial division of Calgary-based Newalta, the energy industry waste and environmental services specialist since merged into Tervita, Terrapure now has over 2,000 employees - doubled from when it started in 2015. The company operates about 70 locations across Canada, with headquarters in Burlington, Ontario, and regional offices in Quebec, Nova Scotia, B.C. and Alberta.
"We've certainly had some good organic growth, and have grown a lot through acquisition," explains Greg Jones, managing director, communications & public affairs for Terrapure. He says in basic terms that their business is focused around helping industrial customers minimize waste and realize the full potential for recovery of value from their waste, and is separated into two main divisions.
The first is environmental solutions, which consists of industrial waste management, including both wastewater and solid waste collection, transportation and disposal, as well as industrial site remediation and cleaning services, dredging, dewatering, chemical and tank cleaning, and hazardous waste management. The second side of Terrapure's business is in resource recovery and recycling, with a focus on organics and biosolids, used oil and lead-acid batteries.
Out of their 70 locations, they operate only one landfill which is in Stoney Creek, Ontario. This, Jones says, makes their company different from many competitors whose businesses are much more based on disposal, incineration and landfilling. They are also unique in the range of services they offer.
"We have lots of competitors in different parts of our business, but there is no one competitor for us that offers the breadth of services and integrated national scope that we do."
Creating award-winning closed loops for lead–acid batteries
According to Atkinson, through efficient, established, closed-loop recycling systems such as theirs, about 99 percent of all lead-acid batteries produced in North America are collected for recycling. Terrapure recovers over 80 percent of the valuable materials from each battery they collect - mostly lead and plastics. From those recovered materials, over 95 percent are exported back to large-scale battery manufacturers for use in making new products, almost all of which are in the U.S., and are the same companies that send Terrapure their used lead-acid batteries for recycling. It is as close to a 100 percent closed-loop model as it gets.
"Lead-acid batteries are a very valuable commodity," Atkinson says. "It's among the highest recycled waste in the world and is really an amazing recycling story."
Terrapure Environmental has won multiple industry awards since 2015 for their innovation, environmentally friendly practices, safety and community involvement. Earlier this year, they won an Environment and Energy Leader Award for their partnership with East Penn, their largest used battery supplier and end market for recovered plastic and lead. East Penn runs a site in Pennsylvania with about 8,000 employees manufacturing lead-acid batteries, and they have a solid, well-established recovery operation there.
According to Atkinson, "We have a really good relationship with East Penn and have for years. Basically, they collect batteries in their network all across North America. A large majority of the batteries collected, certainly all the batteries in Canada and a number of the spent batteries they collect from the northern U.S., come into our facilities - one in Mississauga and one in Ville Sainte-Catherine on the south shore of Montreal.
"It's really a beautiful system. It's all lead-acid batteries, predominantly auto batteries, which are transported up to our sites. We process them and recover more than 80 percent of their value.
"We send East Penn back the metal and plastics recovered from the batteries, and then they incorporate that material directly back into their processing. Because of this, they don't need a vast amount of costly, mined virgin material."
The price of recovered lead
There are really two market prices to consider in the lead-acid battery recycling business. One is associated with the purchase of spent lead batteries on the open market, and the second is the price for tolling of batteries whereby battery manufacturers arrange to collect batteries and send them to recycling plants to be processed for a fee. This is how it works between Terrapure and East Penn, for example.
"We employ both these methods to operate in an economically viable system," says Atkinson. "Tolling is a more predictable system, but does not cover all the batteries that need to be recycled in the marketplace."
Global lead pricing, as tracked by the London Metal Exchange (LME), was about 80 US cents/pound as of the start of October 2020. The one year trend (shown in the graph below) shows the price of lead fluctuated by about 30 US cents/pound over the year and had a number of peaks and valleys. According to Atkinson, this range of fluctuation has been fairly typical for lead over the last five years, but the price is very difficult to forecast as there are many influencing factors, including speculation, world economy, demand for lead and physical stock on the world market.
As of the start of October, the purchase price for lead-acid scrap batteries (essentially a commodity in and of itself) on the open market was about 53 US cents/pound, sold as metal, which Atkinson says, "really does not give us much room to process batteries and receive a reasonable return."
He adds that COVID-19 very likely impacted demand this year, as lead prices were notably low during shutdowns in the spring of 2020 and started to rise again when business started to return through July and August. More recently, since the start of September, the price has been dropping toward its lowest of the year.
"Although demand for lead in North America is reasonable at this time, it is likely that factors other than the pandemic, such as speculation and perhaps the U.S. election, will significantly impact lead prices through 2020.
We have to be very prudent in our purchasing and buffer the risk of the lead price dropping substantially."
Terrapure’s battery recycling process
Atkinson describes their process for recovering used lead-acid batteries, which come into their facility typically shrink-wrapped on skids. These are commonly piled in three layers, with between 50 and 80 auto batteries, with cardboard between each layer, at roughly 3,000 pounds per skid.
"Those are shipped in by transport trucks, received at our facility, weighed and segregated depending what type of battery they are," explains Atkinson. "Then at both our battery recycling facilities we use similar equipment for processing. We typically receive on what's called a battery tipper after we've weighed incoming material. It is tipped into vibrating conveyors and we have one picking station where there is a person that will remove any residual cardboard, shrink wrap plastic, non-conforming batteries [such as non-lead batteries] or any materials [such as stainless steel] that could harm our process."
Batteries are cut up into chunks with a shredder so they can be drained of acid. The drained acid is disposed of and they are left with what Atkinson calls the solids: comprised mainly of lead and plastic, which are then run through a high-speed fine grinding hammermill.
"The 1,800-rpm hammermill breaks a battery into very fine parts that we can then sort both by gravity and hydrodynamic separation, using water and density," he says.
From lead-acid batteries, there are two main types of plastics captured: polypropylene (PP) and polyethylene (PE). Terrapure recovers 100 percent of the polypropylene, washes it, prepares it and sends it back to the manufacturer where it is reintroduced directly into new batteries. Atkinson says the other plastic is a rubber and polyethylene blend material that holds in place a series of plates that the batteries are composed of. "That material is recovered, separated and used as auxiliary fuel in the battery manufacturers' smelting process."
Besides plastic, the solids of lead-acid batteries consist of two main types of lead.
What Atkinson calls the "gold" of the battery, the high-value lead, is about 92 percent pure. It's recovered from the posts, connectors and grid of a battery and comprises about 30 percent of the battery weight.
"Once this is separated, it's a very simple smelting operation to basically melt it down and recover it."
He describes the second lead component, called paste, as more of a challenge chemically. "It's lead oxide and lead sulfate paste, which is really the material that allows a charge to move back and forth through the battery."
In their smelting operation, they put recovered paste into 1,100-degrees Celsius rotary type furnaces and add iron, soda ash and coal. "That basically pulls any of the non-lead or non-metallic material out of the paste," continues Atkinson. "Mostly it's sulfur."
The smelting process also results in a metallic intermediate metal (about 95 to 96 percent lead mixed with minor metals including tin, antimony and selenium). This intermediate metal from the furnaces is run through a further series of refining stages to remove any remaining fine metals, to make finished, pure product (about 99.97+ percent pure). Or, sometimes the mixed minor metals in their lead are retained if they are making a custom-specified lead for a customer.
According to Atkinson, the lead refining process is something like baking. "We use oxygen and various chemicals, mixed with lead at different processing temperature to refine the lead. We end up with beautiful, 2,000-pound blocks of pure lead, or 65-pound ingots. We're shipping out a massive amount of this product, direct to battery manufacturers."
He emphasizes that the output of their lead is very close to 100 percent pure. "It really looks beautiful and has crystals on top of it. It looks so nice that in the past thieves have stolen it because they thought it was titanium or something extremely valuable.
"They end up stealing it and it's sitting in a transport truck and then they realize what it is and they don't know what to do with it, and it'll cost just as much to remove it. Granted, as lead prices have gone up, it's becoming more of a valuable commodity."
Changing times, changing waste for good
In part because their battery recycling business relies on regular, consistent cross-border transactions, COVID-19 has posed some extra challenges for Terrapure this year. Recalling this past spring Atkinson says, "Batteries were not being collected, nobody was driving cars and so the business kind of came to a halt.
"The good thing is that our industry, both our clients and ourselves, really adjusted well in terms of putting up all the protocols to manage COVID-19. We really have got back rolling, and starting in July and August the industry has basically come right back.
"We're not out of the woods, of course," Atkinson adds. "Everybody continues to be extremely diligent and concerned, but business is rolling again."
Going forward, he says they face a few other notable challenges, including ongoing safety issues with lithium-ion batteries in their incoming streams.
Safety is a top priority for Terrapure, and according to Atkinson, compared to the explosion hazard related to lithium-ion batteries, lead-acid batteries are relatively very safe to process and have only a remote chance of causing a fire (via short if two live batteries are packaged with the opposite poles touching). Lithium-ion batteries, however, can cause a violent reaction, and it remains one of their largest safety hazards.
"They get mixed in with our materials, which is why we've got people watching very carefully to make sure lithium-ion batteries do not enter our breaking process," says Atkinson. "There is potential for explosions."
He relates one cautionary tale about a recycler in the U.S., where they reported having a 1,000-pound steel door blown off of their hammermill, 100 feet across their plant, due to a lithium-ion battery explosion.
"Our industry right now is trying to negotiate with the lithium-ion manufacturers to create a battery that is noticeably different, either in colour or some other way, so we can better handle the risk," Atkinson says, adding that they are also developing a lithium-ion detector in-house for their plant so they can make sure none get through.
"That's in the works. I don't know how quickly it will happen, but I would say in the next three to five years, we will have something in place."
Another major challenge for Terrapure currently has to do with their international competition operating at low costs due to a disparity of regulatory complexity for recycling lead-acid batteries between North America and many countries.
"In North America it's no longer necessarily a level or balanced, competitive playing field between us and some global operations," comments Atkinson. "Here we have extensive resources for protection of the environment and our workers, and have spent a huge amount of money on that at our operations. But in probably the last five years there's been a greater and greater amount of shipping of batteries offshore.
"Some offshore operations are certainly not modernized or regulated like ours and so their cost structures are much less demanding. North Americans are able to export used batteries at a very low cost, and that's started to create a concern for our industry in general and for ourselves."
Atkinson continues, "It goes against the principles about what we should be doing in Canada, which is firstly handling our own waste. It also could in the long run affect our viability if we're allowing less regulated competitors to operate at low cost."
Because we operate in a world economy, he adds that it would be unreasonable to suggest that all lead-acid batteries be kept within North America. However, Atkinson says, for this type of lead-bearing material, a standard of environmental protection, and health and safety practices that protect workers and community should be verified for any lead-acid batteries exported.
"In North America, the standard of operations are very good, regulatory controls are strict, and all operations must allocate substantial financial resources to continually improve on environmental protection and worker/community protection," he continues. "While I am not an expert on worldwide operations, if one thinks about the off-shore process, there are a number of practices starting from shipping the batteries across the ocean, transferring them to mainland routes and processing them in non state-of-the-art faculties offshore that may be putting the environment and people at risk. Fundamentally, the most effective way of managing waste materials is to manage them at source so that impacts on community are always considered carefully, and a continuous upgrading to better and better practices is encouraged."
Greg Jones concludes by reflecting on Terrapure's mantra: Changing waste for good. "This, for Terrapure, is both a mantra and a vision, in terms of being what we aspire to and what we in fact do today," says Jones, adding that their battery recycling business is the best example of this mantra. "All waste streams are revenue streams. That's really important these days because the definition of waste is changing for many, and many are realizing that the materials they are dealing with are not waste, but a resource. We're seeing government policy slowly move more in this direction in Canada. Certainly, in Europe it's more advanced.
"At Terrapure, we feel like we're in a really good space and that the differentiation that we've been able to carve out between us and some of our competitors will really serve us well as society pushes more and more to a resource recovery-focused approach to waste."
Company info
1100 Burloak Drive Ste. 500 Burlington, Ontario L7L 6B2 905-315-6300
Burlington, ON
CA,
Website:
terrapureenv.com