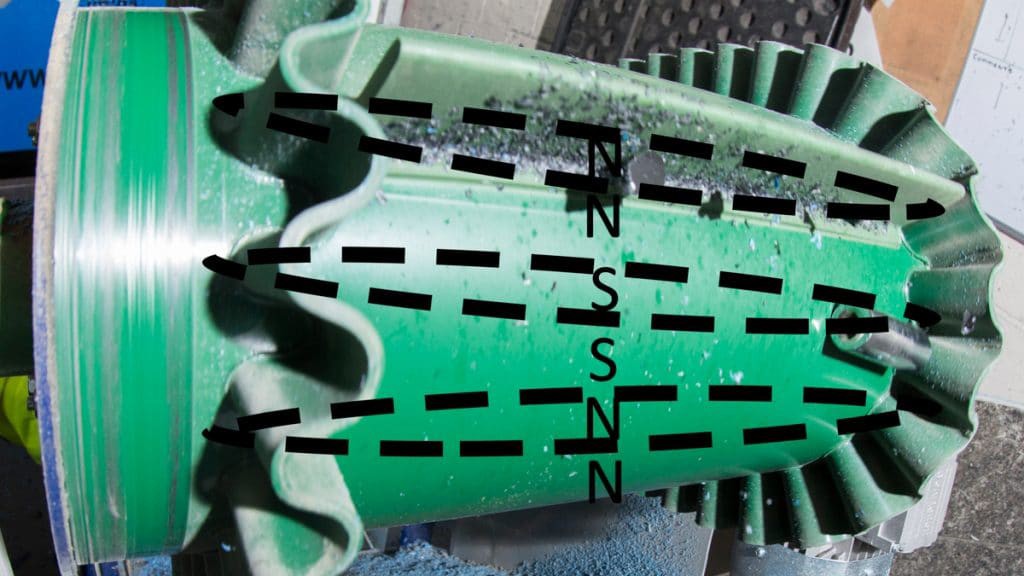
Bunting manufactures several varieties of magnetic separators classified as rotary magnetic separators, including a drum magnet.
Rotary magnetic separators are designed with a specific type of magnetic field, which is considered when evaluating an application in order to decide which design will best achieve a customer's separation objective.
For rotary magnetic separators, there are two types of magnetic field: axial and radial. Below is an explanation of axial and radial magnetic fields, as well as why the differences between the two are so important.
Axial magnetic field
Axial magnetic fields stretch across the width of a rotary magnetic separator. When magnetically susceptible material enters the field, it is attracted to the point of highest magnetic intensity —known as the pole— but then, the motion of the conveyor or drum drags the material through a weaker area of field located between the two poles before it eventually settles onto another pole.
An axial magnetic field is ideal in situations where the magnetic separator may have captured a high level of entrapped non-magnetic material. Because of the motion of movement between the poles, non-magnetic material will be released as the magnetic item "tumbles" in the field. The downside of this type of magnetic field is that there is the potential for reduced separation performance.
An axial magnetic field is best for applications where the separation objective is to maximize the purity of the recovered ferrous metal. An example of an application that may prioritize the purity of recovered material is an auto recycling application where the purity of ferrous material recovered is essential in determining its resale value. This is because the "tumbling" effect is able to release entrapped non-magnetic material. However, this means that recovery rates of ferrous metals may be slightly lower.
Typically, magnetic separators using an axial field can be found recovering ferrous metal from recycling operations. Bunting products that can utilize axial magnetic fields include permanent drum magnets, electro drum magnets, and pulley magnets.
Radial magnetic field
In a radial magnetic field, poles are running in the same direction that the conveyor or drum is rotating, and follow the flow of the material. Magnetically susceptible material will be attracted to the poles, which are the highest points of magnetic intensity, and held there until it is dragged out of the magnetic field.
A radial magnetic field is ideal when the goal is to maximize the amount of magnetic metal being separated from material. An example of an application that may seek to separate the maximum amount of magnetic metal is in a mineral application where ferrous tramp metal must be removed from the product stream, so as not to contaminate the product. The downside of a radial magnetic field is that it is possible for entrapment of non-magnetics to occur, which then reduces the purity level of the recovered metal that is ultimately separated out.
Magnetic separators with radial magnetic field design are typically found in applications such as recovering magnetic minerals in mineral processing, and also applications such as removing ferrous metals in certain recycling applications.
Bunting products that can utilize radial magnetic field design include drum magnets, pulley magnets, rare earth roll separators, and induced magnetic roll separators.