Manufacturers share best practices for COVID-19 management
AEM has developed a list of best practices based on what member companies are doing to keep operations open
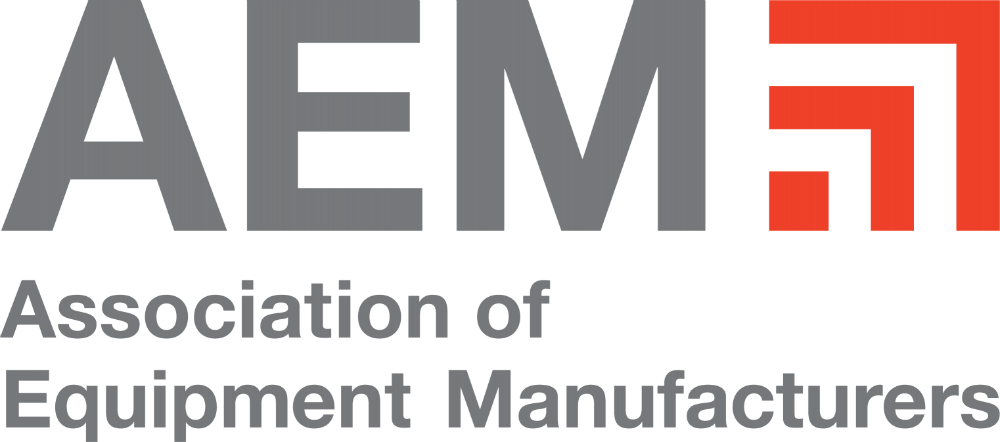
AEM has developed a list of best practices based on what member companies are doing to keep operations open while minimizing the risks associated with the COVID-19 pandemic.
For those looking to either reopen or scale back their operations in the coming months, here are some of the actions and initiatives that can be implemented and shared with suppliers and partners to help ensure a successful transition.
Managing risks
- Understand your shift population to determine how many employees can work in a designated area while staying 6 feet apart. How many of your employees can safely practice social distancing throughout the workday? This includes looking at all facilities and thinking through areas, such as entrances and exits, elevators, stairways, meeting rooms, lunch rooms and break areas, locker rooms, etc.
- Plan for appropriate personal protective equipment (PPE) and the amount needed of each for your manufacturing facilities and office environment. This inventory includes masks and may also include proper gowns and face shields.
- Make sure all employees working onsite have travel permits/letters from the company so they can travel to work per the essential business rulings. It is important to be aware of regulations and rulings of each state or province where there are operations.
- Provide guidance on employee and public transportation to keep employees safe and protect them from bringing the virus to work and home. This requires reminders of social distancing and disinfecting their seating area on buses and trains, tips for disinfecting cars and motorcycles, as well as avoiding carpooling and sharing rides.
- Implement thermal screening at entrances to minimize spreading the virus. This can include adding walk-through temperature scans for manufacturing and office employees. Individuals identified as having a positive temperature should be sent to a medical area either onsite or at an offsite location for further testing.
- Set up teams and hold daily leadership meetings to share information and make needed decisions from the top. Set up appropriate teams to focus on key business areas and have these teams connect daily. Teams can focus on areas such as COVID-19 preparedness, business continuity, operations, internal communications, community relations/public relations, etc.
Onsite facility, office procedures and space planning
- Set up procedures for entrances and exits to help employees manage opening doors and passing others in hallways and on staircases. This includes adjusting to allow only one person to enter/exit at a time, creating visual signs for social distancing and providing nearby hand sanitizers. Adding foot pulls and forearm pulls to allow for easy, hand-free door openings will help to avoid touching door surfaces.
- Map out traffic patterns such as stairways, hallways and shop floor common areas to keep employees on track for social distancing. Providing physical cues to show traffic patterns on stairs and allowing only one person per elevator are helpful. Some stairways can be designated for only up traffic and others for only down traffic. Adding floor markings to indicate where individuals can stand during production meetings, clearly showing walking areas on the shop floor and using signage in different languages for your employee base all can be helpful.
- Implement distance checks and adjust office areas to keep office employees sitting at a safe distance from their neighbors in cubes and in desks. Make sure chairs are stationed 6 feet apart in conference rooms and capacity numbers are prominently displayed. Dividers or walls should be installed for open concept areas and adjustments may be needed to use new spaces for desks. Map traffic patterns in the office areas using tape or floor markings to divide hallways and indicate walking direction as needed.
Hygiene and disinfection
- Train staff on proper hygiene procedures and expectation to minimize infections. Clean down and wipe all surface areas during a change in shift or workforce. This includes anything touched, such as handles, doorknobs, clipboard, pens, keyboard, monitors, etc. It is important to have clear signage reminding staff to wash hands, wipe down areas and to use hand sanitizer. Discontinue use of drinking fountains and/or provide no-touch water bottle filling stations and close off common areas that are not to be used during this time.
- Show videos of proper hygiene and area cleaning techniques to reinforce expected procedures. Station monitors showing videos in areas to inform employees of expectation and cleaning techniques in break or cafeteria areas.
- Ban community and shared food to promote a healthy working environment and guard against the virus spreading.
Communications
- Provide ongoing and frequent communications with all staff, even globally, so leadership can communicate directly with employees, address rumors and share facts. This improves engagement and productivity among employees, including those currently working onsite, those working remotely and/or those furloughed.
- Eliminate all non-essential meetings and conduct essential meetings and trainings online via electronic media options such as WebEx, GoToMeeting, Google Hangouts, etc. Make sure your IT team provides guidance to employees on the best tools for your organization and how to use those tools effectively.
- Promote wellness via texts and social media to encourage employees to change their personal behaviors that make them more susceptible to contracting COVID-19. Frequent communication using social media and texting alerting systems can provide needed hygiene reminders and company announcements and new procedure implementation.