TRS plant providing efficient metal separation from incinerator bottom ash
Downsizing, liberation, fractionizing and a well-organized process increasing metal recovery for IBA processor
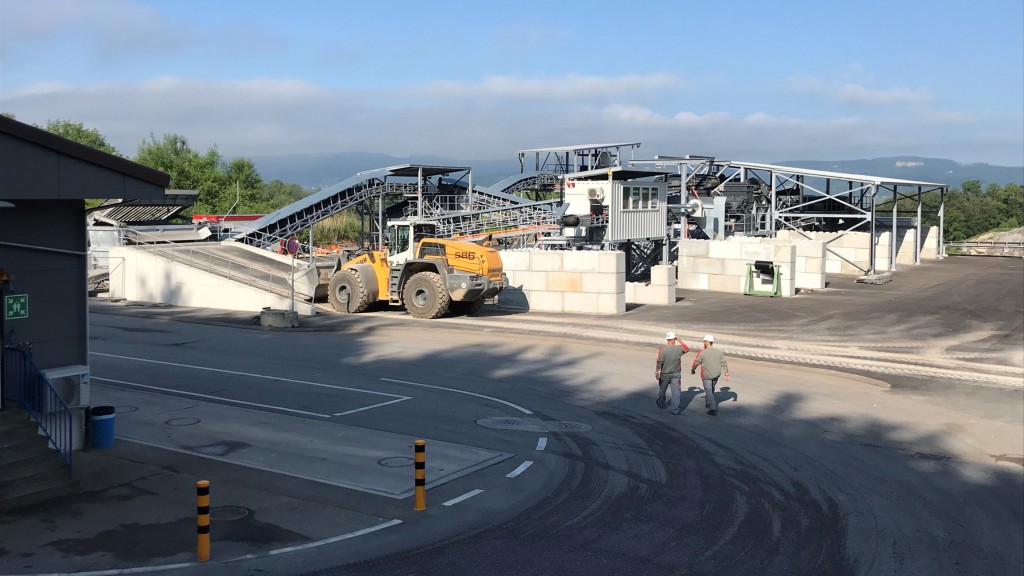
In the summer of 2019, Netherlands-based manufacturer TRS BV delivered a complete, newly built Incinerator Bottom Ash (IBA) Treatment and Metal Recovery plant to AIB, near Basel, Switzerland. The new plant is treating IBA material coming from the nearby Basel incineration plant, located at the waste management facility, Deponie Elbisgraben, in Liestal.
According to TRS, before IBA-material is landfilled, it is crucial to regain as many metals as technically possible such as ferrous, non-ferrous and stainless steel.
The process in Basel has been developed between three parties, AIB, TRS BV and Prof. Dr. Bunge (Hochschule für Technik Rapperswil), a Swiss expert regarding the subject of processing IBA-material. The goal on this project is to downsize, liberate and clean all IBA material to an end-fraction of < 5mm, and to recover as many metals as technically possible, and render materials suitable for disposal. In Switzerland it is prohibited by law to use IBA-material e.g. for road construction and/or other applications, and landfills require a prior separation of metal and IBA-material. Landfilled material must not contain a maximum of more than 1 percent non-ferrous metals. The new plant achieves a value under 0,22%.
A healthy and logical process-flow
The unprocessed and pre-conditioned IBA-material is loaded into a bunker where the +250 mm is separated by a tilting grid. Afterwards the 0-250 mm fraction is sieved at 40mm, the 40-250 mm fraction continues to an electromagnet and manual sorting cabin for recovery of ferrous, non-ferrous, stainless steel, copper coils, unburned and mineral components.
The 0-40mm fraction is further sieved at 5 mm, creating a 0-5 mm and 5-40 mm fraction to render possible an optimal metal recovery by the latest material spreading and metal recovery techniques. These techniques such as active clean vibratory feeders, low intensity magnetic separation and high intensity Eddy Current separation make sure a maximum recovery of metals is achieved. Directly after sieving, the 5-40mm fraction is first treated by an electro over band magnet taking out clean ferrous and then processed by an active clean vibratory feeder to allow a perfect wide distribution of the material.
Afterwards the Eddy Current recovers the non-ferrous metals which are directed towards the metal storage bay. The remaining mineral fraction of this Eddy Current is forwarded to an impact crusher, liberating more metals that are bound with minerals and cleaning the stainless steel fraction that is not separated by the conventional magnets and Eddy Current. The crushed material is then looped back into the 5 mm sieve and finds its way back to the non-ferrous metals separation stages.
The stainless steel parts, mainly sized between 5-40 mm (including bigger pieces such as forks, spoons and knives) travels through the plant until being released into a container by a reversing conveyor belt.
The 0-5 mm fraction is separately forwarded into a "waterfall" distribution and separation set-up, consisting of an active clean vibration feeder for perfect wide distribution of the material to ensure the best possible separation efficiency, both on the low intensity magnetic separator module and in the 2.000 mm wide high magnetic density and frequency Eddy Current separator.
In the end a clean and downsized IBA fraction exits the plant and goes to landfill. The overall input capacity of the installation is 30T/hr. The metal separation is very efficient at times even achieving better values than 0,22% of non-ferrous metals in the 0-5 mm end product. The ROI comes totally from the metal recovery. The installation will be running and exploited for the next 10 years to come.
IBA Treatment facilities
In general there are many ways to process incinerator bottom ash (IBA) materials into re-usable IBAA aggregates and recycled secondary metal fractions. IBA downsizing, metal liberation and material fractionizing are healthy ways to follow and to connect your process to that type of thought. Every situation is different in relation to legislations, material types, pre-processing, type of incineration, material storage, et cetera. TRS BV is able to make a quick inventory of the situation and adapt to the local and necessary issues. With these features taken into consideration, often a very pragmatic, simple and as a result of that, economically feasible project will arise.