Sennebogen E-Series 855 M Hybrid first to arrive in North America
Scrap handlers helping to build capacity and reliability for Nucor
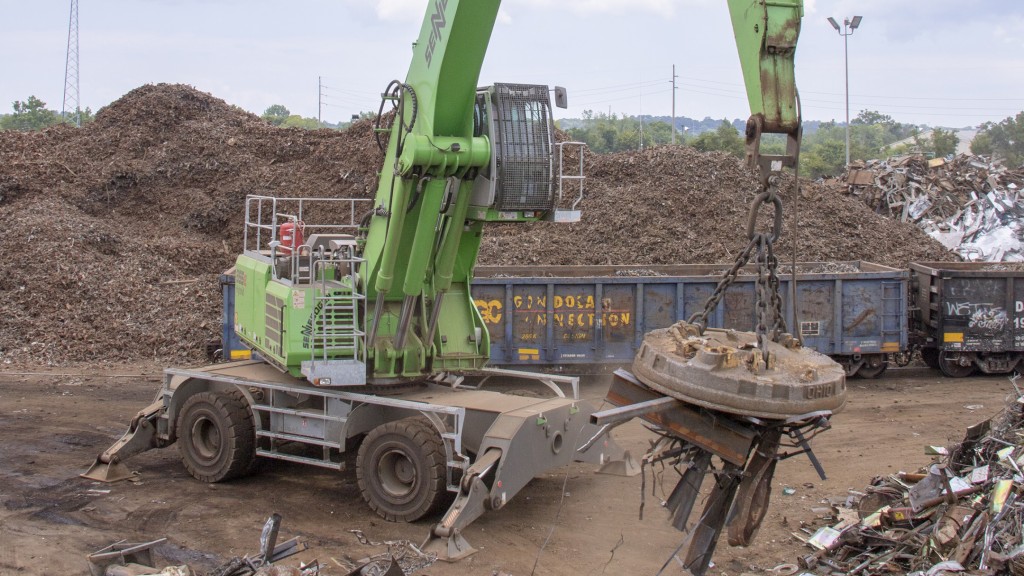
Space is at a premium at the Nucor scrap yard in Birmingham, Alabama. Three Sennebogen scrap handlers are proving themselves very valuable in helping the company move close to 4,000 tons of scrap per day in total to feed a nearby melt shop.
"It's pretty intense" according to Amy Alford, Scrap Yard Supervisor and Brandon Keller, Scrap Yard Lead. "It's 24/7. We can't afford to have downtime."
Between them, they oversee the unloading and loading of 40 to 50 trucks plus 15 rail cars every day. "We're melting everything we take in every day," Alford says. "The rail cars are basically our storage. If we get 15 in one day; they have to be ready to be picked up the next day. And if they aren't unloaded, we're getting charged for them."
To keep the material moving, the yard is operating three purpose-built material handlers. The latest addition is SENNEBOGEN's new E-Series 855 M Hybrid machine, the first to arrive in North America. Nucor purchased the steel mill here in 2002. The scrap processing operation was contracted out at that time, but Nucor took over the yard in 2007.
Building capacity
On duty around the clock, two of the material handlers, equipped with grapples, typically log 12 to 17 actual operating hours each day. The third machine is fitted with a magnet and generally works lighter hours. The 855 is planned to take on the heavier workload but, at this time, it has taken over for the material handler equipped with the magnet while one of the older machines is out of service. Alford explains: "We want to add a 4th machine, in order to give us the time for proper service."
Focus on uptime
Equipment reliability is crucial to such a tight operation: "If we aren't running, the melt shop isn't making steel," Keller says. "One of the things we really looked at when we were buying was the accessibility for maintaining the machines. You could count on my hands the number of times we have cost the melt shop even 30 minutes downtime in my 17 years here."
"I tend to look most closely at the maintenance side of things. I try to make it easy on the crew. This SENNEBOGEN is a lot simpler to work on than the other machines. Technicians were working down in little tiny holes and really fighting to put parts on and replace things. With the 855, everything is ‘right there.' I think we'll also see a cost reduction in basic service parts. I'm a big fan of these Cummins engines. Starters and alternators and such are a fraction of what they cost on the other machines."
What's a "Hybrid"?
The 855 is one of SENNEBOGEN's new-generation machines, featuring the unique Green Hybrid energy recovery system. According to Alford and Keller, "We wanted to do the right thing for the environment. These machines really help our numbers."
Green Hybrid models are easily recognized by their large energy recovery cylinder, mounted between the two hoist cylinders on the lifting boom. On every downstroke of the boom, this oversized hydraulic cylinder captures the energy produced by the lowering action, and stores it in compressed nitrogen cylinders located in the rear of the machine. The stored energy is then used during the next upstroke to supplement the hydraulic power that lifts the load. The system performs best in operations that cycle frequently through up and down strokes. In these operations, the system can reduce energy costs by as much as 30%.
SENNEBOGEN developed the Green Hybrid concept using standard hydraulic components, so service staff can support the technology with their existing skills and parts. Initially introduced on larger models used in port facilities, the 157,000 lb. (71,000 kg) E-Series 855 is the smallest in the SENNEBOGEN line-up to offer Green Hybrid emissions and fuel savings.
"So far, so good!"
The 855 M is Alford's and Keller's first hands-on exposure to SENNEBOGEN equipment and they're pleased with what they have seen in its first months of operation. "We were looking at other machines; looking to what was available for an early delivery. Robert (Boehme) from the Tractor & Equipment Company has been coming in here for years, really putting the effort into getting the sale for SENNEBOGEN. We didn't really get that from anyone else so, for all the right reasons, we thought we'd give it a try."
Operators at the site are on-board with the decision, too. Keller notes that new operators recruited to Nucor recently were familiar with SENNEBOGEN at previous locations, and are happy with improvements in the E-Series models. "This is a really smooth machine to handle," Keller reports, "They say it's not bouncing them all over the place every time they load a bucket or unload a rail car."
While the yard staff was waiting for delivery of the 855, Boehme arranged for his customer to attend technical courses at SENNEBOGEN's Training Center near Charlotte, NC. "That is a really nice facility," says Keller. "Two maintenance guys attended the service training, and we also brought one of our operators so he can help out with some of service. And I went along also. We're really lean. We run with as little as possible. The training we received was unbelievable; as a company, we were very pleased with what we saw there."