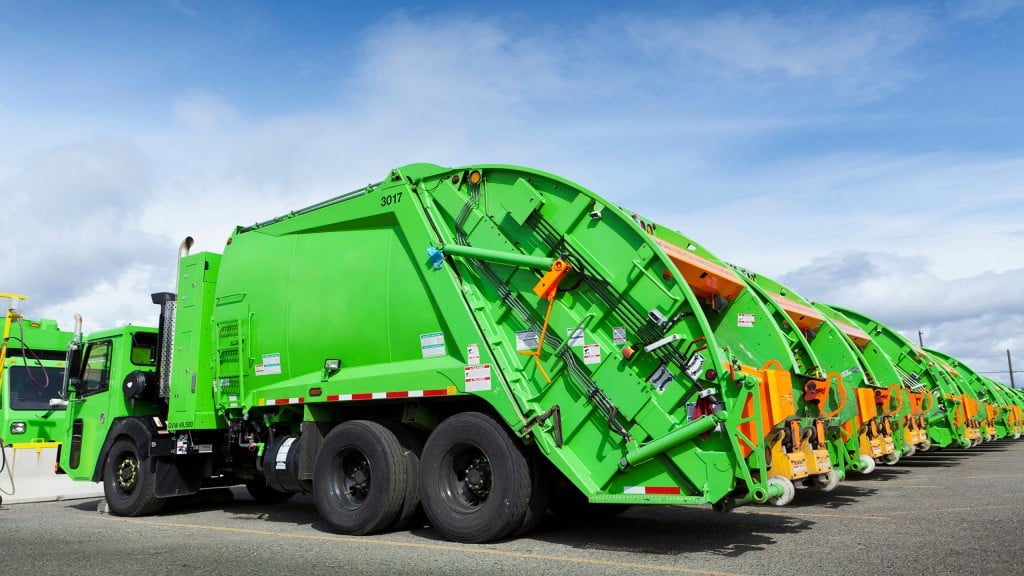
Heavy-duty diesel vehicles that collect and transport waste and recyclables in urban environments, and which work at transfer station sites, material recycling facilities (MRFs) scrapyards and landfills, operate under tough conditions. In these settings, fleet managers are required to maintain high levels of monitoring on specialized vehicles to ensure optimum performance and safety of their employees.
Constantly stopping and starting, waste fleets work in unique conditions where there is often a wide operating temperature range. These varied environments can result in increased engine wear - resulting in unplanned maintenance and downtime. This, combined with heavy loads that further accelerate engine wear, can significantly impact a business' bottom line, where every day a vehicle is down can result in lost revenue. For waste fleet managers, selecting the correct lubrication is crucial for ensuring the protection of vital engine components to prevent unscheduled maintenance and breakdowns.
A closer look at the role of heavy-duty engine oils
Before considering the factors that influence lubricant choice for heavy-duty vehicles, it's good practice to understand the crucial role that engine oils play in vehicle maintenance.
Reducing pumping and spinning losses as well as minimizing frictional losses between moving components, heavy-duty engine oils protect engine components while improving fuel economy and reducing viscous drag.
Supported by the move to lower-viscosity oils, newer engine oils reduce frictional resistance and drag in the engine even further. Simply put, this means that the engine does not have to consume as much fuel or work as hard to provide the same level of power. This allows the engine to run more efficiently and offer improved levels of wear protection, and helps improve fuel economy, which in turn reduces carbon emissions.
What to consider when selecting a lubricant
Evolving industry legislation and heavy-duty engine oil technology means that selecting a lubricant can be challenging. So, with an abundance of oils available, what factors should be considered before making a choice?The first step should always be to consult the Original Equipment Manufacturer (OEM) vehicle manual or contact the company directly for information and advice.
Following this, the fleet and its operating conditions should be considered - a particularly important factor for the heavy-duty equipment used in the recycling industry where the use of stop/start technology is common. For this type of technology, it is important to use a more durable lubricant that can provide protection during the engine's high number of on/off cycles.
Also, for newer engines that run at higher temperatures, a conventional lubricant that suffers from an accelerated rate of oxidation and degradation under these conditions would not be the most suitable solution. Recent innovations, such as oils that meet API CK-4 or FA-4 standards, should be utilized as they offer greater resistance to oxidation and improved aeration control and shear stability.
As part of this process, operators should examine their region and climate. Fleets operating in warmer climates will have different oil requirements to fleets in the colder regions of Canada and the northern U.S. Oils that are designed to provide protection in colder temperatures have a ‘W' (which stands for winter) on the container, which features after the SAE (Society of Automotive Engineer) grade.
For those fleets in warmer areas, a heavier oil such as an SAE 30 or 40 grade would be more suitable - these resist the breakdown associated with high temperatures and ensure proper flow and engine protection.
The oil's viscosity dictates its ability to flow. In cold conditions, if the oil's viscosity is too high it may resist easy movement, delaying the lubrication and protection of the engine resulting in increased engine wear. Oils that meet industry standard tests such as Cold Crank Viscosity and Low Temperature Pumpability provide peace of mind that the oils will lubricate critical components, even in the coldest of operating conditions.
Because, there are a multitude of factors to consider, it's always important to seek OEM and expert lubricant advice and recommendations ahead of changing the type or grade of engine oil used.
The benefits of used oil analysis
Due to the number of factors involved, including the extreme conditions in which waste vehicles operate, incorporating a used oil analysis program can prove to be very beneficial. The process itself is typically comprised of three steps:
-Take a representative sample - this is the most important step in the process as improper sampling can lead to inaccurate interpretation of the results and potential equipment damage or failure. A clean, dry container suitable for oil analysis should be used, and the sampling point should be wiped with a rag before a small amount of oil is flushed to ensure no foreign contamination makes its way into the bottle.
-Send sample to a qualified used oil analysis laboratories - once the sample has been taken, it should be sent as soon as possible to an oil analysis lab certified to perform the testing required. The lab will test the oil using standard test regimes, providing accurate results and diagnosis in a report that can be sent by email or viewed online.
-Interpret used oil analysis results - this is when technical advisors take stock, evaluate the results and provide recommendations on whether it is possible to extend oil drain intervals.
A worthwhile investment, used oil analysis can highlight minor maintenance problems before they become serious and expensive to repair. This helps improve fleet reliability while also minimizing maintenance costs and unplanned downtime. In addition, used oil analysis programs can help to determine oil drain intervals to ensure that the optimum performance of the oil and protection of vital engine components.
Selecting a heavy-duty lubricant for a fleet operating in unique, extreme conditions can be a challenging task. By seeking expert advice and following OEM manual recommendations, superior engine protection can be achieved, resulting in increased fleet reliability and less unplanned downtime. RPN
Brian Humphrey is OEM technical liaison, Petro-Canada Lubricants.
This article was originally published in Recycling Product News, September 2018, Volume 26, Number 6.
Company info
2310 Lakeshore Road West
Mississauga, ON
CA, L5J 1K2
Website:
www.lubricants.petro-canada.ca